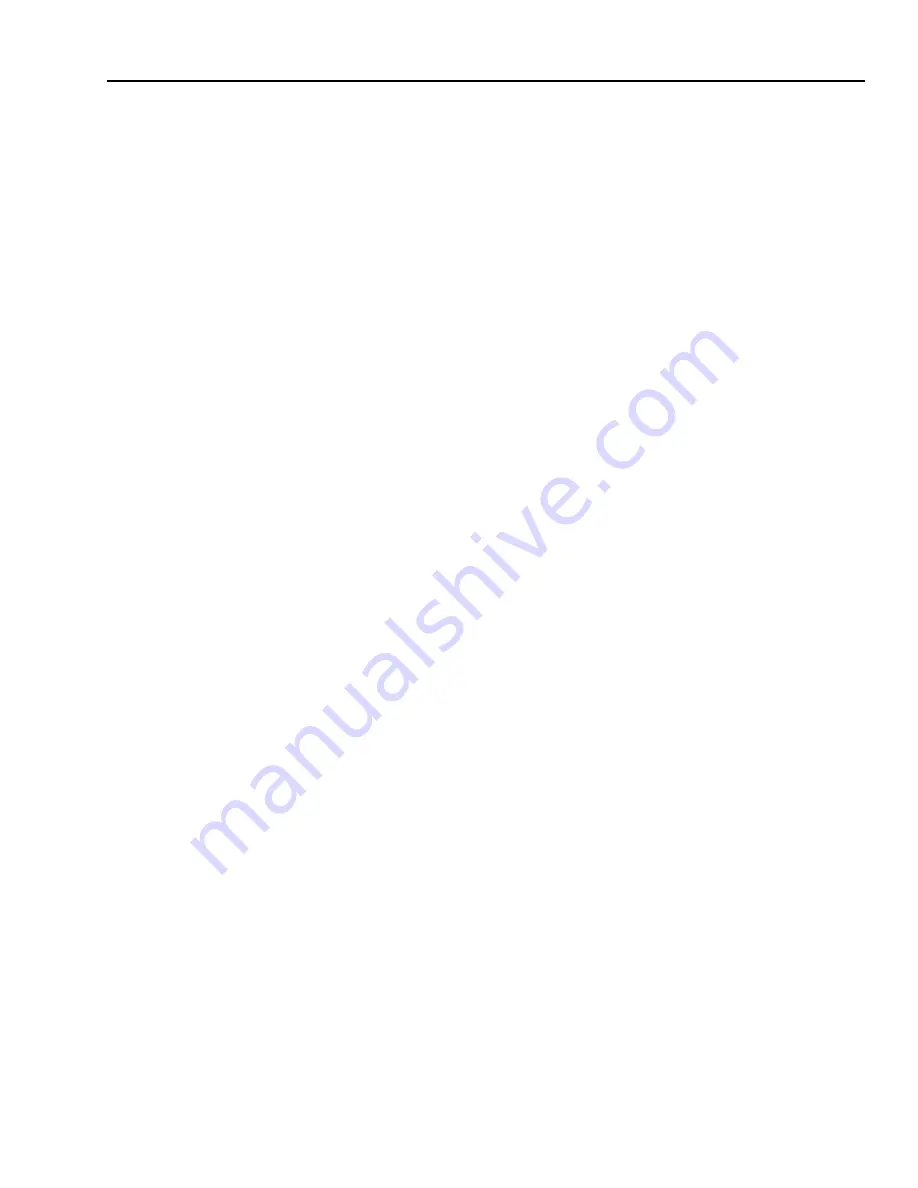
Chapter 3 - Installation
3-1
CHAPTER 3 - INSTALLATION
About Chapter 3
All information contained in Chapter 3 pertains to unpacking, cabling,
interconnecting and installing the HI 2160RC
PLUS
rate controller. Alter-
natives to any specifications contained or implied in this section are not
recommended. It is very important that the user and service personnel
be familiar with the procedures contained in this chapter, before install-
ing or operating the HI 2160RC
PLUS
rate controller.
Unpacking
Step 1. Before signing the packing slip, inspect the packing for dam-
age of any kind.
Step 2. Report any damage to the carrier company immediately.
Step 3. Check to see that everything in the package matches the bill
of lading. You should normally have:
•
1 - HI 2160RC
PLUS
instrument with mating connectors
installed.
•
1 - Mounting Rail Kit (Prt. # 0551-0287-01)
4 - mounting Rails
4 -6-32 UNC phillips panhead machine screws.
1 - Installation and Operation Manual
NOTE:
The HI 2160RC
PLUS
comes in two configurations: Panel Mount and Remote Mount.
Depending on the configuration purchased, some additional hardware such as rack
mounts may be included.
Step 4. If any items are missing, damaged, or there are any questions,
please contact Customer Support at:
Hardy Process Solutions
10075 Mesa Rim Road
San Diego, CA 9212
1
Phone: (858) 278-4900
Web Site: http
s:
//www.hardy
solutions.com
Customer Support e-mail:
hardy
support@hardy
solutions.com
Step 5. Record the model number and serial number of the Rate Con-
troller. Store in a convenient, secure location for
reference when contacting
Hardy Process Solutions
Customer Service Department or to buy parts or firmware
upgrades.
Summary of Contents for HI 2160RC PLUS
Page 1: ...HI 2160RCPLUS Rate Controller Operation and Installation Manual ...
Page 23: ...HI 2160RCPLUS MANUAL 2 6 ...
Page 49: ...HI 2160RCPLUS MANUAL 3 26 ...
Page 67: ...HI 2160RCPLUS MANUAL 4 18 ...
Page 91: ...HI 2160RCPLUS MANUAL 5 24 ...
Page 151: ...HI 2160RCPLUS MANUAL 7 12 ...
Page 187: ...HI 2160RCPLUS MANUAL 8 36 ...
Page 207: ...HI 2160RCPLUS MANUAL 9 20 ...
Page 219: ...Data Worksheets WKSHT 6 ...