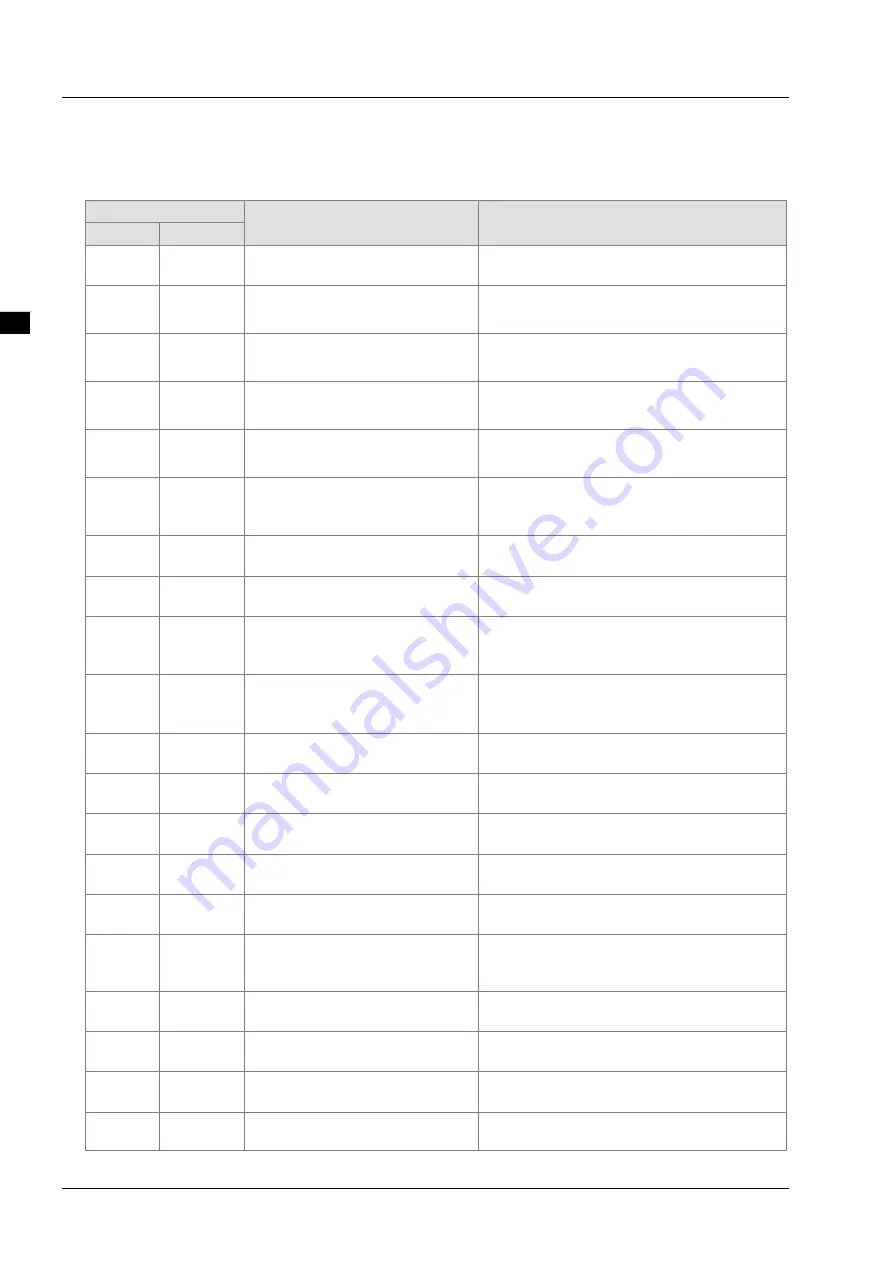
DVP15MC11T Operation Manual
12
1
12.2
Table of Error IDs in Motion Instructions
When an error occurs in the motion instruction, the value of ErrorID can be seen as follows for analysis of
the cause and troubleshooting.
ErrorID
Meaning
How to deal with
Hex
Decimal
0x1001
4097
The axis No. exceeds the valid range.
Make sure that the value of the input variable,
Axis
is within the range of 1~32.
0x1002
4098
The acceleration exceeds the valid
range.
Make sure that the value of the input variable,
Acceleration
is a positive number.
0x1003
4099
The deceleration exceeds the valid
range.
Make sure that the value of the input variable,
Deceleration
is a positive number.
0x1004
4100
The change rate of the acceleration
exceeds the valid range.
Make sure that the value of the input variable,
Jerk
is a positive number.
0x1005
4101
The velocity exceeds the valid range.
Make sure that the value of the input variable,
Velocity
is a nonzero value.
0x1006
4102
The position value exceeds the valid
range.
Make sure that the value of the input variable,
Position
of MC_MoveAbsolute is not greater than
the value of Modulo among axis parameters.
0x1007
4103
The direction value exceeds the valid
range.
Modify the value of the input variable,
Direction
into that which can be set in the instruction.
0x1008
4104
The buffermode value exceeds the
valid range.
Modify the value of the input variable,
BufferMode
into that which can be set in the instruction.
0x1009
4105
The input value for reference position
type is wrong.
Modify the value of the input variable,
ReferenceType
into that which can be set in the
instruction.
0x100A
4106
The timing for executing
MC_SetPosition is improper.
Change the timing of executing MC_SetPosition.
Do not execute MC_SetPosition while
MC_Home or MC_Stop is being executed.
0x100B
4107
The number of e-cam table is
incorrect.
Modify the value of the input variable,
CamTable
into that of CamId set in the software.
0x100C
4108
The axis No. of the master axis is
incorrect.
Make sure that the value of the input variable,
Axis
is within the range of 1~32.
0x100D
4109
The input value of the engagement
mode is wrong.
Modify the value of the input variable,
StartMode
into that which can be set in the instruction.
0x100E
4110
The value of the master scaling is
incorrect.
Make sure that the value of the input variable,
MasterScaling
is a positive number.
0x100F
4111
The value of the slave scaling is
incorrect.
Make sure that the value of the input variable,
SlaveScaling
is a nonzero value.
0x1010
4112
The chosen position source of the
master axis is wrong.
Modify the value of the input variable,
MasterValueSource
into that which can be set for
the instruction.
0x1011
4113
Conflict in the axis No. of the master
and slave axes.
Modify the values of the input variables,
Master
and
Slave
into different values.
0x1012
4114
Wrong e-gear numerator value
Modify the value of the input variable,
Numerator
into a nonzero value.
0x1013
4115
Wrong e-gear denominator value
Modify the value of the input variable,
Denominator
into a nonzero value.
0x1014
4116
The value of VelFactor is incorrect.
Modify the value of the input variable,
VelFactor
into that which can be set in the instruction.
12-8
Summary of Contents for DVP15MC11T
Page 9: ...Memo viii...
Page 15: ...DVP15MC11T Operation Manual _2 MEMO 2 4...
Page 71: ...DVP15MC11T Operation Manual _7 Memo 7 10...
Page 81: ...DVP15MC11T Operation Manual _8 Timing Chart F_TRG_CLK F_TRG_Q 8 10...
Page 158: ...Chapter 8 Logic Instructions 8_ The program 1 ASIN EN ENO In Out ASIN_EN ASIN_In Out1 8 87...
Page 249: ...DVP15MC11T Operation Manual _8 8 178...
Page 285: ...DVP15MC11T Operation Manual _8 Memo 8 214...
Page 323: ...DVP15MC11T Operation Manual 10 MEMO 10 34...
Page 549: ...DVP15MC11T Operation Manual A MEMO A 16...