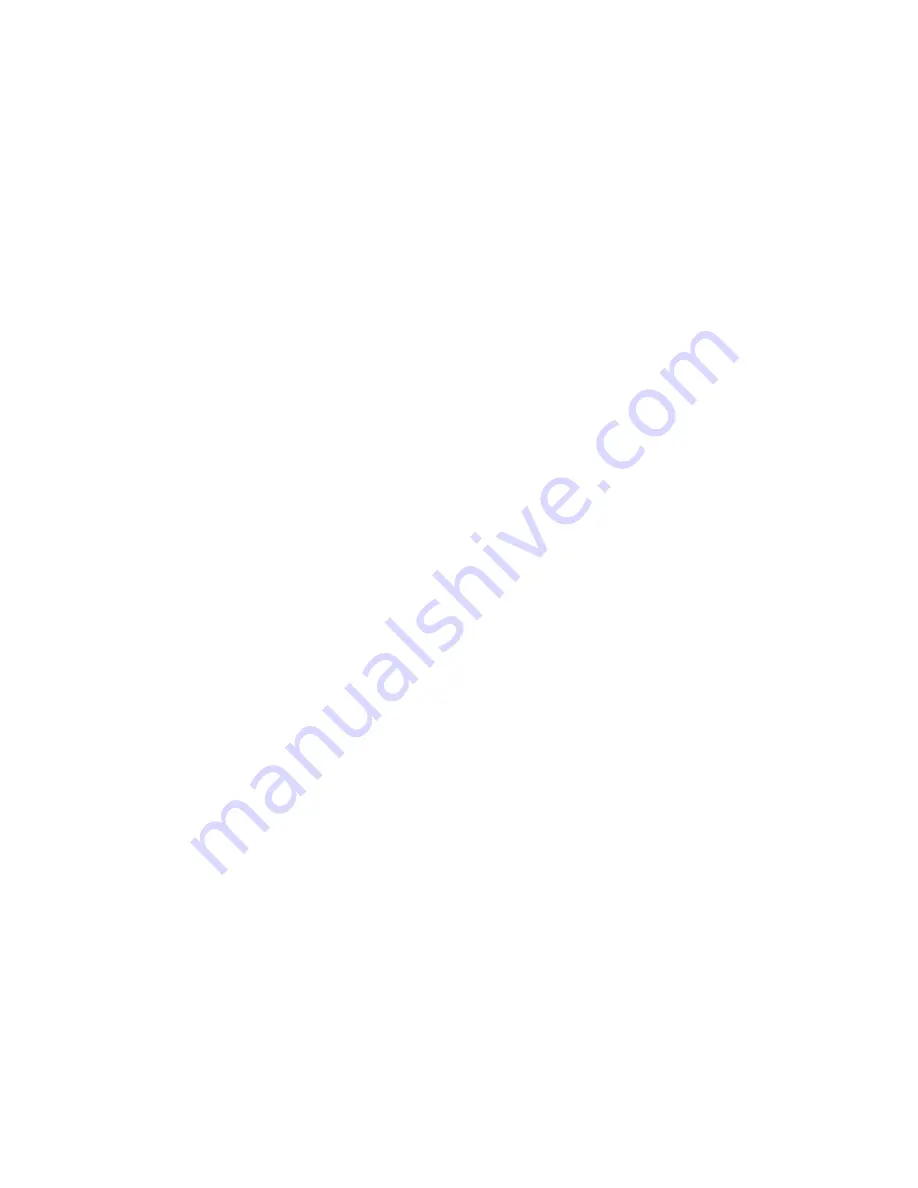
CB FALCON
750-265
70
1.
Open the master switch.
2.
Close the pilot and main burner manual fuel shut-off
valve(s).
3.
Close the master switch
—
Go to the 833-3577 Display/Operator Interface.
—
Select Diagnostics Test button at the bottom of the
display.
—
Select Diagnostics test button at the bottom of this new
screen.
—
Select Pilot Test at the bottom of this new screen.
—
Select Start Test at the bottom of this screen.
4.
Start the system with a call for heat. Raise the setpoint of
the operating controller. The Falcon sequence should
start and prepurge (if applicable) should begin. The
sequence will hold in pilot flame establishing period with
only the ignition on. Ignition spark should occur but the
flame signal should not be more than 0.5 Vdc.
5.
If the flame signal is higher than 0.5 Vdc and the FLAME
LED does come on, consult the equipment operating
manual and resight the detector farther out from the
spark, or away from possible reflection. It may be neces-
sary to construct a barrier to block the ignition spark from
the detector view. Continue adjustments until the flame
signal due to ignition spark is less than 0.5 Vdc.
NOTE:
For controllers with software revision xxxx.2292 or
higher, if the above procedures have been attempted
and flame signal is still above 0.5 Vdc, use the follow-
ing procedure:
FOR DIRECT BURNER IGNITION SYSTEMS
a.
