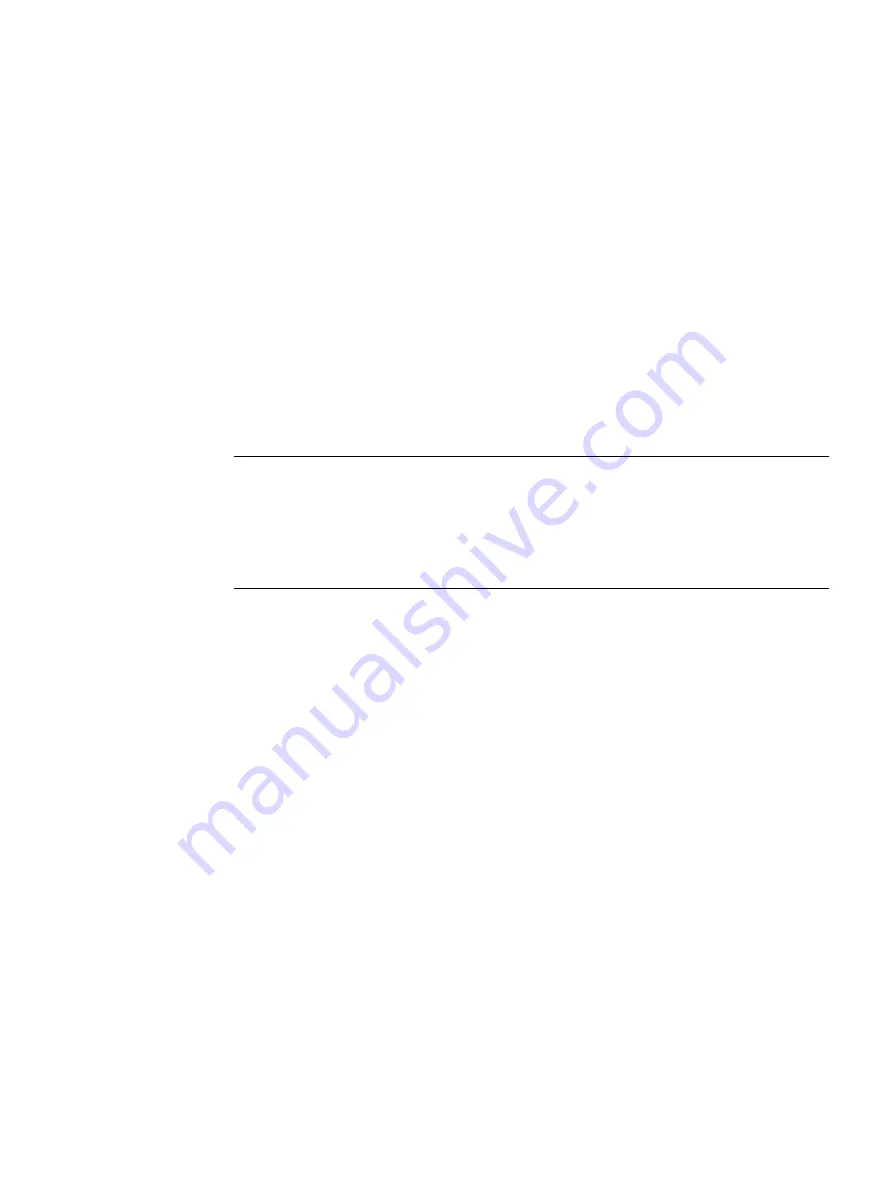
Programming technological functions (cycles)
10
10.1
Drilling
10.1.1
General
General geometry parameters
● Retraction plane RP and reference point Z0
Normally, reference point Z0 and retraction plane RP have different values. The cycle
assumes that the retraction plane is in front of the reference point.
Note
If the values for reference point and retraction planes are identical, a relative depth
specification is not permitted. Error message "Reference plane defined incorrectly" is output
and the cycle is not executed.
This error message is also output if the retraction plane is located after the reference point,
i.e. its distance to the final drilling depth is smaller.
● Safety clearance SC
Acts in relation to the reference point. The direction in which the safety clearance is active
is automatically determined by the cycle.
● Drilling depth
Depending on the selection of the drill shank or drill tip or the centering diameter, the
programmed drilling depth refers to the following for cycles with a selection field:
– Tip (drilling depth in relation to the tip)
The drill is inserted into the workpiece until the drill tip reaches the value programmed
for Z1.
– Shank (drilling depth in relation to the shank)
The drill is inserted into the workpiece until the drill shank reaches the value programmed
for Z1. The angle entered in the tool list is taken into account.
– Diameter (centering in relation to the diameter, only for CYCLE81)
The diameter of the centering hole is programmed at Z1. In this case, the tip angle of
the tool must be specified in the tool list. The drill is inserted into the workpiece until the
specified diameter is reached.
Drilling positions
The cycle assumes the tested hole coordinates of the plane.
Milling
Operating Manual, 08/2018, 6FC5398-7CP41-0BA0
371
Содержание SINUMERIK 828D Turning
Страница 68: ...Introduction 2 4 User interface Milling 68 Operating Manual 08 2018 6FC5398 7CP41 0BA0 ...
Страница 162: ...Setting up the machine 4 12 MDA Milling 162 Operating Manual 08 2018 6FC5398 7CP41 0BA0 ...
Страница 270: ...Machining the workpiece 6 17 Setting for automatic mode Milling 270 Operating Manual 08 2018 6FC5398 7CP41 0BA0 ...
Страница 278: ...Swivel combination 45 90 Simulating machining 7 1 Overview Milling 278 Operating Manual 08 2018 6FC5398 7CP41 0BA0 ...
Страница 294: ...Simulating machining 7 9 Displaying simulation alarms Milling 294 Operating Manual 08 2018 6FC5398 7CP41 0BA0 ...
Страница 316: ...Generating a G code program 8 10 Measuring cycle support Milling 316 Operating Manual 08 2018 6FC5398 7CP41 0BA0 ...
Страница 684: ...Collision avoidance 12 2 Set collision avoidance Milling 684 Operating Manual 08 2018 6FC5398 7CP41 0BA0 ...
Страница 746: ...Tool management 13 16 Working with Multitool Milling 746 Operating Manual 08 2018 6FC5398 7CP41 0BA0 ...
Страница 830: ...Alarm error and system messages 15 9 Remote diagnostics Milling 830 Operating Manual 08 2018 6FC5398 7CP41 0BA0 ...
Страница 846: ... Working with Manual Machine 16 7 More complex machining Milling 846 Operating Manual 08 2018 6FC5398 7CP41 0BA0 ...
Страница 870: ...HT 8 840D sl only 18 5 Calibrating the touch panel Milling 870 Operating Manual 08 2018 6FC5398 7CP41 0BA0 ...
Страница 890: ...Easy Message 828D only 20 7 Making settings for Easy Message Milling 890 Operating Manual 08 2018 6FC5398 7CP41 0BA0 ...
Страница 924: ...Edit PLC user program 828D only 23 8 Searching for operands Milling 924 Operating Manual 08 2018 6FC5398 7CP41 0BA0 ...
Страница 925: ...Appendix A A 1 840D sl 828D documentation overview Milling Operating Manual 08 2018 6FC5398 7CP41 0BA0 925 ...