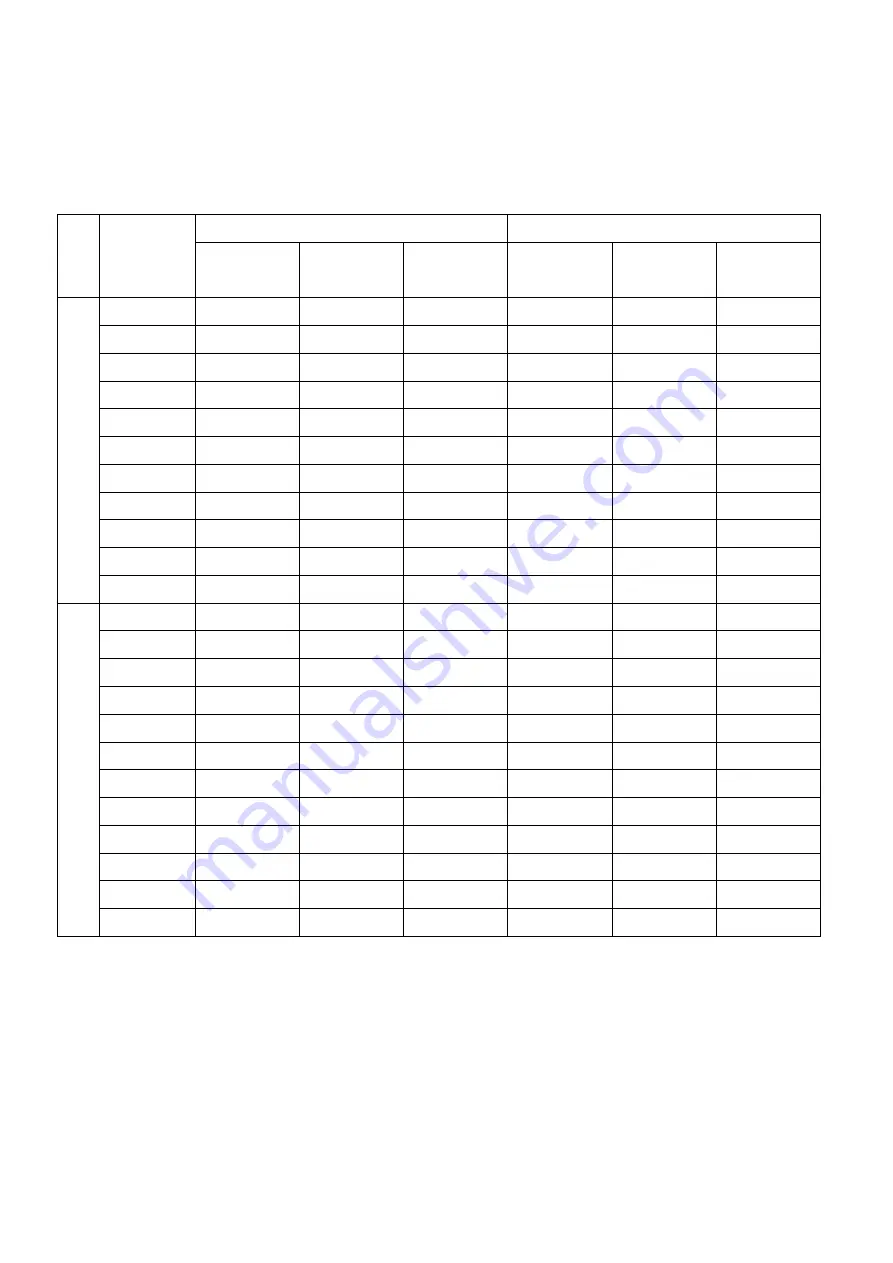
06 Optional Accessories | VFD-ED
6-2
The optional accessories listed in this chapter are available upon request. Installing additional accessories
to your drive can substantially improve the drive’s performance. Select accessories according to your
needs or contact your local distributor for suggestions.
