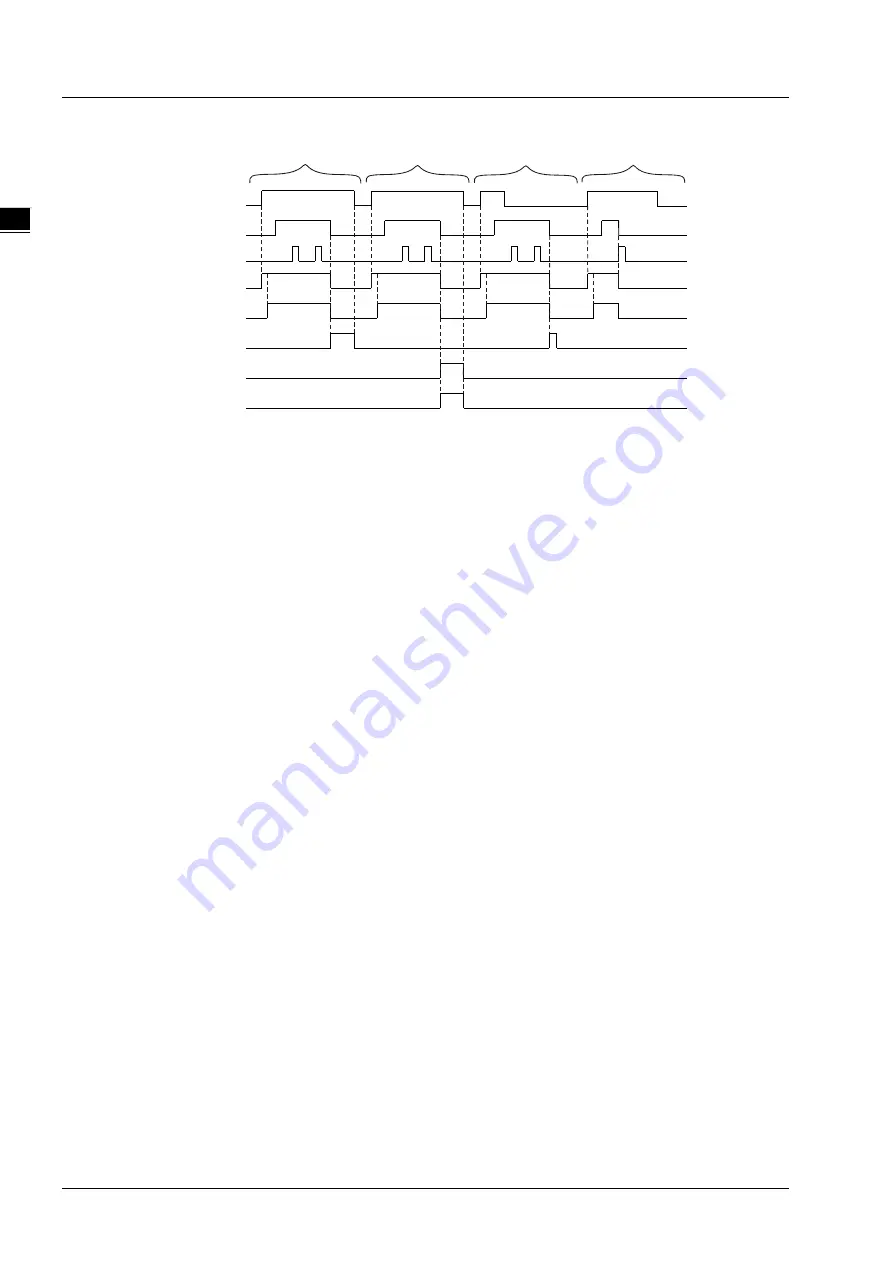
DVP15MC11T Operation Manual
11
1
Output Update Timing Chart
Case 1
:
Busy
changes to TRUE as
Execute
changes from FALSE to TRUE. And one period later,
Active
changes to TRUE. When the slave axis and master axis are in the synchronous motion,
InSync
changes from FALSE to TRUE. When the final point of the cam cycle is reached,
EndOfProfile
changes from FALSE to TRUE and changes to FALSE one cycle later. When
the cam relationship between the slave axis and master axis is disconnected (e.g. by
executing the MC_CamOut instruction),
CommandAborted
changes from FALSE to TRUE
and
InSync, Busy
and
Active
all change from TRUE to FALSE. After that,
CommandAborted
changes from TRUE to FALSE as
Execute
changes from TRUE to FALSE.
Case 2
:
As an error occurs in the execution of the instruction,
Error
changes from FALSE to TRUE,
ErrorID
shows corresponding error codes and
InSync
,
Busy
and
Active
all change from TRUE
to FALSE. After that,
Error
changes from TRUE to FALSE and the value of
ErrorID
changes
to 0 as
Execute
changes from TRUE to FALSE.
Case 3
:
The instruction execution still continues after
Execute
changes from TRUE to FALSE during
execution of the instruction. The timing for changing the state of
InSync
,
EndOfProfile, Busy
and
Active
is consistent with what state they are in as
Execute
is TRUE. After that,
InSync
,
Busy
and
Active
all change from TRUE to FALSE after the cam relationship between the
slave axis and master axis is disconnected. Meanwhile CommandAborted changes from
FALSE to TRUE and changes to FALSE one cycle later.
Case 4
:
If the cam motion is performed in the acyclic way (
Periodic
=FALSE),
EndOfProfile
changes
from FALSE to TRUE when the end point of the cam cycle is reached. Meanwhile
InSync
,
Busy
and
Active
all
change from TRUE to FALSE and
EndOfProfile
changes from TRUE to
FALSE one cycle later.
Function
The
MC_CamIn
instruction is used for making the slave axis and master axis move synchronously
according to the planned cam relationship. The
MC_CamOut
instruction is used for disconnecting the
cam relationship between the two axes.
Ca se 1
C ase 2
Case 3
Case 4
Exe cute
InS ync
E nd O fPr ofil e
B usy
A ctive
Er ro r
E rr or ID
A bo rt
11-152
Summary of Contents for DVP15MC11T
Page 9: ...Memo viii...
Page 15: ...DVP15MC11T Operation Manual _2 MEMO 2 4...
Page 71: ...DVP15MC11T Operation Manual _7 Memo 7 10...
Page 81: ...DVP15MC11T Operation Manual _8 Timing Chart F_TRG_CLK F_TRG_Q 8 10...
Page 158: ...Chapter 8 Logic Instructions 8_ The program 1 ASIN EN ENO In Out ASIN_EN ASIN_In Out1 8 87...
Page 249: ...DVP15MC11T Operation Manual _8 8 178...
Page 285: ...DVP15MC11T Operation Manual _8 Memo 8 214...
Page 323: ...DVP15MC11T Operation Manual 10 MEMO 10 34...
Page 549: ...DVP15MC11T Operation Manual A MEMO A 16...