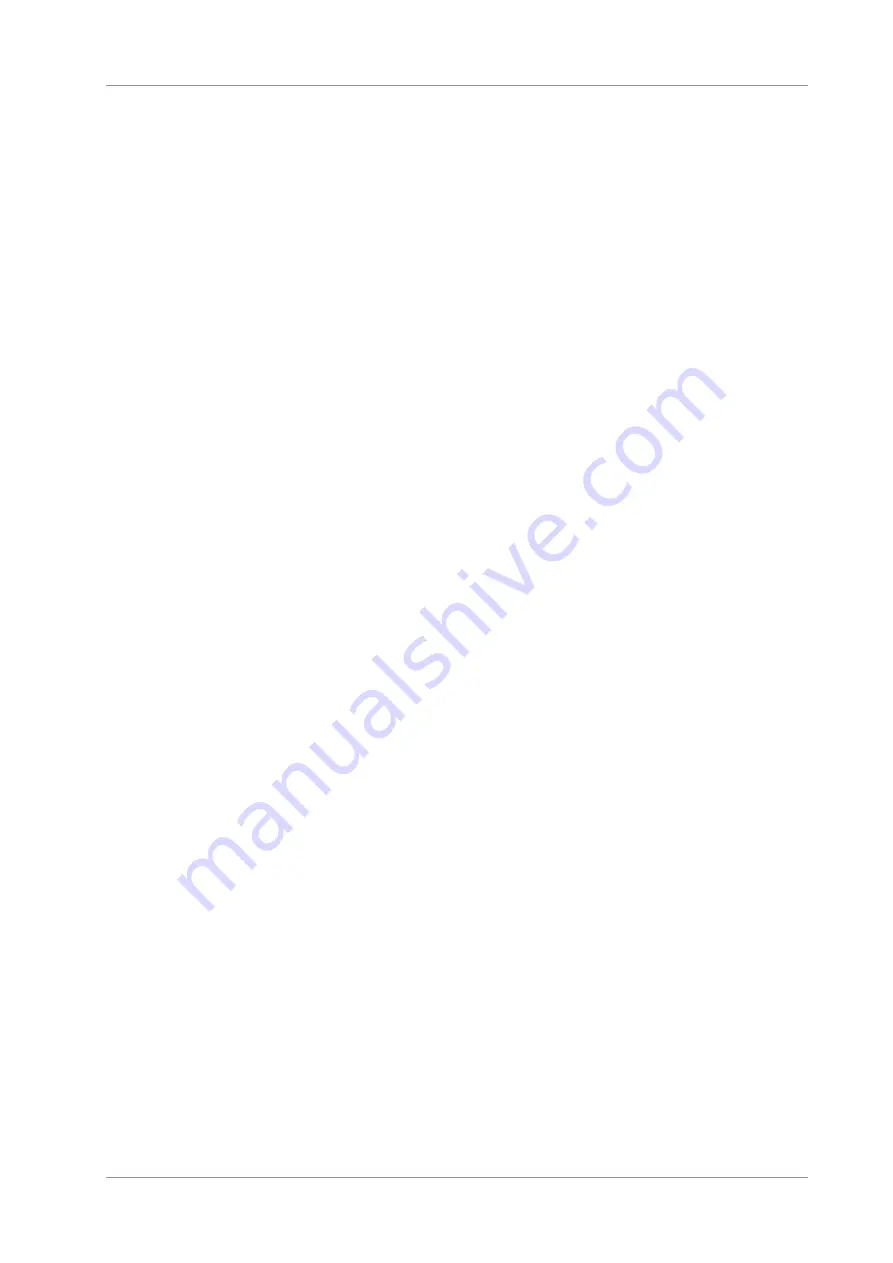
3
•
Device Overview
Pumps C, Pumps F ( VC-Pxx, VF-Pxx)
Operating Manual
Page 33
3.2
Operating Principle
General Information
The pump is a serial dual-piston pump with electronic compressibility
compensation for precise and virtually pulse-free flow.
The pump head comprises a working cylinder and an equilibration
cylinder that are connected in series. Thus, the solvent passes both
cylinders successively. To achieve continuous delivery, the working
cylinder delivers while the equilibration cylinder is filled simultaneously.
The equilibration cylinder serves as the reservoir and delivers while the
working cylinder performs the intake stroke.
When delivering compressible liquids without controlled pre-
compression, pulsation increases along with the increasing working
pressure because part of the delivery stroke is required for compressing
the liquid in the working cylinder. Pulsation during the pre-compression
phase is reduced to a minimum by velocity modulation of the drive.
Highly constant delivery is ensured by a patented secondary control
system (automatic compressibility compensation). The flow rate at
atmospheric pressure is always kept constant.
Pump-Specific Information
•
Pumps with vacuum degasser
The vacuum degasser enhances the flow stability and allows best
detector sensitivity by continuously removing dissolved gasses that
may be trapped in the solvents.
•
Pumps with mixing system
The mixing system ensures smoother baselines by combining and
premixing the solvent streams in the capillary mixer and improving
the mixing quality further in the static mixer.
•
For pump-specific pictures that illustrate how the pump operates,
see
Содержание thermoscientific Vanquish Pumps C
Страница 4: ...Contacting Us Page 4 Pumps C Pumps F VC Pxx VF Pxx Operating Manual ...
Страница 30: ...2 Safety Page 30 Pumps C Pumps F VC Pxx VF Pxx Operating Manual ...
Страница 40: ...3 Device Overview Page 40 Pumps C Pumps F VC Pxx VF Pxx Operating Manual ...
Страница 196: ...7 Maintenance and Service Page 196 Pumps C Pumps F VC Pxx VF Pxx Operating Manual ...
Страница 214: ...8 Troubleshooting Page 214 Pumps C Pumps F VC Pxx VF Pxx Operating Manual ...
Страница 284: ...12 Accessories Consumables and Replacement Parts Page 284 Pumps C Pumps F VC Pxx VF Pxx Operating Manual ...
Страница 290: ...13 Appendix Page 290 Pumps C Pumps F VC Pxx VF Pxx Operating Manual ...
Страница 296: ...Thermo Fisher Scientific Inc 168 Third Avenue Waltham Massachusetts 02451 USA www thermofisher com ...