6-1 Brake Resistors and Brake Units Used in AC Motor Drives
Recommended Model Selection
V
o
lt
ag
e
Delta’s
Motor Drive
Model
IM 10% ED*
1
PM 30% ED*
2
Min. Resistor
Value*
3
(
Ω
)
Suggested
Resistor Value*
4
(
Ω
)
Suggested
Braking Power
(kW)
Min. Resistor
Value*
3
(
Ω
)
Suggested
Resistor Value*
4
(
Ω
)
Suggested
Braking Power
(kW)
230V
VFD022ED21S
38.0
70.0
0.3
38.0
50.0
1.0
VFD037ED21S
19.0
30.0
0.5
19.0
32.0
1.5
VFD040ED23S
19.0
30.0
0.5
19.0
32.0
1.5
VFD055ED23S
15.6
20.0
1.0
15.6
25.0
2.0
VFD075ED23S
11.5
20.0
1.0
11.5
16.7
3.0
VFD110ED23S
9.5
13.0
1.5
9.5
12.5
4.0
VFD150ED23S
8.3
10.0
2.0
8.3
10.0
5.0
VFD185ED23S
5.8
8.0
2.0
5.8
7.8
7.5
VFD220ED23S
5.8
6.6
3.0
5.8
6.5
9.0
VFD300ED23S
4.8
5.1
4.0
4.8
5.0
10.0
VFD370ED23S
3.2
3.9
4.8
3.2
3.6
14.0
460V
VFD040ED43S
54.3
100.0
0.5
54.3
100.0
2.0
VFD055ED43S
48.4
75.0
1.0
48.4
100.0
2.0
VFD075ED43S
39.4
75.0
1.0
39.4
60.0
3.0
VFD110ED43S
30.8
43.0
1.5
30.8
50.0
4.0
VFD150ED43S
25.0
32.0
2.0
25
39.0
6.0
VFD185ED43S
20.8
32.0
2.0
20.8
26.0
7.2
VFD220ED43S
19.0
26.0
3.0
19.0
26.0
9.0
VFD300ED43S
14.1
20.0
4.0
14.1
19.5
12.0
VFD370ED43S
12.7
14.3
4.5
13.8
15.6
15.0
VFD450ED43S
12.7
13.0
6.0
10.3
13.0
18.0
VFD550ED43S
9.5
10.2
8.0
6.9
9.8
19.2
VFD750ED43S
6.3
7.2
9.0
6.4
7.1
26.4
*
1
The brake resistor should be able to endure 10 times the overload capacity.
*
2
The brake resistor should be able to endure 3.3 times the overload capacity.
*
3
If you choose other brake resistors instead of Delta's, calculate the maximum power and average power of the
selected braking power to ensure that they meet the requirements. Maximum power: Vb
2
/R; average power:
Vb
2
/R x ED%. (Vb stands for braking voltage; R stands for brake resistor value.)
*
4
The calculation of the brake resistor value and braking power is based on Delta’s brake resistor.
Summary of Contents for VFD-ED Series
Page 3: ......
Page 10: ...Ch01 Introduction VFD ED 1 3 1 2 Model Name 1 3 Serial Number...
Page 21: ...Ch01 Introduction VFD ED 1 14 Built In Keyboard Panel KPED LE01 Unit mm inch...
Page 26: ...Ch02 Installation VFD ED 2 5 Ambient Temperature Derating Curve Altitude Derating Curve...
Page 27: ...Ch02 Installation VFD ED 2 6 The page intentionally left blank...
Page 28: ...Ch03 Wiring VFD ED 3 1 Chapter 3 Wiring 3 1 Wiring 3 2 System Wiring Diagram...
Page 30: ...Ch03 Wiring VFD ED 3 3 3 1 Wiring...
Page 32: ...Ch03 Wiring VFD ED 3 5...
Page 38: ...Ch04 Main Circuit Terminals VFD ED 4 3 4 1 Main Circuit Diagram Frame B Frames C D Frame E...
Page 46: ...Ch05 Control Terminals VFD ED 5 3 Frame E Step 1 Step 2 Step 3...
Page 47: ...Ch05 Control Terminals VFD ED 5 4 5 2 Control Terminal Specifications...
Page 51: ...Ch05 Control Terminals VFD ED 5 8 The page intentionally left blank...
Page 94: ...06 Optional Accessories VFD ED 6 43 EMC Filter Model B84143D0150R127 Unit mm inch...
Page 95: ...06 Optional Accessories VFD ED 6 44 EMC Filter Model B84143D0200R127 Unit mm inch...
Page 96: ...06 Optional Accessories VFD ED 6 45 EMC Filter Model B84142A0042R122 Unit mm inch...
Page 242: ...Ch12 Descriptions of Parameter Settings VFD ED 12 31 Elevator Timing Diagram...
Page 313: ...Ch12 Descriptions of Parameter Settings VFD ED 12 102 The page intentionally left blank...
Page 317: ...Ch13 Warning Codes VFD ED 13 4 The page intentionally left blank...
Page 329: ...Ch14 Fault Codes VFD ED 14 12 The page intentionally left blank...
Page 351: ...Ch16 Safe Torque Off Function VFD ED 16 10 16 5 6 STL1 Figure 6 16 5 7 STL2 Figure 7...
Page 353: ...Ch16 Safe Torque Off Function VFD ED 16 12 The page intentionally left blank...
Page 373: ...Appendix A EMC Standard Installation Guide VFD ED A 20 The page intentionally left blank...
Page 389: ...Appendix B Revision History VFD ED B 16 The page intentionally left blank...