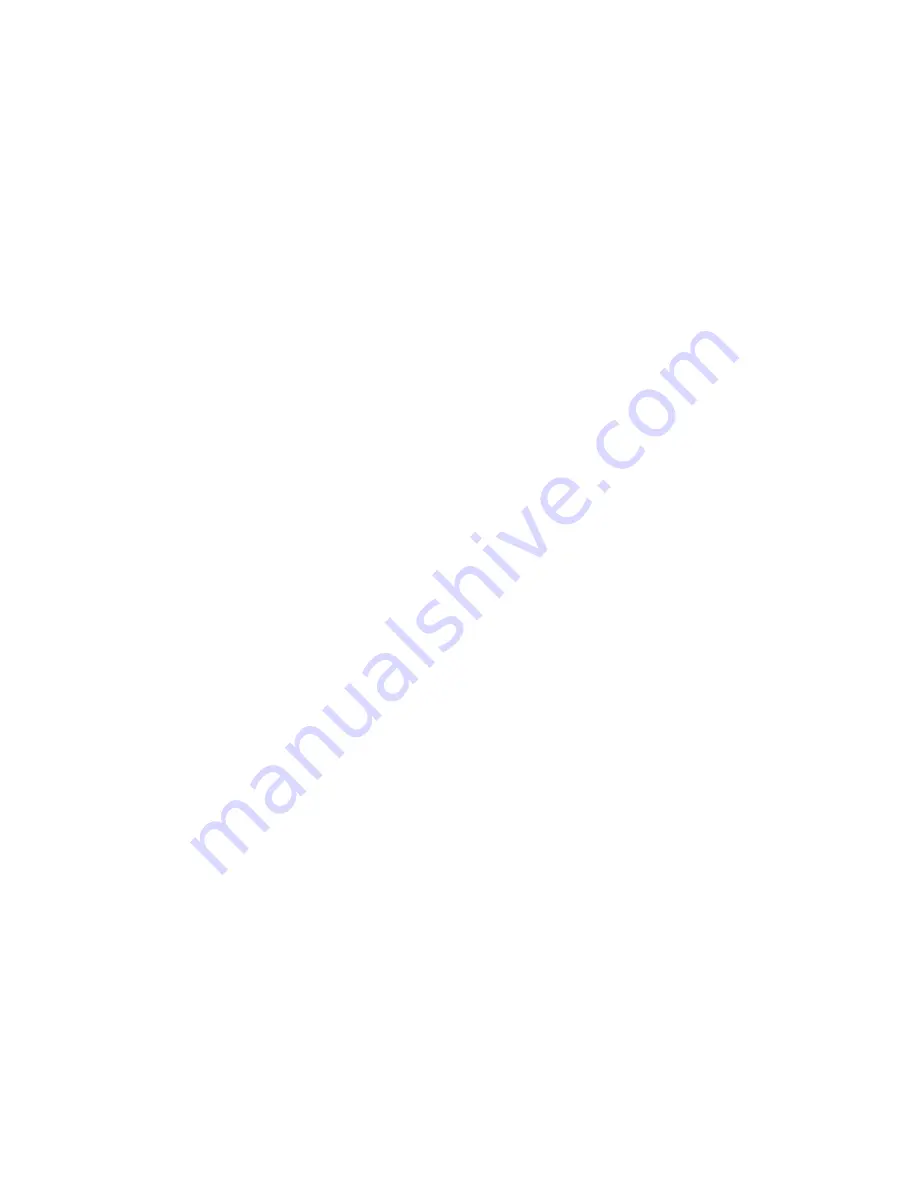
32
3.5.3 ADAPTING THE HYDRAULIC SOLENOID BLOCK FOR A LOAD
SENSING HYDRAULIC SYSTEM
The Norac 6 Station Valve block can be changed from a Closed Centre system to Load Sensing system. A
solenoid-operated valve and a sensing line must be added to change the valve type.
There is a possibility that some tractors may have a heating problem, if they run the SB4000 sprayer in a close
centre configuration with a tractor that has load sense hydraulics. Brandt recommends that you first try using the
sprayer as a closed centre and closely monitor the hydraulic temperature. If you do not have a heating problem,
you will not have to install the Load Sensing Kit on the sprayer. If you find you do have a heating problem, you
should install the Load Sensing Kit. You will also need to modify the tractor hydraulics system to accept the load
sensing line, the pressure line and the return line coming from the sprayer. For many tractors, a load sensing
conversion kit can be purchased directly from the tractor manufacturer and in other cases, hydraulic hoses and
fittings will need to be sourced locally.
The 6 station valve block located on the back of the sprayer can be changed from a standard closed centre
configuration to a load sensing configuration by adding the Load Sensing Kit, P/N C002975. The Load Sensing
Kit consists of a normally closed solenoid operated valve and a sensing line.
The load sensing line that installs on the sprayer must couple into a load sensing port on the tractor. The pressure
line to the sprayer must be connected into the pump pressure line (or power beyond port) on the tractor and the
return line from the sprayer should be directed to tank. With the load sensing kit installed, the pressure and return
lines should not be connected to the quick couplers on the back of the tractor. They must be connected as per
above.
There is no oil flow through the sensing line. This line is used to sense the load once the joystick control has been
activated and tell the pump to stroke up and deliver the required flow and pressure to meet the hydraulic demand.
If the tractor manufacturer does not have a tractor load sense kit available and one has to be created, then it should
be noted that a flow limiting device ( 2 port pressure compensated flow control or fixed orifice ) needs to be
installed in the pressure supply line to limit the flow to the block to 7 gpm.
The sprayer water pump should be still connected to a remote valve on the tractor and the flow should be set so
that a sufficient deadhead pressure is achieved. The flow limiter at the pump must be installed and the needle valve
on the motor must be closed all the way.
To change the valve block to a Load Sensing system, a Normally Closed solenoid valve must be added to the “LS”
port on the Norac 5 Station Valve block. The Load Sensing conversion kit can be purchased from Brandt, Part
No. C002975.
1. Remove the plug installed in the “LS” port and install the solenoid valve.
2. Connect the Normally Closed solenoid valve to the extra terminal in the wiring harness.
3. Remove the plug from the ‘S’ port in the side of the block and replace it with the #4 MORB x #4 MJIC
adapter fitting.
Summary of Contents for SB4000
Page 1: ...SB4000 SUSPENDED BOOM SPRAYER Part No B012920 Rev 14 Effective Mar 2009 OPERATORS MANUAL...
Page 5: ......
Page 107: ...96...
Page 136: ...125 8 SPECIFICATIONS FIG 8 1 MACHINE DIMENSIONS FOR SB4000 SPRAYER TRANSPORT POSITION...
Page 137: ...126 FIG 8 2 MACHINE DIMENSIONS FOR SB4000 SPRAYER FIELD POSITION...
Page 144: ...133 Notes...