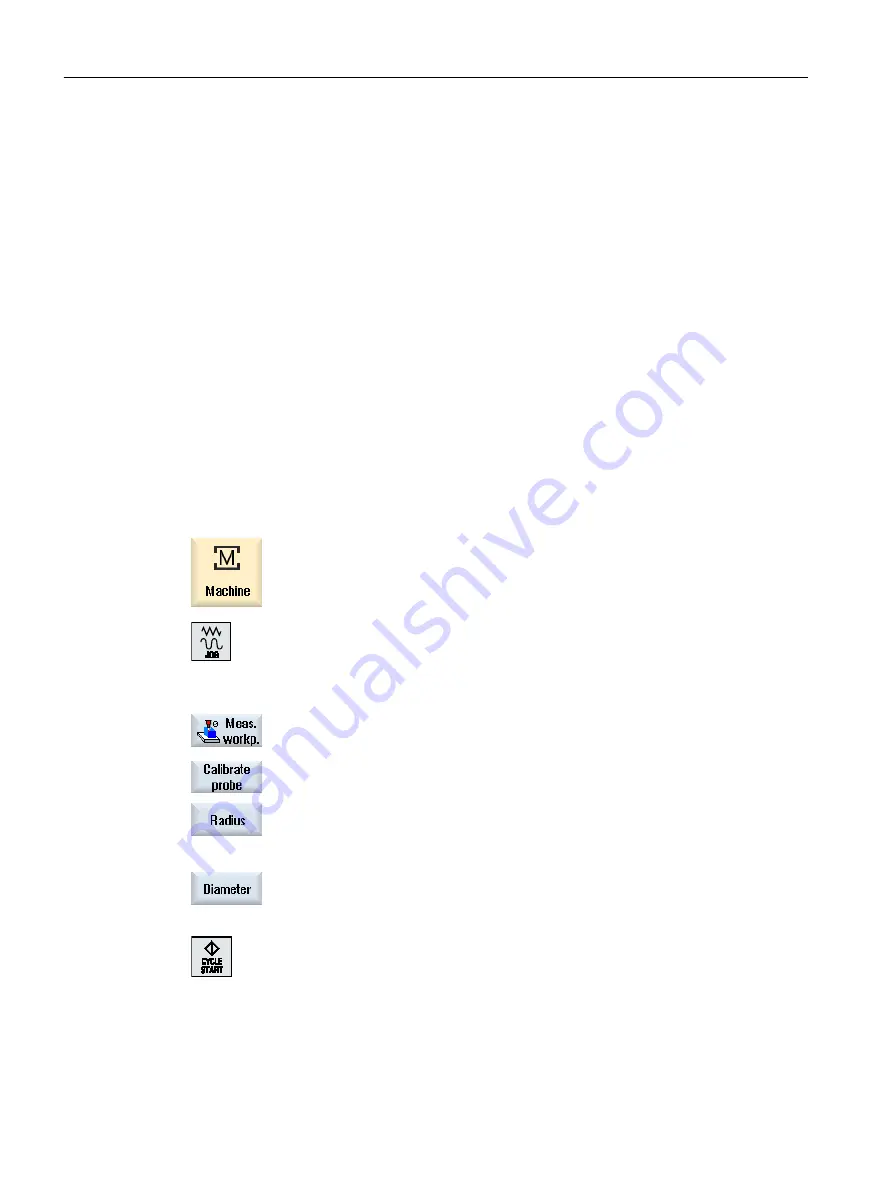
4.6.13
Calibrating the electronic workpiece probe
4.6.13.1
Calibration of length and radius or diameter
When the electronic probes are attached to the spindle, clamping tolerances usually occur.
This can lead to measurement errors.
In addition, you need to determine the trigger points of the probe relative to the spindle center
(trigger points).
Therefore, you need to calibrate the electronic probe. The radius or diameter is calibrated in
a setting ring (calibration ring) or a hole, the length is calibrated on a surface. The diameter of
the setting ring and the dimension of the surface in the Z direction (for G17) must be precisely
known and this is entered into the corresponding entry field when calibrating the probe. The
diameter of the workpiece probe ball and its length 1 must be stored in the tool list.
Procedure
1.
Load the workpiece probe into the spindle.
2.
Enter the approximate length and radius or diameter in the tool data.
Calibration of radius / diameter
3.
Select the "JOG" mode in the "Machine" operating area.
4.
Move the workpiece probe into the hole and position it at the approximate
center of the hole.
5.
Press the "Workpiece zero" and "Probe calibration" softkeys.
The window "Calibration: Probe" is opened.
- OR -
6.
Press the "Radius" or "Diameter" softkey.
Note
The "Diameter" softkey must be set up by the machine manufacturer.
7.
In ∅, enter the calibration bore corresponding to the diameter.
8.
Press the <CYCLE START> key.
Calibration starts.
When calibrating the radius, the exact hole center point is determined first.
Then the four trigger points on the inside wall of the hole are approached.
This procedure is carried out automatically twice: First with 180° (to the
starting position of the working spindle) and then in its starting position.
Setting up the machine
4.6 Measuring the workpiece zero
Milling
140
Operating Manual, 08/2018, 6FC5398-7CP41-0BA0
Содержание SINUMERIK 828D Turning
Страница 68: ...Introduction 2 4 User interface Milling 68 Operating Manual 08 2018 6FC5398 7CP41 0BA0 ...
Страница 162: ...Setting up the machine 4 12 MDA Milling 162 Operating Manual 08 2018 6FC5398 7CP41 0BA0 ...
Страница 270: ...Machining the workpiece 6 17 Setting for automatic mode Milling 270 Operating Manual 08 2018 6FC5398 7CP41 0BA0 ...
Страница 278: ...Swivel combination 45 90 Simulating machining 7 1 Overview Milling 278 Operating Manual 08 2018 6FC5398 7CP41 0BA0 ...
Страница 294: ...Simulating machining 7 9 Displaying simulation alarms Milling 294 Operating Manual 08 2018 6FC5398 7CP41 0BA0 ...
Страница 316: ...Generating a G code program 8 10 Measuring cycle support Milling 316 Operating Manual 08 2018 6FC5398 7CP41 0BA0 ...
Страница 684: ...Collision avoidance 12 2 Set collision avoidance Milling 684 Operating Manual 08 2018 6FC5398 7CP41 0BA0 ...
Страница 746: ...Tool management 13 16 Working with Multitool Milling 746 Operating Manual 08 2018 6FC5398 7CP41 0BA0 ...
Страница 830: ...Alarm error and system messages 15 9 Remote diagnostics Milling 830 Operating Manual 08 2018 6FC5398 7CP41 0BA0 ...
Страница 846: ... Working with Manual Machine 16 7 More complex machining Milling 846 Operating Manual 08 2018 6FC5398 7CP41 0BA0 ...
Страница 870: ...HT 8 840D sl only 18 5 Calibrating the touch panel Milling 870 Operating Manual 08 2018 6FC5398 7CP41 0BA0 ...
Страница 890: ...Easy Message 828D only 20 7 Making settings for Easy Message Milling 890 Operating Manual 08 2018 6FC5398 7CP41 0BA0 ...
Страница 924: ...Edit PLC user program 828D only 23 8 Searching for operands Milling 924 Operating Manual 08 2018 6FC5398 7CP41 0BA0 ...
Страница 925: ...Appendix A A 1 840D sl 828D documentation overview Milling Operating Manual 08 2018 6FC5398 7CP41 0BA0 925 ...