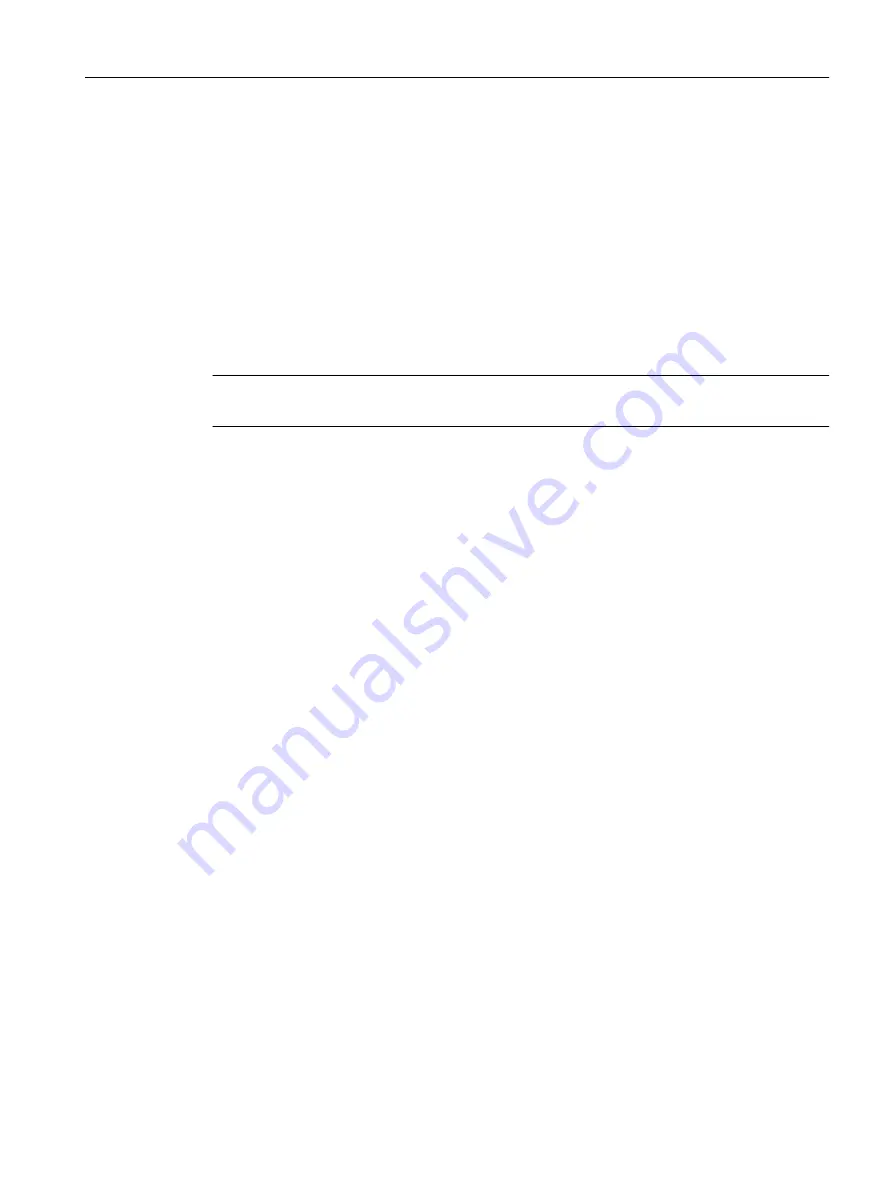
10.6.5
Subroutines
If you require the same machining steps when programming different workpieces, you can
define these machining steps in a separate subprogram. You can then call this subprogram
in any program.
Identical machining steps therefore only have to be programmed once.
A distinction is not made between the main program and subprograms. This means that you
can call a "standard" ShopMill or G code program in another ShopMill program as a
subprogram.
You can also call another subprogram in the subprogram. The maximum nesting depth is 15
subprograms.
Note
You cannot insert subprograms into linked blocks.
If you want to call a ShopMill program as a subprogram, the program must already have been
calculated once (load or simulate program in the "Machine Auto" mode). This is not necessary
for G code subprograms.
Program clipboard
If you use the "Execution from external storage (EES)" software option, the subprogram can
be stored locally or externally in an arbitrary program memory configured for EES.
If you use the "CNC user memory extended" software option, the subprogram can be stored
on the system CF card in a program memory configured for EES.
Without these two software options, the subprogram must always be stored in the NCK work
memory (in a separate "XYZ" directory or in the "Subprograms" directory). If you still want to
call a subprogram located on another drive, you can use G code command "EXTCALL".
Program header
Please note that when a subprogram is called, the settings in the program header of the
subprogram are evaluated. These settings also remain active even after the subprogram has
ended.
If you wish to activate the settings from the program header of the main program again, you
can make the settings again in the main program after calling the subprogram.
Procedure
1.
Generate a ShopMill or G code program that you wish to call as a sub‐
program in another program.
2.
Position the cursor in the work plan or in the program view of the main
program on the program block after which you wish to call the subpro‐
gram.
Programming technological functions (cycles)
10.6 Further cycles and functions
Milling
Operating Manual, 08/2018, 6FC5398-7CP41-0BA0
651
Содержание SINUMERIK 828D Turning
Страница 68: ...Introduction 2 4 User interface Milling 68 Operating Manual 08 2018 6FC5398 7CP41 0BA0 ...
Страница 162: ...Setting up the machine 4 12 MDA Milling 162 Operating Manual 08 2018 6FC5398 7CP41 0BA0 ...
Страница 270: ...Machining the workpiece 6 17 Setting for automatic mode Milling 270 Operating Manual 08 2018 6FC5398 7CP41 0BA0 ...
Страница 278: ...Swivel combination 45 90 Simulating machining 7 1 Overview Milling 278 Operating Manual 08 2018 6FC5398 7CP41 0BA0 ...
Страница 294: ...Simulating machining 7 9 Displaying simulation alarms Milling 294 Operating Manual 08 2018 6FC5398 7CP41 0BA0 ...
Страница 316: ...Generating a G code program 8 10 Measuring cycle support Milling 316 Operating Manual 08 2018 6FC5398 7CP41 0BA0 ...
Страница 684: ...Collision avoidance 12 2 Set collision avoidance Milling 684 Operating Manual 08 2018 6FC5398 7CP41 0BA0 ...
Страница 746: ...Tool management 13 16 Working with Multitool Milling 746 Operating Manual 08 2018 6FC5398 7CP41 0BA0 ...
Страница 830: ...Alarm error and system messages 15 9 Remote diagnostics Milling 830 Operating Manual 08 2018 6FC5398 7CP41 0BA0 ...
Страница 846: ... Working with Manual Machine 16 7 More complex machining Milling 846 Operating Manual 08 2018 6FC5398 7CP41 0BA0 ...
Страница 870: ...HT 8 840D sl only 18 5 Calibrating the touch panel Milling 870 Operating Manual 08 2018 6FC5398 7CP41 0BA0 ...
Страница 890: ...Easy Message 828D only 20 7 Making settings for Easy Message Milling 890 Operating Manual 08 2018 6FC5398 7CP41 0BA0 ...
Страница 924: ...Edit PLC user program 828D only 23 8 Searching for operands Milling 924 Operating Manual 08 2018 6FC5398 7CP41 0BA0 ...
Страница 925: ...Appendix A A 1 840D sl 828D documentation overview Milling Operating Manual 08 2018 6FC5398 7CP41 0BA0 925 ...