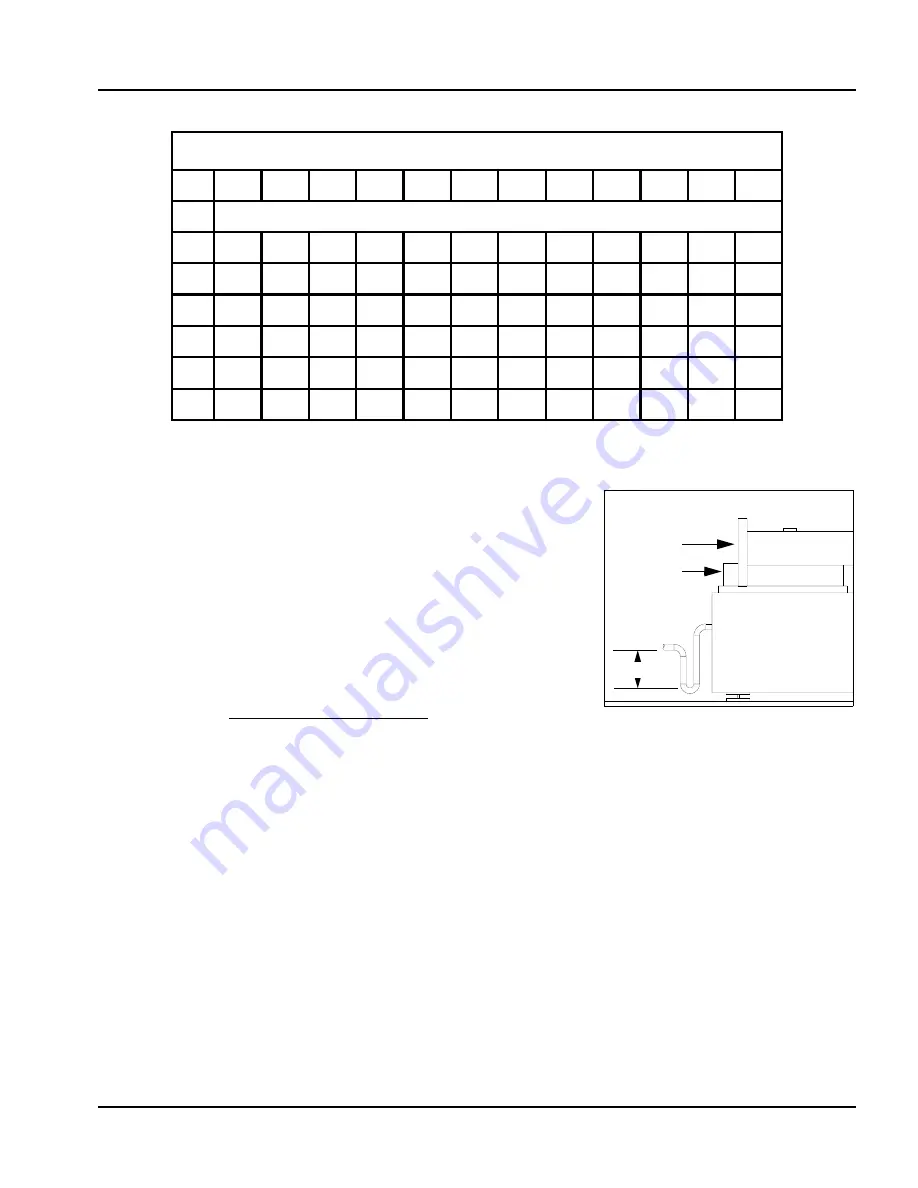
Section 2 — Installation
Part No. 750-263
2-29
Table 2-13: Maximum flow rate through ClearFire boilers (metric flow rates)
H. CONDENSATE REMOVAL AND TREATMENT
The condensate generated during normal boiler operation must be
removed in accordance with local codes and regulations. The
condensate can be piped to a local treatment system or run into the
optional condensate treatment assembly. When piping condensate
direct to drain, a trap (
Figure 2-36
) must be installed on the
condensate outlet to prevent discharge of flue gases from the boiler.
When using the treatment tank, a drain trap is included in the tank
assembly and no external trap is required.
The water trap must be filled with water prior to commissioning and
checked or refilled at each required maintenance interval.
Notice
The condensate occurring during operation in both the boiler and the flue
gas pipeline has to be neutralized and piped to a safe drain. The conditions
for the discharge of condensates into public drain systems are determined
by the local authorities and municipalities.
Condensate leaving the boiler normally has a pH of 4-6. The
responsible authority will inform you if a higher pH value is required
for condensate piped to drain. The CFC neutralization system
contains the granulate NEUTRALAT, a natural compound which
acts to increase the pH of the condensate flowing through it. The
neutralization system comprises the plastic neutralization tank with
condensate inlet, makeup valve, drain trap, granulate chamber and
condensate outlet (see
Figure 2-38
). The system is installed in the
CFC lower collection area.
5
11
17
22
27
33
38
45
50
55
61
64
500
21.6
10.9
7.5
5.4
4.3
3.6
2.7
2.5
2.3
2
1.8
1.6
750
29.75
15
10
7.5
6
5
4.3
3.6
3.4
2.9
2.7
2.5
1000
40
20
14
10
8
7
6
5
4.5
4
3.6
3.4
1500
59
29.5
20
15
12
10
8.4
7.5
6.6
6
5.4
5.2
1800
80
40
27
20
16
13
11.3
10
9
8
7.3
6.8
2500
106.7
53.4
36.7
26.8
21.6
17.9
15.2
13.4
11.8
10.9
9.8
8.8
Recommended flow rates relative to temperature drop so as not to exceed boiler output.
System Temperature Drop
0
C
Flow Rate m
3
/hr.
Boiler
Size
Figure 2-36 Flue Gas Trap 6 inch
Minimum Water Column
6”
Return Water In
Stack
Clearfire
Base
Summary of Contents for CFC-1000
Page 35: ...Section 2 Installation Part No 750 263 2 21 Figure 2 23 Gas Piping ...
Page 47: ...Section 2 Installation Part No 750 263 2 33 Figure 2 41 Electrical Connection Diagram ...
Page 49: ...Section 2 Installation Part No 750 263 2 35 Figure 2 43 CFC Wiring Diagram dual fuel units ...
Page 50: ...Section 2 Installation 2 36 Part No 750 263 ...
Page 70: ...Section 3 Stack and Intake Vent Sizing and Installation 3 20 Part No 750 263 ...
Page 102: ...Section 4 CFC Commissioning 4 32 Part No 750 263 ...
Page 108: ...Section 5 Service and Maintenance 5 6 Part No 750 263 ...
Page 113: ...Section 6 Parts Part No 750 263 6 5 Figure 6 3 Casing Table 6 5 Casing parts ...
Page 117: ...Section 6 Parts Part No 750 263 6 9 Figure 6 7 Electrical assemblies single fuel ...
Page 123: ...APPENDIX A CB FALCON CONTROLLER ...
Page 124: ......
Page 244: ...CB FALCON 750 265 120 ...
Page 245: ...APPENDIX B CB FALCON PLUG IN MODULE ...
Page 246: ......
Page 250: ......
Page 251: ...APPENDIX C GAS VALVE ...
Page 252: ......
Page 269: ...APPENDIX D CB FALCON MODBUS COMMUNICATION ...
Page 270: ......