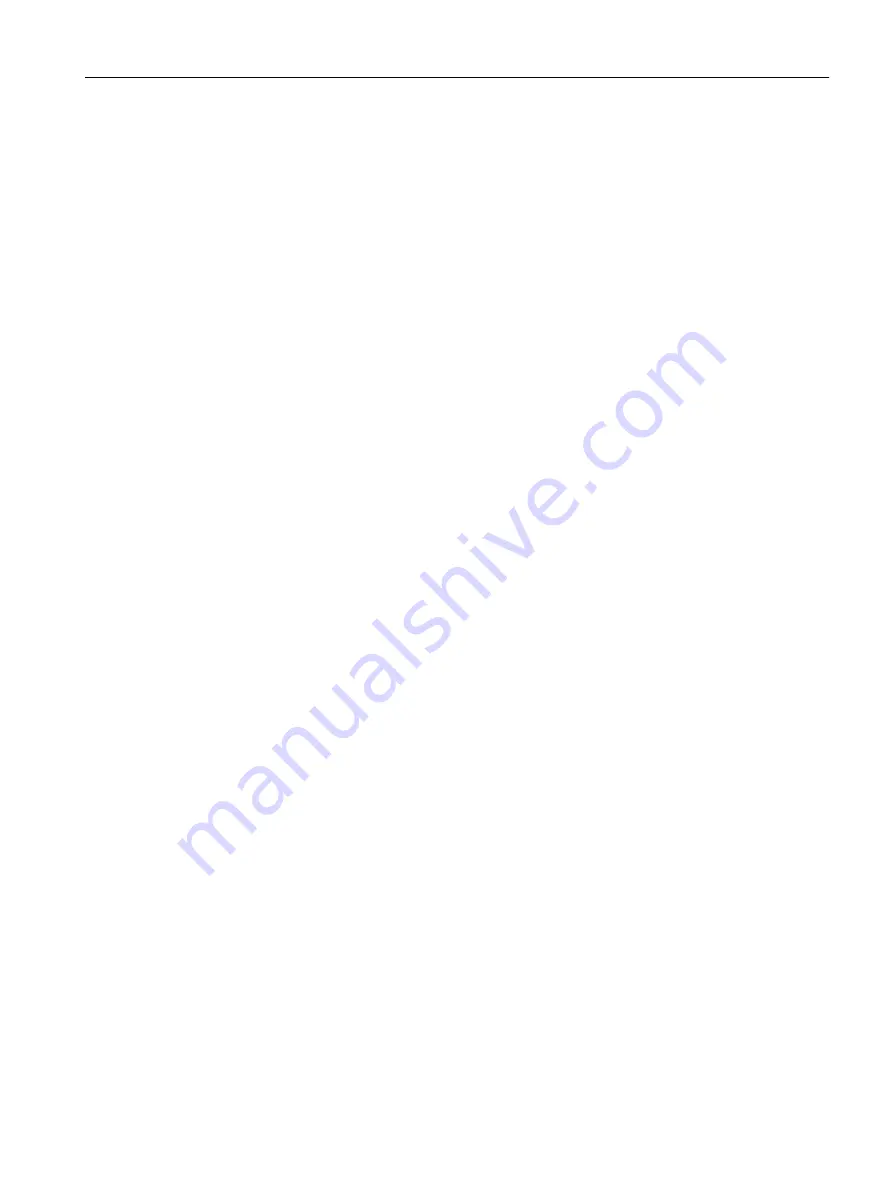
4.6
Measuring the workpiece zero
4.6.1
Overview
The reference point for programming a workpiece is always the workpiece zero. You can
determine the workpiece zero on the following workpiece elements:
● Edge (Page 121)
● Corner (Page 123)
● Pocket and hole (Page 126)
● Spigot (Page 129)
Measuring methods
You can measure the workpiece zero either manually or automatically.
Manual measurement
To measure the zero point manually, you need to traverse your tool manually up to the
workpiece. You can use edge probes, sensing probes, or dial gauges with known radii and
lengths. You can also use any other tool of which you know the radius and length.
The tools used for measuring must not be electronic probes.
Automatic measurement
For automatic measurements, only use the electronic workpiece probe, tool type 710/712. You
must calibrate the electronic workpiece probes beforehand.
In the case of automatic measuring, first position the workpiece probe manually. After starting
using the <CYCLE START> key, the workpiece probe is automatically extended to the
workpiece with the measuring feedrate. Retraction motion from the measuring point is realized
as a function of the setting data with the rapid traverse velocity or a user-specific positioning
velocity.
Logging measurement results
After you have completed the measurement, you have the option to output the displayed values
to a log. You can define whether the log file that is generated is continually written to for each
new measurement, or is overwritten.
Measuring with rotation
Under the function "Measuring with rotation" you have the option to measure without prior
calibration and without entry of a calibration data set to be used.
Setting up the machine
4.6 Measuring the workpiece zero
Milling
Operating Manual, 08/2018, 6FC5398-7CP41-0BA0
113
Содержание SINUMERIK 828D Turning
Страница 68: ...Introduction 2 4 User interface Milling 68 Operating Manual 08 2018 6FC5398 7CP41 0BA0 ...
Страница 162: ...Setting up the machine 4 12 MDA Milling 162 Operating Manual 08 2018 6FC5398 7CP41 0BA0 ...
Страница 270: ...Machining the workpiece 6 17 Setting for automatic mode Milling 270 Operating Manual 08 2018 6FC5398 7CP41 0BA0 ...
Страница 278: ...Swivel combination 45 90 Simulating machining 7 1 Overview Milling 278 Operating Manual 08 2018 6FC5398 7CP41 0BA0 ...
Страница 294: ...Simulating machining 7 9 Displaying simulation alarms Milling 294 Operating Manual 08 2018 6FC5398 7CP41 0BA0 ...
Страница 316: ...Generating a G code program 8 10 Measuring cycle support Milling 316 Operating Manual 08 2018 6FC5398 7CP41 0BA0 ...
Страница 684: ...Collision avoidance 12 2 Set collision avoidance Milling 684 Operating Manual 08 2018 6FC5398 7CP41 0BA0 ...
Страница 746: ...Tool management 13 16 Working with Multitool Milling 746 Operating Manual 08 2018 6FC5398 7CP41 0BA0 ...
Страница 830: ...Alarm error and system messages 15 9 Remote diagnostics Milling 830 Operating Manual 08 2018 6FC5398 7CP41 0BA0 ...
Страница 846: ... Working with Manual Machine 16 7 More complex machining Milling 846 Operating Manual 08 2018 6FC5398 7CP41 0BA0 ...
Страница 870: ...HT 8 840D sl only 18 5 Calibrating the touch panel Milling 870 Operating Manual 08 2018 6FC5398 7CP41 0BA0 ...
Страница 890: ...Easy Message 828D only 20 7 Making settings for Easy Message Milling 890 Operating Manual 08 2018 6FC5398 7CP41 0BA0 ...
Страница 924: ...Edit PLC user program 828D only 23 8 Searching for operands Milling 924 Operating Manual 08 2018 6FC5398 7CP41 0BA0 ...
Страница 925: ...Appendix A A 1 840D sl 828D documentation overview Milling Operating Manual 08 2018 6FC5398 7CP41 0BA0 925 ...