Using the 833-3577 Display/Operator Interface,
select the Configure button (lower left corner of the
Status page).
b. Using the left scroll down function, scroll down to
select the System Configuration Parameter page
(you will need to be logged in with a password).
c. Select Flame Sensor Type parameter.
d. Select UV Power Tube with Spark Interference.
e. Changing the Flame Sensor Type will require param-
eter verification.
f.
Page back one level (upper right screen corner back
arrow button).
g. Select the Verify button.
h. Select Begin.
i.
Follow the prompts on the Operator Interface.
FOR PILOT SYSTEMS
a.
Using the 833-3577 Display/Operator Interface,
select the Configure button (lower left corner of the
Status page).
b. Using the left scroll down function, scroll down to
select the System Configuration Parameter page
(you will need to be logged in with a password).
c. Select Flame Sensor Type parameter.
d. Select UV Power Tube with Spark Interference.
e. Select the Burner Control Ignition Page.
f.
Select Ignitor On During parameter.
g. Select 1st half of PFEP.
h. Changing these two parameters will require parame-
ter verification.
i.
Page back one level (upper right screen corner back
arrow button).
j.
Select the Verify button.
k. Select Begin.
l.
Follow the prompts on the Operator Interface.
Response to Other Ultraviolet
Sources
Some sources of artificial light (such as incandescent or
fluorescent bulbs, and mercury sodium vapor lamps) and
daylight produce small amounts of ultraviolet radiation. Under
certain conditions, an ultraviolet detector responds to these
sources as if it is sensing a flame. To check for proper detector
operation, check the Flame Failure Response Time (FFRT) and
conduct Safety Shutdown Tests under all operating conditions.
Flame Signal With Hot Combustion
Chamber (All Installations)
1.
With all initial start-up tests and burner adjustments com-
pleted, operate the burner until the combustion chamber
is at the maximum expected temperature.
2.
Observe the equipment manufacturer’s warm-up
instructions.
3.
Recycle the burner under these hot conditions and mea-
sure the flame signal. Check the pilot alone, the main
burner flame alone, and both together (unless monitoring
only the pilot flame when using an intermittent pilot, or
only the main burner flame when using DBI). Check the
signal at both High and Low Firing Rate positions and
while modulating, if applicable.
4.
Lower the setpoint of the operating controller and
observe the time it takes for the burner flame to go out.
This should be within four seconds FFRT of the control-
ler.
5.
If the flame signal is too low or unsteady, check the flame
detector temperature. Relocate the detector if the tem-
perature is too high.
6.
If necessary, realign the sighting to obtain the proper sig-
nal and response time.
7.
If the response time is still too slow, replace the control-
ler.
8.
If the detector is relocated or resighted, or the controller
is replaced, repeat all required Checkout tests.
SAFETY SHUTDOWN TESTS
(ALL INSTALLATIONS)
Perform these tests at the end of Checkout, after all other tests
are completed. If used, the external alarm should turn on.
Press the RESET pushbutton on the Falcon module to restart
the system.
1.
Open a Pre-Ignition Interlock (if PII parameter is enabled)
during the STANDBY or PREPURGE period.
a. *Pre-Ignition ILK* fault is displayed on the Operator
Interface Module.
b. Safety shutdown occurs.
2.
Opening a Lockout Interlock during PREPURGE, PILOT
IGN, MAIN IGN or RUN period.
a. *Lockout ILK* fault is displayed on the Operator
Interface Module.
b. Safety shutdown occurs.
3.
Detection of flame 240 seconds after entry to STANDBY
from RUN. Detection of flame from 10 seconds up to 30 sec-
onds into PREPURGE time.
a. Simulate a flame to cause the flame signal voltage
level to rise above the flame threshold value for 240
seconds after entry to STANDBY from RUN and also
Summary of Contents for CFC-1000
Page 35: ...Section 2 Installation Part No 750 263 2 21 Figure 2 23 Gas Piping ...
Page 47: ...Section 2 Installation Part No 750 263 2 33 Figure 2 41 Electrical Connection Diagram ...
Page 49: ...Section 2 Installation Part No 750 263 2 35 Figure 2 43 CFC Wiring Diagram dual fuel units ...
Page 50: ...Section 2 Installation 2 36 Part No 750 263 ...
Page 70: ...Section 3 Stack and Intake Vent Sizing and Installation 3 20 Part No 750 263 ...
Page 102: ...Section 4 CFC Commissioning 4 32 Part No 750 263 ...
Page 108: ...Section 5 Service and Maintenance 5 6 Part No 750 263 ...
Page 113: ...Section 6 Parts Part No 750 263 6 5 Figure 6 3 Casing Table 6 5 Casing parts ...
Page 117: ...Section 6 Parts Part No 750 263 6 9 Figure 6 7 Electrical assemblies single fuel ...
Page 123: ...APPENDIX A CB FALCON CONTROLLER ...
Page 124: ......
Page 244: ...CB FALCON 750 265 120 ...
Page 245: ...APPENDIX B CB FALCON PLUG IN MODULE ...
Page 246: ......
Page 250: ......
Page 251: ...APPENDIX C GAS VALVE ...
Page 252: ......
Page 269: ...APPENDIX D CB FALCON MODBUS COMMUNICATION ...
Page 270: ......