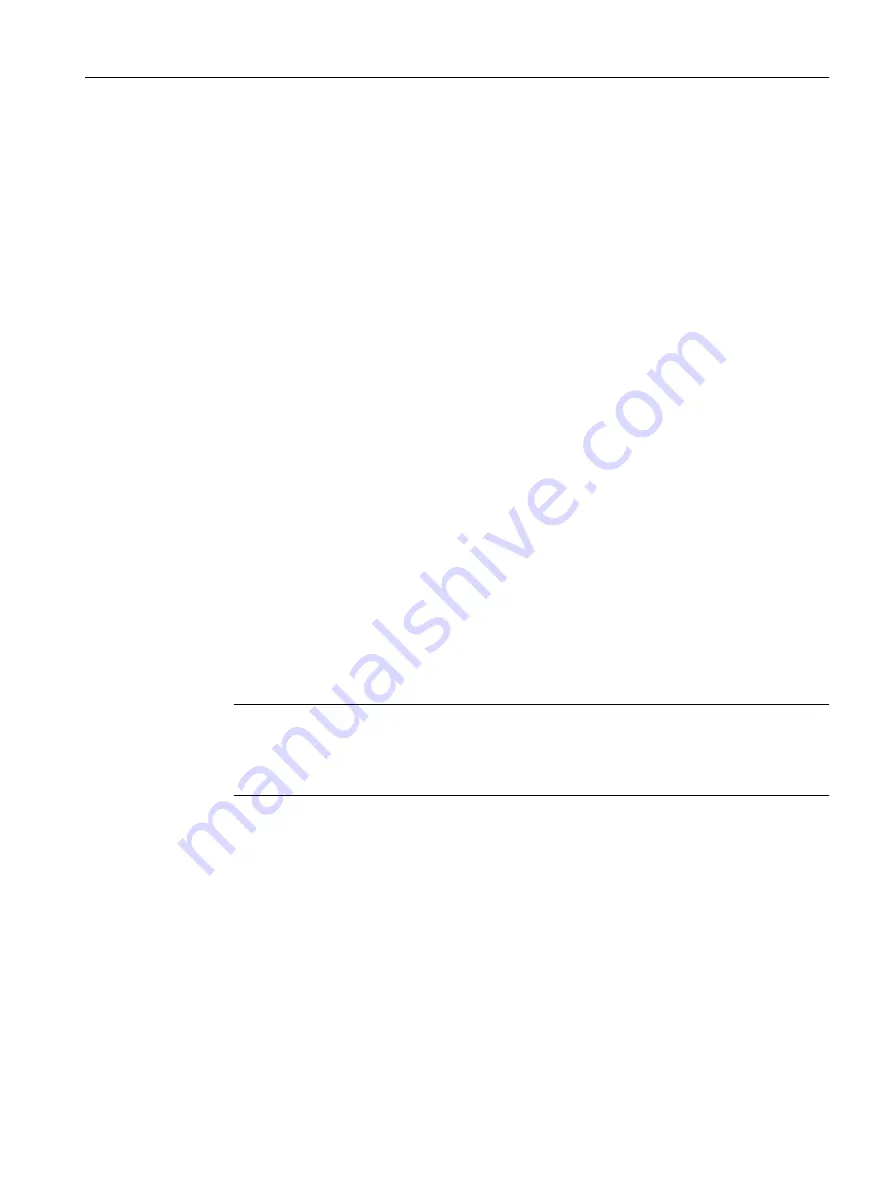
● Axis by axis
In the case of axis-by-axis swiveling, the coordinate system is rotated about each axis in
turn, with each rotation starting from the previous rotation. The axis sequence can be freely
selected.
● Solid angle
With the solid angle swiveling option, the tool is first rotated about the Z axis and then about
the Y axis. The second rotation starts from the first.
● Projection angle
When swiveling using the projection angle, the angle value of the swiveled surface is
projected onto the first two axes of the right-angle coordinate system. The user can freely
select the axis rotation sequence.
The 3rd rotation is based on the previous rotation. The active plane and the tool orientation
must be taken into consideration when the projection angle is used:
– For G17 projection angle XY, 3rd rotation around Z
– For G18 projection angle ZX, 3rd rotation around Y
– For G19 projection angle YZ, 3rd rotation around X
When projection angles around XY and YX are programmed, the new X-axis of the swiveled
coordinate system lies in the old ZX plane.
When projection angles around XZ and ZX are programmed, the new Z-axis of the swiveled
coordinate system lies in the old Y-Z plane.
When projection angles around YZ and ZY are programmed, the new Y-axis of the swiveled
coordinate system lies in the old X-Y plane.
● directly
For direct swiveling, the required positions of the rotary axes are specified. The HMI
calculates a suitable new coordinate system based on these values. The tool axis is aligned
in the Z direction. You can derive the resulting direction of the X and Y axis by traversing
the axes.
Note
Direction of rotation
The positive direction of each rotation for the different swivel versions is shown in the help
displays.
Axis sequence
Sequence of the axes which are rotated around:
XYZ or XZY or YXZ or YZX or ZXY or ZYX
Programming technological functions (cycles)
10.6 Further cycles and functions
Milling
Operating Manual, 08/2018, 6FC5398-7CP41-0BA0
635
Содержание SINUMERIK 828D Turning
Страница 68: ...Introduction 2 4 User interface Milling 68 Operating Manual 08 2018 6FC5398 7CP41 0BA0 ...
Страница 162: ...Setting up the machine 4 12 MDA Milling 162 Operating Manual 08 2018 6FC5398 7CP41 0BA0 ...
Страница 270: ...Machining the workpiece 6 17 Setting for automatic mode Milling 270 Operating Manual 08 2018 6FC5398 7CP41 0BA0 ...
Страница 278: ...Swivel combination 45 90 Simulating machining 7 1 Overview Milling 278 Operating Manual 08 2018 6FC5398 7CP41 0BA0 ...
Страница 294: ...Simulating machining 7 9 Displaying simulation alarms Milling 294 Operating Manual 08 2018 6FC5398 7CP41 0BA0 ...
Страница 316: ...Generating a G code program 8 10 Measuring cycle support Milling 316 Operating Manual 08 2018 6FC5398 7CP41 0BA0 ...
Страница 684: ...Collision avoidance 12 2 Set collision avoidance Milling 684 Operating Manual 08 2018 6FC5398 7CP41 0BA0 ...
Страница 746: ...Tool management 13 16 Working with Multitool Milling 746 Operating Manual 08 2018 6FC5398 7CP41 0BA0 ...
Страница 830: ...Alarm error and system messages 15 9 Remote diagnostics Milling 830 Operating Manual 08 2018 6FC5398 7CP41 0BA0 ...
Страница 846: ... Working with Manual Machine 16 7 More complex machining Milling 846 Operating Manual 08 2018 6FC5398 7CP41 0BA0 ...
Страница 870: ...HT 8 840D sl only 18 5 Calibrating the touch panel Milling 870 Operating Manual 08 2018 6FC5398 7CP41 0BA0 ...
Страница 890: ...Easy Message 828D only 20 7 Making settings for Easy Message Milling 890 Operating Manual 08 2018 6FC5398 7CP41 0BA0 ...
Страница 924: ...Edit PLC user program 828D only 23 8 Searching for operands Milling 924 Operating Manual 08 2018 6FC5398 7CP41 0BA0 ...
Страница 925: ...Appendix A A 1 840D sl 828D documentation overview Milling Operating Manual 08 2018 6FC5398 7CP41 0BA0 925 ...