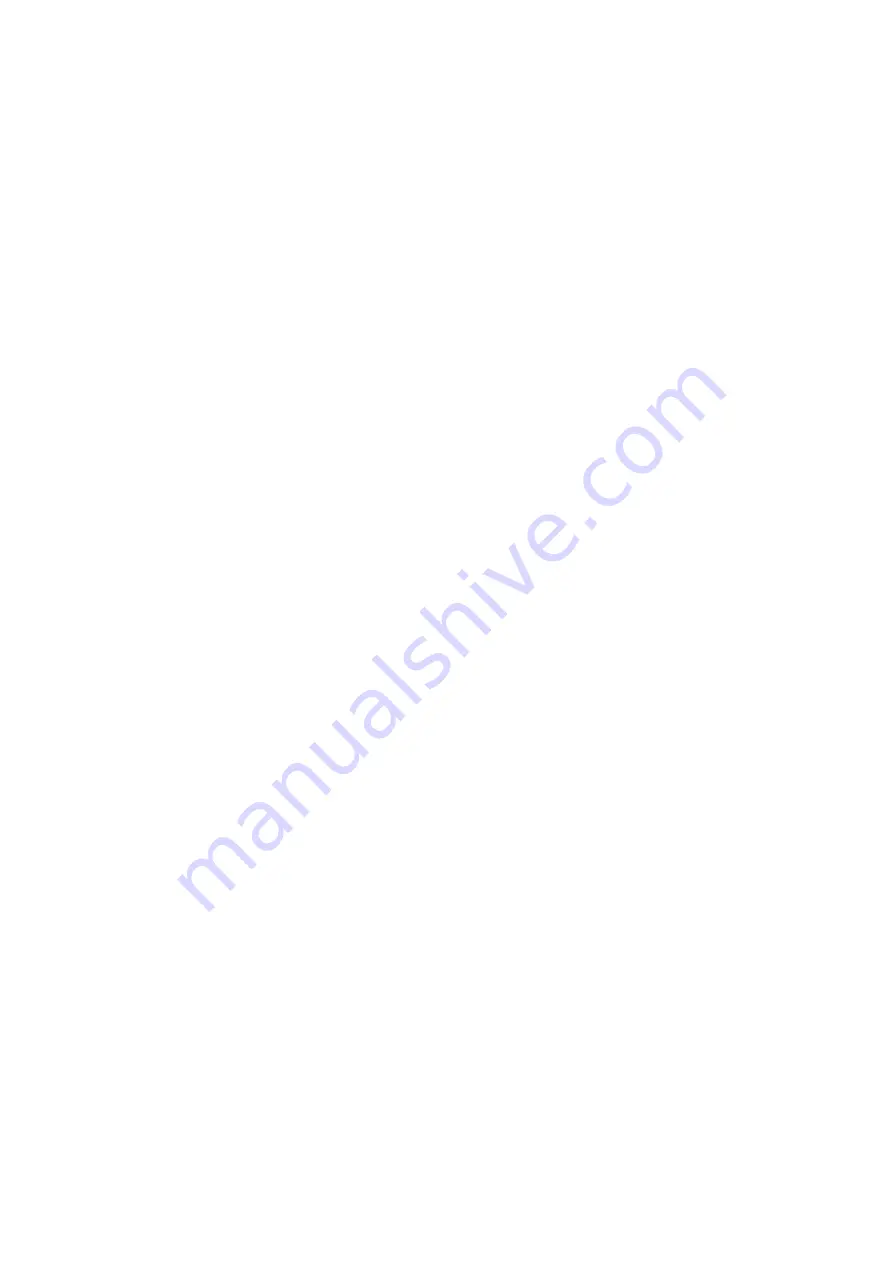
3522.5-0000010
РЭ
11
Introduction
The present manual is designed for studying the structure, operation rules and
maintenance of tractors “Belarus-3522.5”.
Scrutinize this manual and operation manual of the engine TCD 7,8 L06, attached
to your tractor. It will help you to study the rules of correct operation and maintenance.
Failure to follow this instruction can lead to operator's injury or a breakdown of a
tractor or harming third persons.
Operation of a tractor, its maintenance and repair shall be carried out only by em-
ployees, familiar with all of its parameters and characteristics and informed about neces-
sary safety requirements to prevent casualties.
In connection with constant development of a tractor some changes, which are not
depicted in the present manual, can be introduced in the structure of certain units and
parts.
Any arbitrary changes made by a consumer release the manufacturer from respon-
sibility for possible further injuries to the operator and tractor breakdown.
Adopted abbreviations and conventional notations:
ADL – automatic differential lock;
AB – accumulator battery
DL – differential lock
RADL – rear axle differential lock;
PLU – pilot lamps unit;
SU – switching unit;
PASU – protection and switching unit;
FC – fast coupling;
ECU – engine control unit;
EJU – electronic joystick unit;
TDC – top dead center;
PTO – power takeoff shaft;
PRS – power reception shaft;
HSC – hydrostatic steering control;
HLL – hydraulic lift linkage;
HS – hydraulic system;
FFVS – frequency fuel volume sensor;
STM – shift-time maintenance;
RPTO – rear power takeoff shaft;
SPTA – spare parts, tools and accessories;
RA – rear axle;
RLL – rear lift linkage;
IVA – integral voltage adjuster;
II – integrated indicator;
GB – gearbox;
CECS – complex electronic control system;
MTU – machine and tractor unit;
CC – coupling clutch;
LL – lift linkage;
CAC – charged air cooler;
IAH – inlet air heater;
FDA – front driving axle;
FPTO – front power takeoff;
VC – voltage converter;
https://tractormanualz.com/
Summary of Contents for 3522.5
Page 1: ...BELARUS 3522 5 3522 5 0000010 OM OPERATOR S MANUAL 2011 https tractormanualz com ...
Page 9: ...3522 5 0000010 РЭ 10 https tractormanualz com ...
Page 335: ...3522 5 0000010 OM 336 Service bulletins https tractormanualz com ...
Page 337: ...3522 5 0000010 OM 375 Annex B compulsory https tractormanualz com ...
Page 338: ...3522 5 0000010 OM 376 Annex B obligatory https tractormanualz com ...
Page 339: ...3522 5 0000010 OM 377 Annex C obligatory https tractormanualz com ...
Page 340: ...3522 5 0000010 РЭ Annex D obligatory 378 https tractormanualz com ...