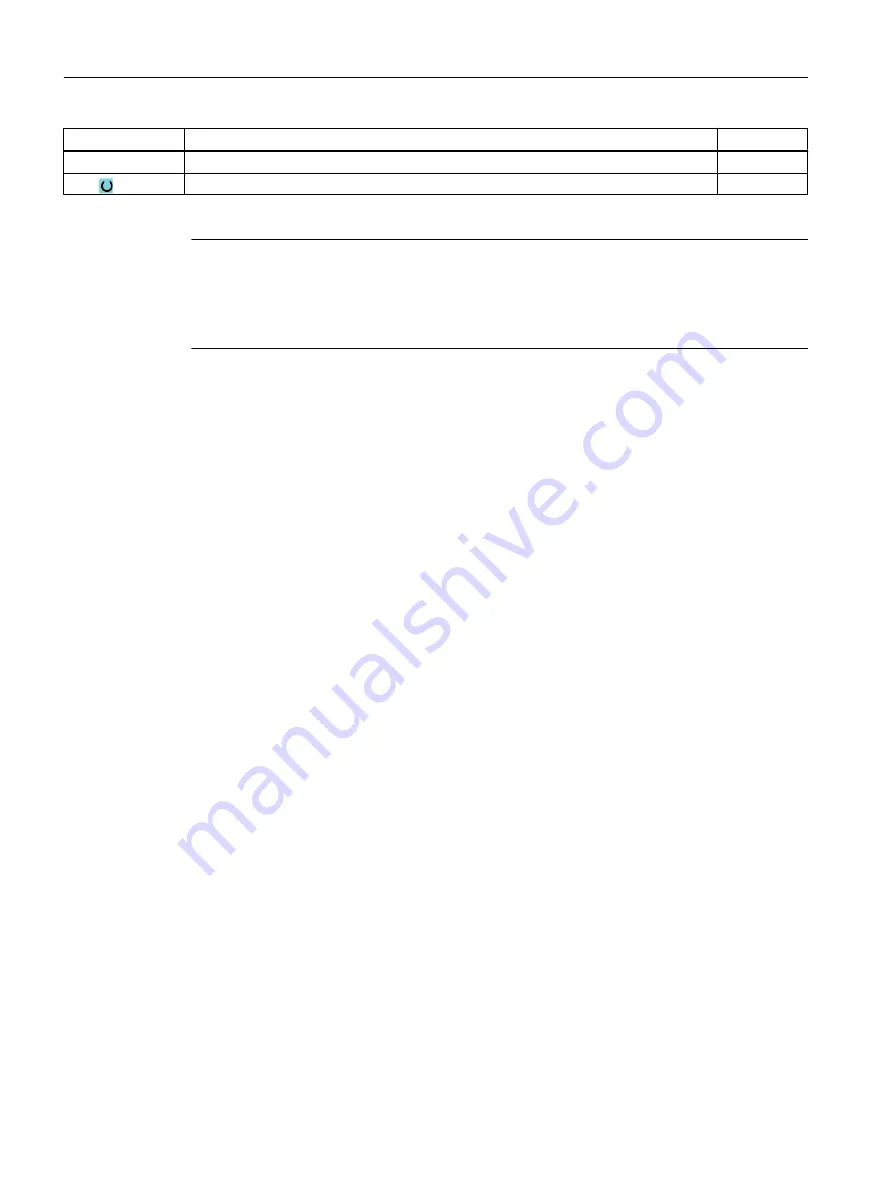
Parameter
Description
Unit
FS
Chamfer width for chamfering - (only for chamfering machining)
mm
ZFS
Insertion depth of tool tip (abs or inc) - (for machining only)
mm
* Unit of feedrate as programmed before the cycle call
Note
Cylinder surface transformation with slot side compensation
For cylinder surface transformation with selected slot side compensation and approach/
retraction in quadrant or semi-circle, the approach/retraction radius must be greater than
“Offset to programmed path – tool radius”.
10.3.8
Contour pocket/contour spigot (CYCLE63/64)
Contours for pockets or islands
Contours for pockets or islands must be closed, i.e. the starting point and end point of the
contour are identical. You can also mill pockets that contain one or more islands. The islands
can also be located partially outside the pocket or overlap each other. The first contour you
specify is interpreted as the pocket contour and all the others as islands.
Automatic calculation / manual input of the starting point
Using "Automatic starting point" you have the option of calculating the optimum plunge point.
By selecting "Manual starting point", you define the plunge point in the parameter screen.
If the islands and the miller diameter, which must be plunged at various locations, are obtained
from the pocket contour, then the manual entry only defines the first plunge point; the remaining
plunge points are automatically calculated.
Contours for spigots
Contours for spigots must be closed, i.e. the starting point and end point of the contour are
identical. You can define multiple spigots that can also overlap. The first contour specified is
interpreted as a blank contour and all others as spigots.
Machining
You program the machining of contour pockets with islands/blank contour with spigots, e.g.
as follows:
1. Enter the pocket contour/blank contour
2. Enter the island/spigot contour
3. Call the contour for pocket contour/blank contour or island/spigot contour (only for G code
program)
4. Center (this is only possible for pocket contour)
Programming technological functions (cycles)
10.3 Contour milling
Milling
496
Operating Manual, 08/2018, 6FC5398-7CP41-0BA0
Содержание SINUMERIK 828D Turning
Страница 68: ...Introduction 2 4 User interface Milling 68 Operating Manual 08 2018 6FC5398 7CP41 0BA0 ...
Страница 162: ...Setting up the machine 4 12 MDA Milling 162 Operating Manual 08 2018 6FC5398 7CP41 0BA0 ...
Страница 270: ...Machining the workpiece 6 17 Setting for automatic mode Milling 270 Operating Manual 08 2018 6FC5398 7CP41 0BA0 ...
Страница 278: ...Swivel combination 45 90 Simulating machining 7 1 Overview Milling 278 Operating Manual 08 2018 6FC5398 7CP41 0BA0 ...
Страница 294: ...Simulating machining 7 9 Displaying simulation alarms Milling 294 Operating Manual 08 2018 6FC5398 7CP41 0BA0 ...
Страница 316: ...Generating a G code program 8 10 Measuring cycle support Milling 316 Operating Manual 08 2018 6FC5398 7CP41 0BA0 ...
Страница 684: ...Collision avoidance 12 2 Set collision avoidance Milling 684 Operating Manual 08 2018 6FC5398 7CP41 0BA0 ...
Страница 746: ...Tool management 13 16 Working with Multitool Milling 746 Operating Manual 08 2018 6FC5398 7CP41 0BA0 ...
Страница 830: ...Alarm error and system messages 15 9 Remote diagnostics Milling 830 Operating Manual 08 2018 6FC5398 7CP41 0BA0 ...
Страница 846: ... Working with Manual Machine 16 7 More complex machining Milling 846 Operating Manual 08 2018 6FC5398 7CP41 0BA0 ...
Страница 870: ...HT 8 840D sl only 18 5 Calibrating the touch panel Milling 870 Operating Manual 08 2018 6FC5398 7CP41 0BA0 ...
Страница 890: ...Easy Message 828D only 20 7 Making settings for Easy Message Milling 890 Operating Manual 08 2018 6FC5398 7CP41 0BA0 ...
Страница 924: ...Edit PLC user program 828D only 23 8 Searching for operands Milling 924 Operating Manual 08 2018 6FC5398 7CP41 0BA0 ...
Страница 925: ...Appendix A A 1 840D sl 828D documentation overview Milling Operating Manual 08 2018 6FC5398 7CP41 0BA0 925 ...