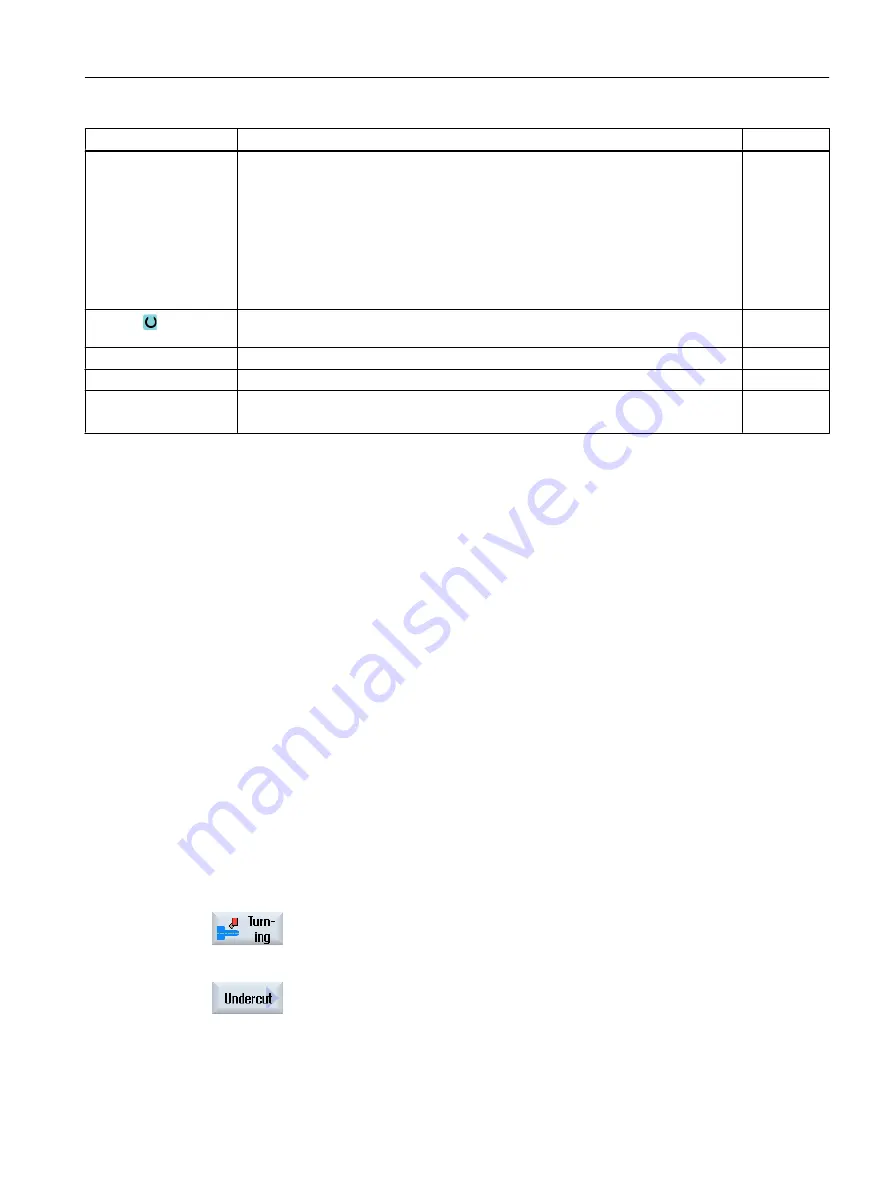
Parameter
Description
Unit
D
● Maximum depth infeed for insertion – (only for ∇ and ∇ + ∇∇∇)
● For zero: Insertion in a cut – (only for ∇ and ∇ + ∇∇∇)
D = 0: 1. cut is made directly to final depth T1
D > 0: 1st and 2nd cuts are made alternately to infeed depth D, in order to achieve
a better chip flow and prevent the tool from breaking, see approaching/retraction
when roughing.
Alternate cutting is not possible if the tool can only reach the groove base at one
position.
mm
UX or U
Finishing allowance in X or finishing allowance in X and Z – (only for ∇ and ∇ +
∇∇∇)
mm
UZ
Finishing allowance in Z – (for UX, only for ∇ and ∇ + ∇∇∇)
mm
N
Number of grooves (N = 1....65535)
DP
Distance between grooves (inc)
DP is not displayed when N = 1
mm
* Unit of feedrate as programmed before the cycle call
10.4.4
Undercut form E and F (CYCLE940)
Function
You can use the "Undercut form E" or "Undercut form F" cycle to turn form E or F undercuts
in accordance with DIN 509.
Approach/retraction
1. The tool first moves to the starting point calculated internally in the cycle at rapid traverse.
2. The undercut is made in one cut at the machining feedrate, starting from the flank through
to the cross-feed VX.
3. The tool moves back to the starting point at rapid traverse.
Procedure
1.
The part program or ShopMill program to be processed has been created
and you are in the editor.
2.
Press the "Turning" softkey.
3.
Press the "Undercut" softkey.
The "Undercut" input window opens.
4.
Select one of the following undercut cycles via the softkeys:
Programming technological functions (cycles)
10.4 Turning - milling/turning machine
Milling
Operating Manual, 08/2018, 6FC5398-7CP41-0BA0
523
Содержание SINUMERIK 828D Turning
Страница 68: ...Introduction 2 4 User interface Milling 68 Operating Manual 08 2018 6FC5398 7CP41 0BA0 ...
Страница 162: ...Setting up the machine 4 12 MDA Milling 162 Operating Manual 08 2018 6FC5398 7CP41 0BA0 ...
Страница 270: ...Machining the workpiece 6 17 Setting for automatic mode Milling 270 Operating Manual 08 2018 6FC5398 7CP41 0BA0 ...
Страница 278: ...Swivel combination 45 90 Simulating machining 7 1 Overview Milling 278 Operating Manual 08 2018 6FC5398 7CP41 0BA0 ...
Страница 294: ...Simulating machining 7 9 Displaying simulation alarms Milling 294 Operating Manual 08 2018 6FC5398 7CP41 0BA0 ...
Страница 316: ...Generating a G code program 8 10 Measuring cycle support Milling 316 Operating Manual 08 2018 6FC5398 7CP41 0BA0 ...
Страница 684: ...Collision avoidance 12 2 Set collision avoidance Milling 684 Operating Manual 08 2018 6FC5398 7CP41 0BA0 ...
Страница 746: ...Tool management 13 16 Working with Multitool Milling 746 Operating Manual 08 2018 6FC5398 7CP41 0BA0 ...
Страница 830: ...Alarm error and system messages 15 9 Remote diagnostics Milling 830 Operating Manual 08 2018 6FC5398 7CP41 0BA0 ...
Страница 846: ... Working with Manual Machine 16 7 More complex machining Milling 846 Operating Manual 08 2018 6FC5398 7CP41 0BA0 ...
Страница 870: ...HT 8 840D sl only 18 5 Calibrating the touch panel Milling 870 Operating Manual 08 2018 6FC5398 7CP41 0BA0 ...
Страница 890: ...Easy Message 828D only 20 7 Making settings for Easy Message Milling 890 Operating Manual 08 2018 6FC5398 7CP41 0BA0 ...
Страница 924: ...Edit PLC user program 828D only 23 8 Searching for operands Milling 924 Operating Manual 08 2018 6FC5398 7CP41 0BA0 ...
Страница 925: ...Appendix A A 1 840D sl 828D documentation overview Milling Operating Manual 08 2018 6FC5398 7CP41 0BA0 925 ...