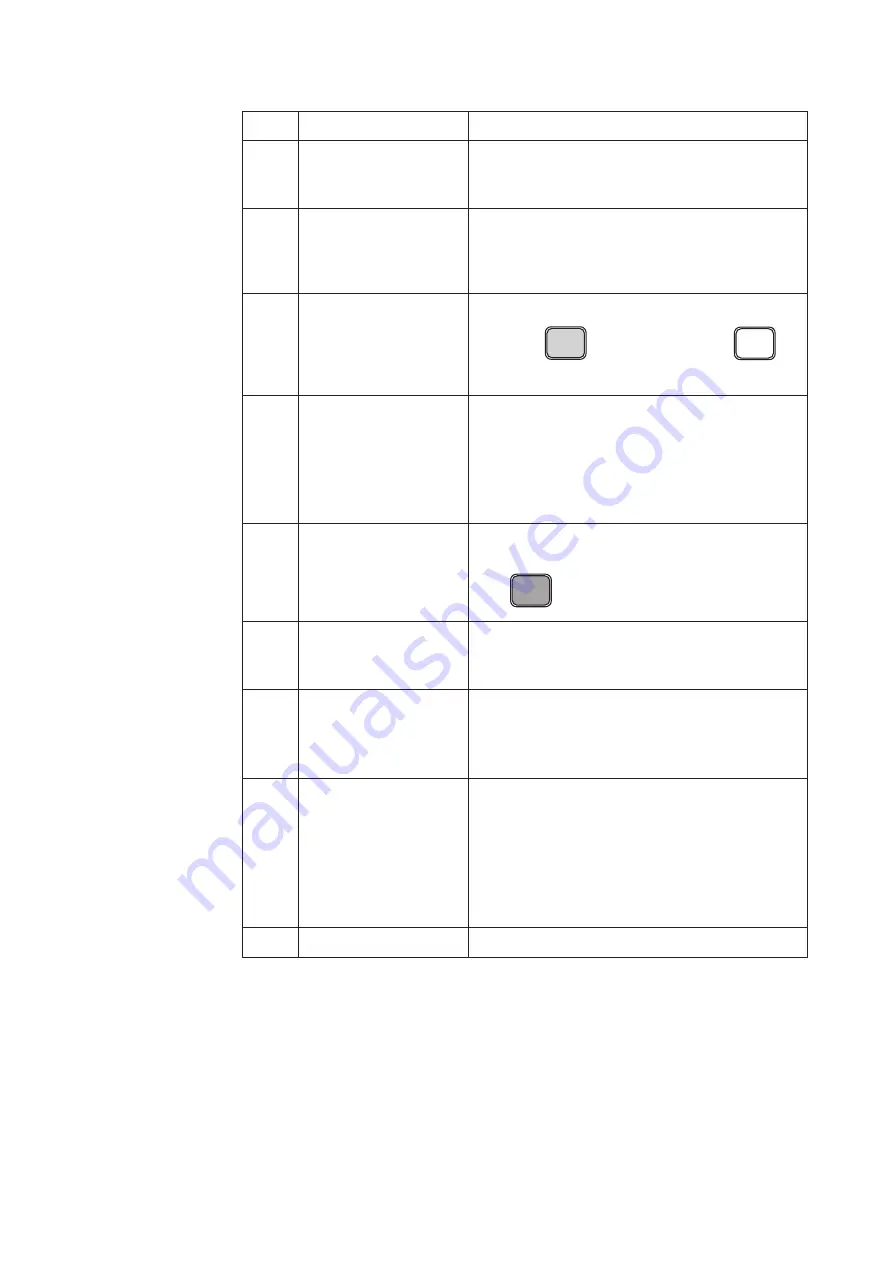
6-33
No.
Error message
Checkpoint and action
8
ILLEGAL RESPONSE
Abnormal communication with the electromagnetic
flowmeter.
Check the communication cable and load resistance.
9
IN LOCAL MODE
The converter is currently being operated from the
display panel.
At this time, it is not possible to communicate from
the SFC.
10
IN OUTPUT MODE
The converter is in constant current generation
mode.
Press the
OUT- J
PUT
INPUT
key and then press the
CLR
( No )
key
to cancel the mode.
11
INVALID DATABASE
A critical failure. Stop the electromagnetic flow
meter.
This error occurs because the converter database has
not been set correctly when the power to the
converter is turned ON.
Re-enter the CONF data.
12
INVALID REQUEST
The requested function cannot be performed.
Check the operation procedure of the SFC and press
the
U
STAT
F/S DIR
key.
13
LOCAL MODE
The converter is being operated.
At this time, it is not possible to communicate from
the SFC.
14
NO XMTR.RESPONSE
There is no response from the electromagnetic flow
meter.
Check the communication cable and measurement
loop.
15
NVM FAULT
A critical failure. Stop the electromagnetic flow
meter.
The non-volatile memory of the converter is
abnormal. Turn OFF the power and then turn it ON
again and check the operation.
If the same message still appears after taking the
action above, contact an Azbil Corp. representative.
16
PRINTER FAIL!
The printer does not operate.
Summary of Contents for MagneW Two-wire PLUS+ MTG15A
Page 8: ...vi...
Page 22: ...1 14...
Page 56: ...2 34...
Page 60: ...3 4 Fig 3 2...
Page 66: ...3 10...
Page 70: ...4 4...
Page 144: ...5 74...
Page 226: ...6 82...
Page 268: ...7 42...
Page 274: ...8 6...
Page 275: ......
Page 278: ......
Page 280: ......