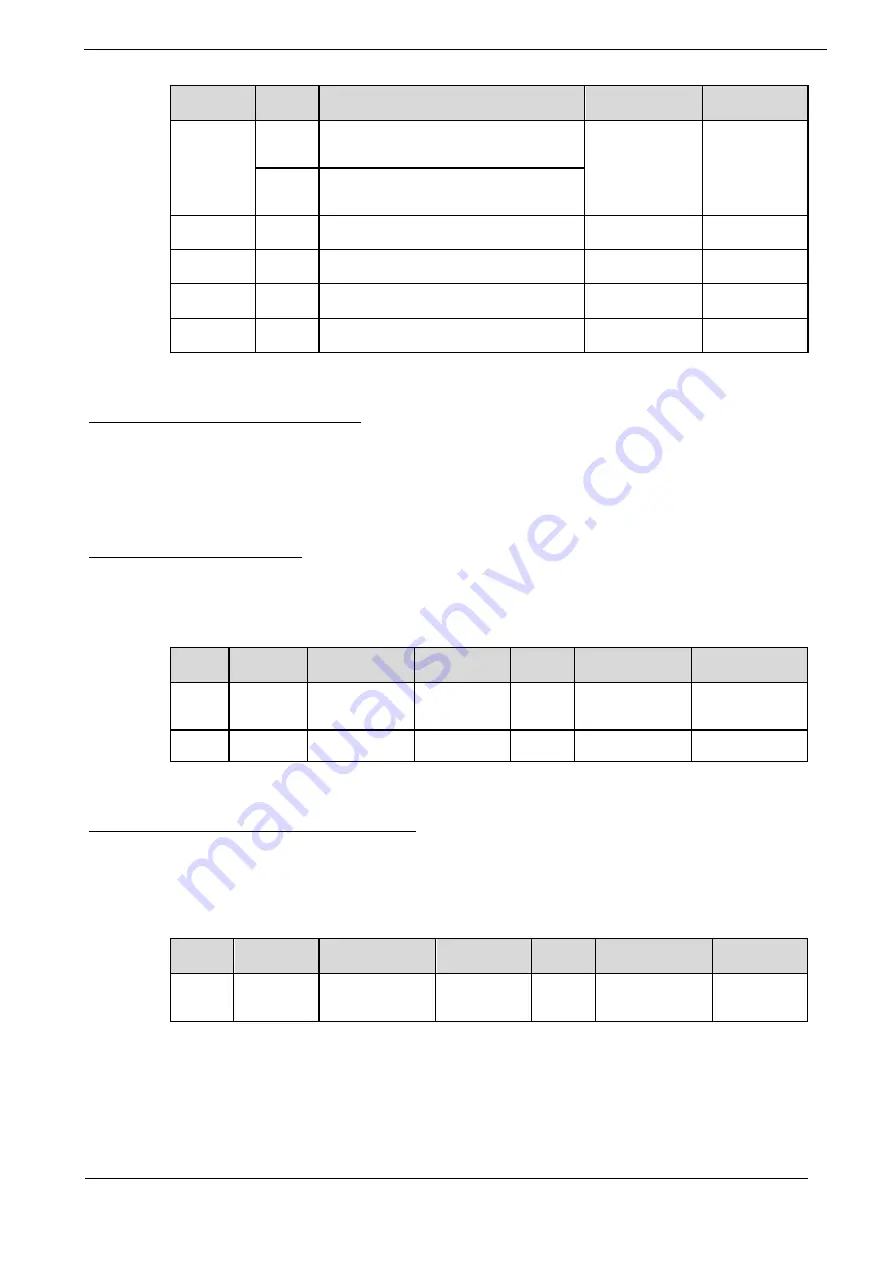
Summa Series Servodrive Product Manual
Tuning
Document Version: V1.01
(Dec, 2019)
© 2019 ESTUN Automation Co., Ltd. All right reserved.
9-33
Parameter Setting Meaning
When Enabled Classification
Pn005.0
0
Use the general internal torque
feedforward.
After restart
Function
2
Use the high-speed internal torque
feedforward.
Pn112
-
Speed Feedforward
Immediately
Adjustment
Pn113
-
Speed Feedforward Filter Time
Immediately
Adjustment
Pn114
-
Torque Feedforward
Immediately
Adjustment
Pn115
-
Torque Feedforward Filter Time
Immediately
Adjustment
Model Following Control Feedforward
You shall confirm and set that the Model Following Control function has been enabled (Pn150.0=1 or 2),
and then set Pn005.3=1(Use the model following control speed) or Pn005.2=1 (Use the model following
control torque feedforward).
For details on this method, refers to the section
Feedforward Set by Controller
The setting of Pn005.3=2 (Use the speed feedforward set by the controller) or Pn005.2=2 (Use the torque
feedforward set by the controller) is only available for EtherCAT Communication.
The relevant objects are 60B1h and 60B2h.
Index Subindex Name
Data Type
Access PDO Mapping Value
60B1h
0
Velocity
Offset
INT32
RW
Yes
-2147483648 to
2147483647
60B2h
0
Torque Offset
INT16
RW
Yes
-32768 to 32767
Feedforward calculated by Cubic Interpolation
The setting of Pn005.3=3 (Use the speed feedforward generated by Cubic interpolation algorithm) or
Pn005.2=3 (Use the torque feedforward generated by Cubic interpolation algorithm) is only available for
EtherCAT Communication.
The relevant object is 60C0h.
Index
Subindex
Name
Data Type
Access PDO Mapping Value
60C0h
0
Interpolation
sub mode select
INT16
RW
No
-1
9.5.4
Friction Compensation
The load friction must exist in the transmission system. However, severe load friction may cause low-
speed crawling, waveform distortion at speed zero-crossing, positioning lag, etc., which can affect the
dynamic and static performance of the Servo system.