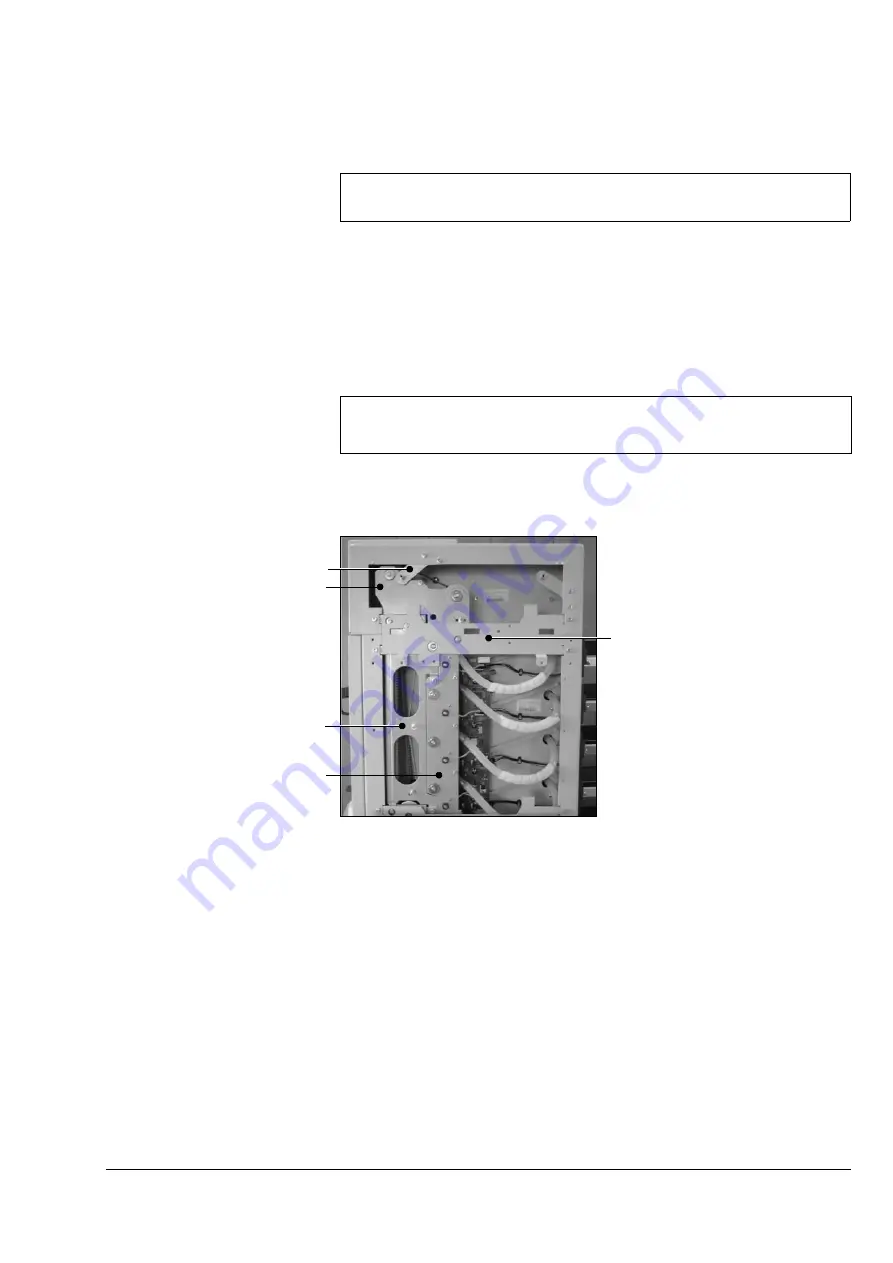
Service Procedures
•
General Service Procedures
Watkiss DigiVAC Service Manual - Issue 2 - 29/11/04
15
3.1.4 Removing L/H Side Plates
For many service procedures it is necessary to remove the joint, coupling and
clamp plates from the L/H side of the machine in order to access other parts.
Procedure
1. Disconnect the DigiVAC from the mains power supply.
2. Remove the side covers from the top module and bin modules on the L/H
side of the machine.
only:
carefully disconnect the 50-way cable and earth lead
from behind the screen mounting panel.
DigiVAC standard only:
Remove the control panel (see Section 3.3.1).
3. Undo the retaining screws and remove the joint plates from between the
top and bin modules.
Figure 3:3 Removing L/H Side Plates
4. Pivot the L/H top module side cover fixing tang bracket away from the top
conveyor coupling plate by undoing one retaining screw and loosening the
other.
5. Undo the retaining screws and remove the top conveyor coupling plate.
6. Undo the retaining screws and remove the bin module feeder belt clamp
plates.
7. Undo the retaining screws and remove the feeder clutch plates.
8. Continue with other service procedures as necessary.
3.1.5 Bin Addressing
After bin modules have been installed, or if the feeder control PCB has been
changed, the bins need to be addressed.
PARTS REQUIRED
TOOLS REQUIRED
None
3mm Allen Key
Note:
The number of joint plates, clutch plates and belt clamp plates that need to be
removed will depend on the position of the part requiring servicing.
Side Cover Fixing Tang
Joint Plate
Top Conveyor Coupling Plate
Feeder Belt Clamp Plate
Feeder Clutch Plate
Содержание DigiVAC
Страница 16: ...10 Watkiss DigiVAC Service Manual Issue 2 29 11 04 Overview Fuses...
Страница 136: ...130 Watkiss DigiVAC Service Manual Issue 2 29 11 04 Trouble Shooting...
Страница 140: ...134 Watkiss DigiVAC Service Manual Issue 2 29 11 04 Appendix...
Страница 141: ......