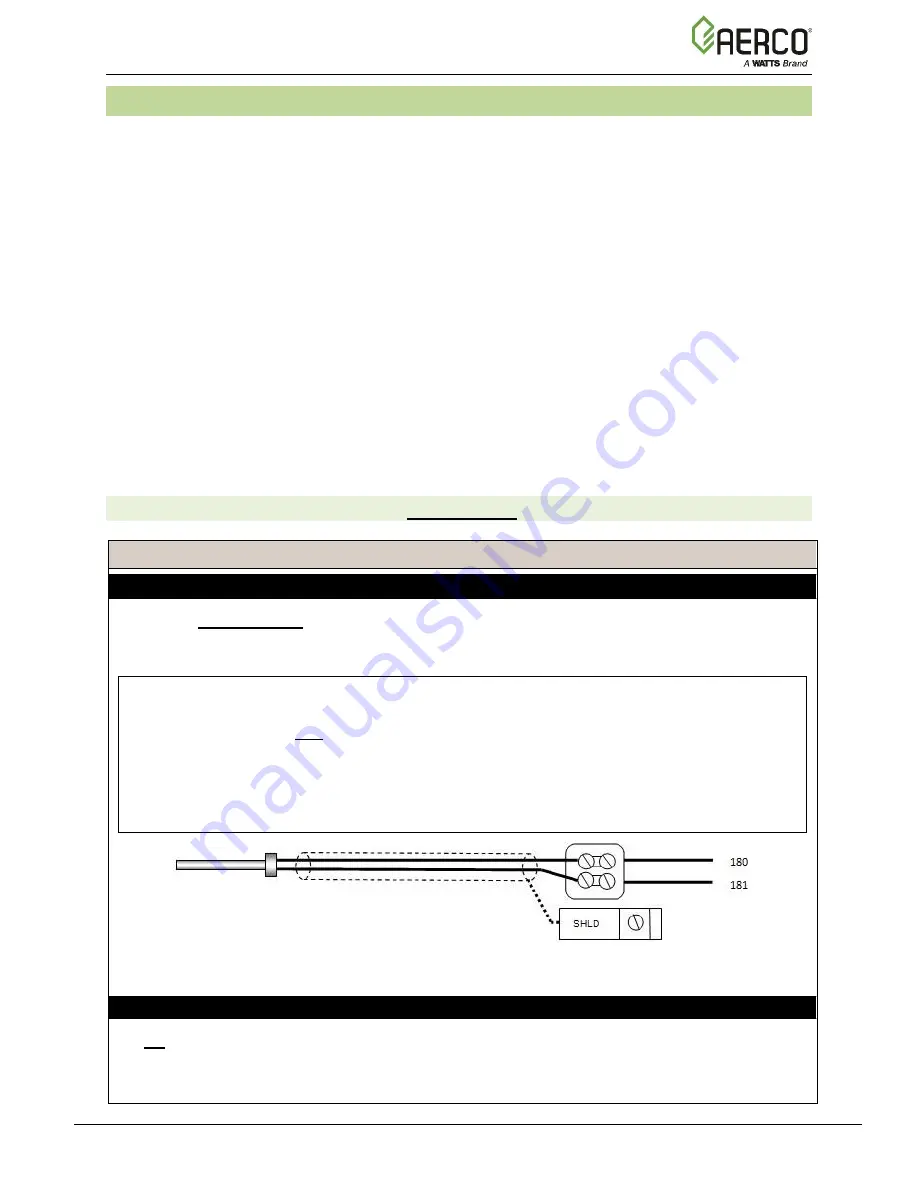
Benchmark with Edge [I]: Operation-Maintenance Manual
SECTION 7
– BOILER SEQUENCING TECHNOLOGY
OMM-0145_A99
• GF-218 • 9/18/2019 Technical Support • (800) 526-0288 • Mon-Fri, 8 am - 5 pm EST Page
107
of
157
7.3 BST Implementation Instruction
There are 8 BST implementation options, described below. The instructions for each refer to I/O
board connections described in Section 2.11.1 in the
Benchmark 750-6000 with Edge [i]: Install-
Startup Manual
(OMM-0144, GF-217).
All instructions in the sections below refer to one or more of the following components:
•
Modbus Transmitter:
o
P/N
24444-1
includes PT1000 Header Temp Sensor P/N
61058
.
o
P/N
24444-3
includes PT1000 Header Temp Sensor P/N
61058
, box and power supply.
•
Header Temp Sensor, either:
o
P/N
61040 (BALCO)
if connecting directly to I/O board.
o
P/N
61058 (PT1000)
dual bead, if connecting to Modbus Transmitter
•
Outdoor Sensor, either:
o
P/N
61047 (BALCO)
if connecting directly to I/O board.
o
P/N
61060 (PT1000)
if connecting to Modbus Transmitter.
7.3.1
Option 1 Constant Setpoint: Direct Wired Header Temp Sensor
OPTION 1
Instructions: Constant Setpoint with Direct Wired Header Temp Sensor
Step 1:
HEADER TEMP SENSOR WIRING
– BST MANAGER Unit
1. On the
BST Manager
unit, connect the
Header Temp Sensor
to the Feed Forward
(FFWD) terminals on the P-1 Harness via the terminal block labeled
Header Temp sensor
in the I/O Box.
NOTES:
•
The
Header Temp Sensor
must be installed between 2 and 10 feet (0.61 and 3.1m)
downstream of the
last
boiler in the plant’s supply water header.
•
Shielded pair 18 - 22 AWG cable is recommended for
Header Temp Sensor
wiring.
There is no polarity to be observed.
•
The ground for the shield is at the “SHLD” terminal in the I/O the Box. The sensor end of
the shield must be left free and ungrounded.
Step 2: CONFIGURATION
On All Boiler:
1. Go to:
Main Menu
→
Advanced Setup
→
BST Cascade
→
Cascade Configuration
:
•
Set the
Unit Mode
parameter to
BST Client
.
HEADER TEMP SENSOR
I/O BOX