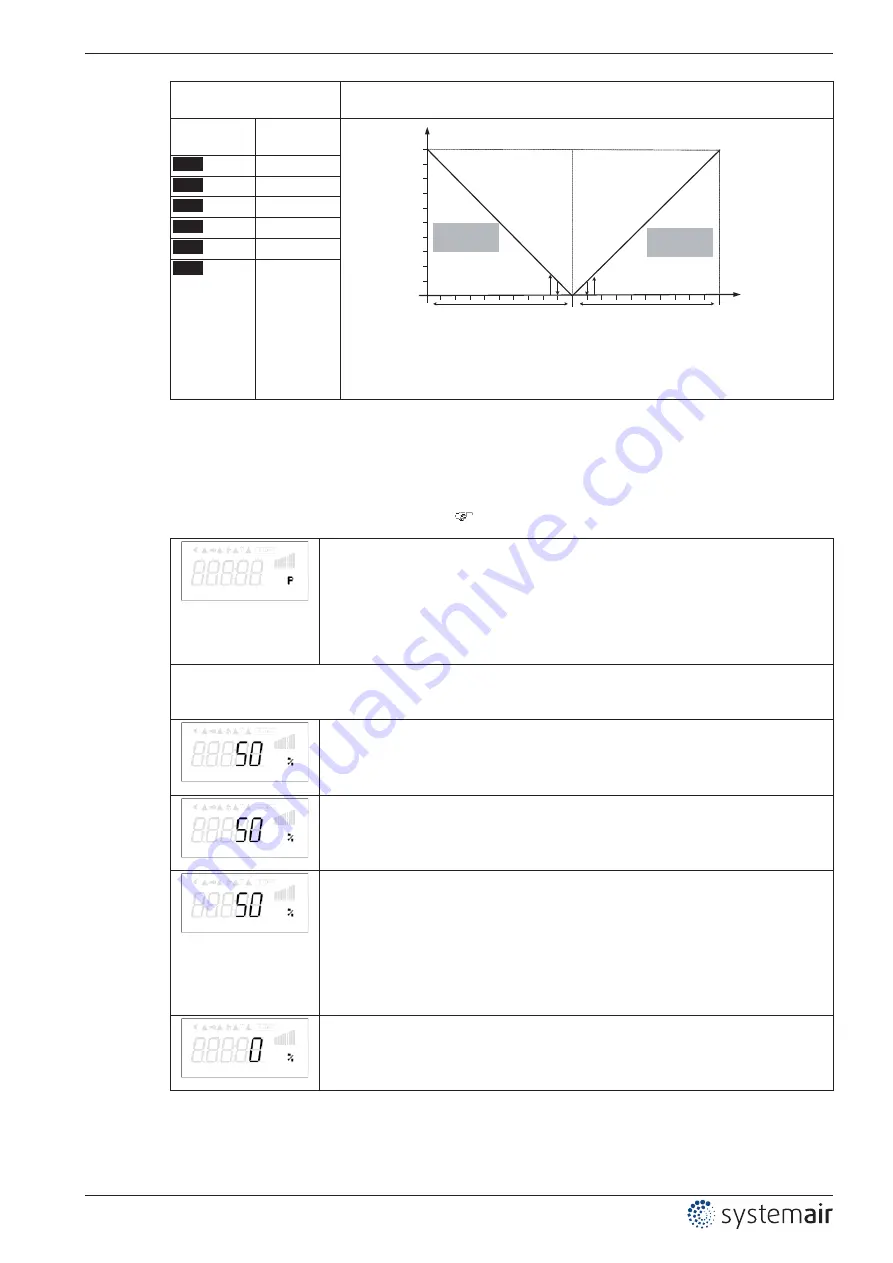
Factory setting depending
on selected mode
Example for temperature control (Idealized principle diagram)
Mode
Controller
function
nM
100 %
I
S
R
R
OFF
ON
10.05.2007
v_umkehr_regelfunktion.vsd
nM
Motor speed
R
Pband
S
Setpoint
I
Actual value
OFF
for Val > Set = n+ = heating function
ON
for Val > Set = n+ = cooling function
1.01
non
2.01
...
ON
3.01
...
ON
4.01
...
OFF
5.01
...
OFF
6.01
...
OFF
9.8.10
Controller con
fi
guration
The
“
controller con
fi
guration
”
is automatically carried out during selection of the application related
mode of operation (Base setup). The factory presets in accordance with the mode of operation are
based on many years of experience, which is suitable for many applications. Under special circum-
stances, these can be individually adapted (
Menu group
“
setting
”
).
Type of control
The type of control determines the method with which the controlled value behaves in
case of a difference between the target and current values. For this, the control
technology has standard algorithms, which consist of a combination of three methods:
Selection P, PID:
•
P
control (Proportional component, proportion of the absolute deviation)
•
I
control (Integral component, proportion of the sum of all deviations)
•
D
control (Differential component, proportion of the last difference)
With pure P controllers (controller type
P
), the following described settings do not have any function.
If needed, the most suitable combination for the respective control system can be determined from these
proportions.
KP
P-component = reaction time
Setting range: 0 - 200 %
smaller = more slowly
bigger = faster
KI
I-component = accuracy, correction time
Setting range: 0 - 200 %
bigger = faster
smaller = more slowly
KD
D-component
More
“
D-component
”
causes more stability by a clean actual value signal with shorter
correction times
By a actual value signal with a superposition should be done to attitude without
“
D-
component
”
→
0 %
Setting range: 0 - 200 %
value smaller = less
“
D-component
”
value higher = more
“
D-component
”
TI
Integration time = correction time
Setting range: 0 - 200 %
smaller = faster
bigger = more slowly
Operating Instructions
REPT6 / REPT10
Programming
L-BAL-E081-GB 1237 Index 002
Part.-No. 00163316-GB
43/67