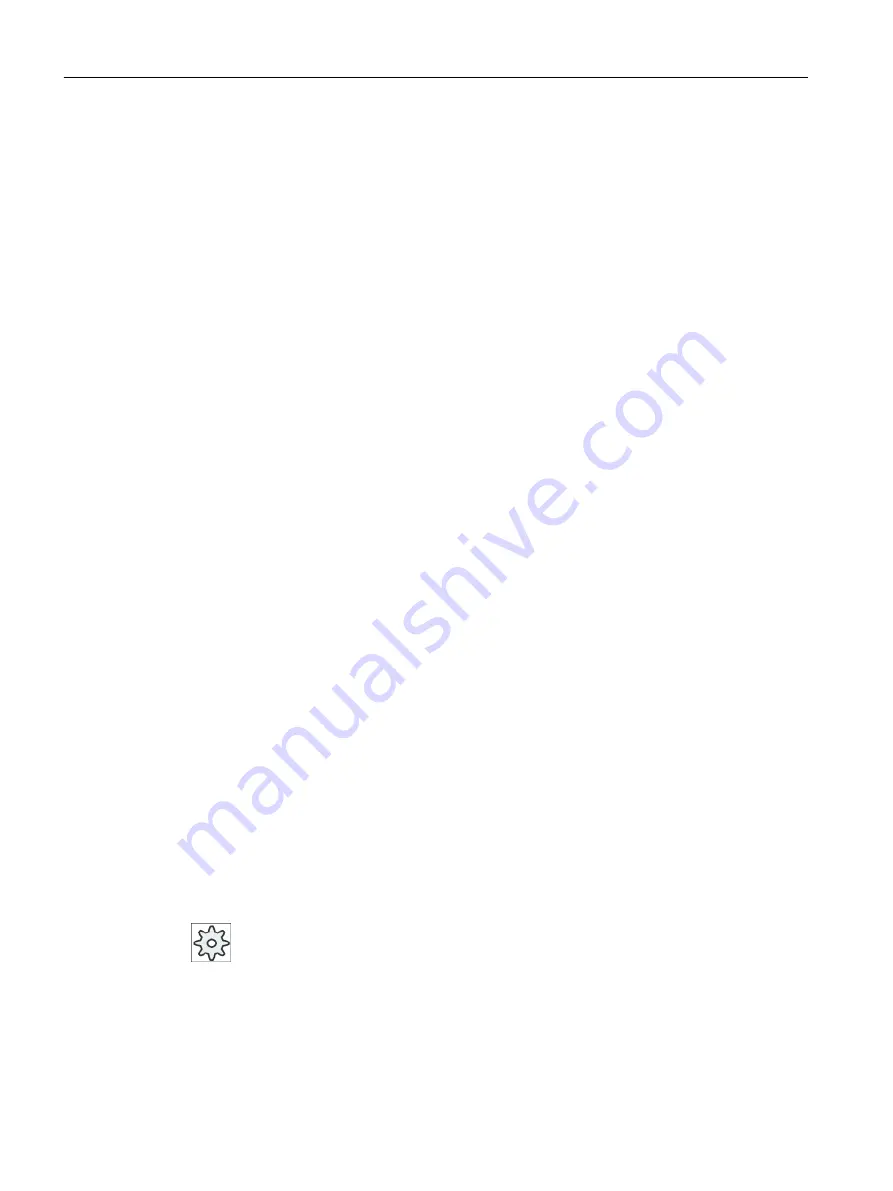
To do this, you will need a positionable spindle as well as an electronic 3D workpiece probe.
The radius of the probe ball of the electrical probe must be determined once by calibration and
entered in the tool data.
Spindle orientation of the probe in the measuring direction
In order to obtain extremely precise measurement results, you have the option to orientate the
electronic 3D probe in the measuring direction to avoid deviations regarding the rotation-
symmetric shifting characteristics. Orienting the probe is performed by positioning the working
spindle into which the probe is clamped.
To do this, you will need a positionable spindle as well as an electronic 3D workpiece probe.
Probe in a machining spindle that cannot be positioned or fixed at the machine
Also at machines without SPOS-capable spindle, you have the possibility of measuring
workpieces using electronic probes.
To do this, you will need a 3D probe (multi probe type 710). This measurement method requires
that the measuring task does not require that the spindle is positioned.
Adapting the user interface to calibrating and measuring functions
Activate the following selection options using setting data:
● Calibration plane, measurement plane
● Calibration feedrate (measuring feedrate)
● Work offset as basis for the measuring process
● Number of the probe calibration data set
● Offset target, adjustable work offset
● Offset target, basis reference
● Offset target, global basis work offset
● Offset target, channel-specific basis work offset
● Standard measuring method
● Measuring with spindle reversal
● Align probe
● The measurement method depends on the probe
Machine manufacturer
Please observe the information provided by the machine manufacturer.
Setting up the machine
4.6 Measuring the workpiece zero
Milling
114
Operating Manual, 08/2018, 6FC5398-7CP41-0BA0
Содержание SINUMERIK 828D Turning
Страница 68: ...Introduction 2 4 User interface Milling 68 Operating Manual 08 2018 6FC5398 7CP41 0BA0 ...
Страница 162: ...Setting up the machine 4 12 MDA Milling 162 Operating Manual 08 2018 6FC5398 7CP41 0BA0 ...
Страница 270: ...Machining the workpiece 6 17 Setting for automatic mode Milling 270 Operating Manual 08 2018 6FC5398 7CP41 0BA0 ...
Страница 278: ...Swivel combination 45 90 Simulating machining 7 1 Overview Milling 278 Operating Manual 08 2018 6FC5398 7CP41 0BA0 ...
Страница 294: ...Simulating machining 7 9 Displaying simulation alarms Milling 294 Operating Manual 08 2018 6FC5398 7CP41 0BA0 ...
Страница 316: ...Generating a G code program 8 10 Measuring cycle support Milling 316 Operating Manual 08 2018 6FC5398 7CP41 0BA0 ...
Страница 684: ...Collision avoidance 12 2 Set collision avoidance Milling 684 Operating Manual 08 2018 6FC5398 7CP41 0BA0 ...
Страница 746: ...Tool management 13 16 Working with Multitool Milling 746 Operating Manual 08 2018 6FC5398 7CP41 0BA0 ...
Страница 830: ...Alarm error and system messages 15 9 Remote diagnostics Milling 830 Operating Manual 08 2018 6FC5398 7CP41 0BA0 ...
Страница 846: ... Working with Manual Machine 16 7 More complex machining Milling 846 Operating Manual 08 2018 6FC5398 7CP41 0BA0 ...
Страница 870: ...HT 8 840D sl only 18 5 Calibrating the touch panel Milling 870 Operating Manual 08 2018 6FC5398 7CP41 0BA0 ...
Страница 890: ...Easy Message 828D only 20 7 Making settings for Easy Message Milling 890 Operating Manual 08 2018 6FC5398 7CP41 0BA0 ...
Страница 924: ...Edit PLC user program 828D only 23 8 Searching for operands Milling 924 Operating Manual 08 2018 6FC5398 7CP41 0BA0 ...
Страница 925: ...Appendix A A 1 840D sl 828D documentation overview Milling Operating Manual 08 2018 6FC5398 7CP41 0BA0 925 ...