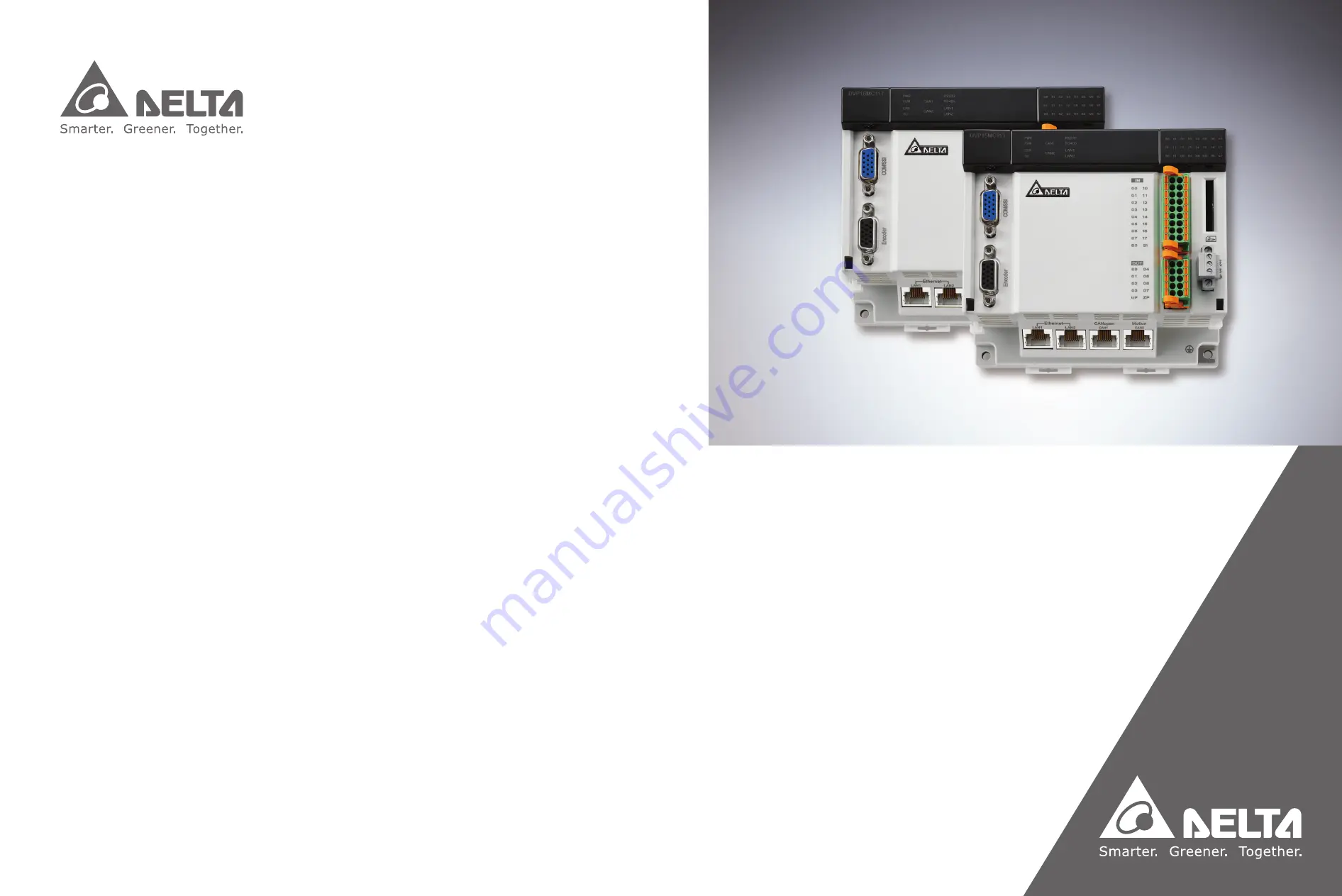
www.deltaww.com
DVP15MC
Operation Manual
D
VP15MC
Operation Manual
2016-06-30
Industrial Automation Headquarters
Delta Electronics, Inc.
Taoyuan Technology Center
No.18, Xinglong Rd., Taoyuan City,
Taoyuan County 33068, Taiwan
TEL: 886-3-362-6301 / FAX: 886-3-371-6301
Asia
Delta Electronics (Jiangsu) Ltd.
Wujiang Plant 3
1688 Jiangxing East Road,
Wujiang Economic Development Zone
Wujiang City, Jiang Su Province, P.R.C. 215200
TEL: 86-512-6340-3008 / FAX: 86-769-6340-7290
Delta Greentech (China) Co., Ltd.
238 Min-Xia Road, Pudong District,
ShangHai, P.R.C. 201209
TEL: 86-21-58635678 / FAX: 86-21-58630003
Delta Electronics (Japan), Inc.
Tokyo Office
2-1-14 Minato-ku Shibadaimon,
Tokyo 105-0012, Japan
TEL: 81-3-5733-1111 / FAX: 81-3-5733-1211
Delta Electronics (Korea), Inc.
1511, Byucksan Digital Valley 6-cha, Gasan-dong,
Geumcheon-gu, Seoul, Korea, 153-704
TEL: 82-2-515-5303 / FAX: 82-2-515-5302
Delta Electronics Int’l (S) Pte Ltd.
4 Kaki Bukit Ave 1, #05-05, Singapore 417939
TEL: 65-6747-5155 / FAX: 65-6744-9228
Delta Electronics (India) Pvt. Ltd.
Plot No 43 Sector 35, HSIIDC
Gurgaon, PIN 122001, Haryana, India
TEL : 91-124-4874900 / FAX : 91-124-4874945
Americas
Delta Products Corporation (USA)
Raleigh Office
P.O. Box 12173,5101 Davis Drive,
Research Triangle Park, NC 27709, U.S.A.
TEL: 1-919-767-3800 / FAX: 1-919-767-8080
Delta Greentech (Brasil) S.A.
Sao Paulo Office
Rua Itapeva, 26 - 3° andar Edificio Itapeva One-Bela Vista
01332-000-São Paulo-SP-Brazil
TEL: 55 11 3568-3855 / FAX: 55 11 3568-3865
Europe
Delta Electronics (Netherlands) B.V.
Eindhoven Office
De Witbogt 20, 5652 AG Eindhoven, The Netherlands
TEL : +31 (0)40-8003800 / FAX : +31 (0)40-8003898
DVP-0191920-00
*We reserve the right to change the information in this manual without prior notice.
Summary of Contents for DVP15MC11T
Page 9: ...Memo viii...
Page 15: ...DVP15MC11T Operation Manual _2 MEMO 2 4...
Page 71: ...DVP15MC11T Operation Manual _7 Memo 7 10...
Page 81: ...DVP15MC11T Operation Manual _8 Timing Chart F_TRG_CLK F_TRG_Q 8 10...
Page 158: ...Chapter 8 Logic Instructions 8_ The program 1 ASIN EN ENO In Out ASIN_EN ASIN_In Out1 8 87...
Page 249: ...DVP15MC11T Operation Manual _8 8 178...
Page 285: ...DVP15MC11T Operation Manual _8 Memo 8 214...
Page 323: ...DVP15MC11T Operation Manual 10 MEMO 10 34...
Page 549: ...DVP15MC11T Operation Manual A MEMO A 16...