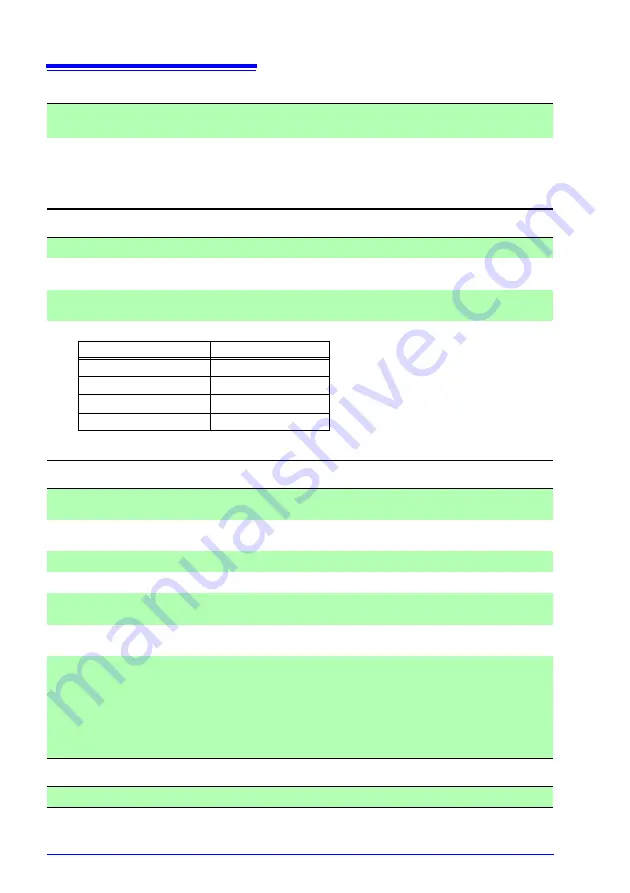
Chapter 13 Specifications
256
(2) Resistance D/A output accuracy
(3) Temperature measurement accuracy (Thermistor sensor)
(4) Temperature measurement accuracy (Analog Input)
(5) Calculation order
Output accuracy
Resistance measurement accuracy ±0.2%f.s.
(temperature coefficient ±0.02%f.s./°C)
Response time
Measurement time + Max. 1 ms
Shortest
2.0 ms (tolerance: ±10%±0.2 ms)
Shortest conditions
INT trigger source, LP: OFF, 1000 k
Ω
or lower range,
Measurement speed: FAST, Delay: 0 ms,
Self-Calibration: MANUAL
Measurement range
-10.0 to 99.9°C
Measurement period
(speed)
2 ± 0.2 s
Period of guaranteed
accuracy
1 year
Combined accuracy with Model Z2001 Temperature Sensor
Guaranteed accuracy
range
0 to 2 V
Maximum allowable
voltage
2.5 V
Resolution
1 mV
Display range
-99.9 to 999.9°C
Measurement period
(speed)
50±5 ms, no moving average
Period of guaranteed
accuracy
1 year
Accuracy
±1%rdg. ±3 mV
Temperature accuracy conversion method
1% × (T
R
−
T
0V
) + 0.3% × (T
1V
−
T
0V
)
T
1V
: temperature @ 1-V input
T
0V
: temperature @ 0-V input
T
R
: current temperature
Add temperature coefficient (±0.1%rdg. ±0.3 mV)/°C to above accuracy for
ambient temperature ranges 0 to 18 and 28 to 40°C.
1. Zero-adjustment 2. Temperature correction 3. Scaling
Accuracy
Temperature range
±(0.55 + 0.009×|t -10|)°C
-10.0°C to 9.9°C
± 0.50°C
10.0°C to 30.0°C
±(0.55 + 0.012×|t -30|)°C
30.1°C to 59.9°C
±(0.92 + 0.021×|t -60|)°C
60.0°C to 99.9°C
t : measurement temperature (°C)
Accuracy of instrument alone: ±0.2°C
Summary of Contents for RM3545
Page 2: ......
Page 4: ......
Page 26: ...Operating Precautions 18...
Page 42: ...1 5 Checking the Measurement Target 34...
Page 54: ...2 6 Pre Operation Inspection 46...
Page 70: ...3 5 Checking Measured Values 62...
Page 226: ...10 6 Supplied Connector Assembly 218...
Page 290: ...Chapter 13 Specifications 282...
Page 312: ...14 4 Disposing of the Instrument 304...
Page 349: ...Appendix 18 Outline Drawing A37 Appendix Appendix 18 Outline Drawing...
Page 362: ...Index Index 4...
Page 363: ......
Page 364: ......