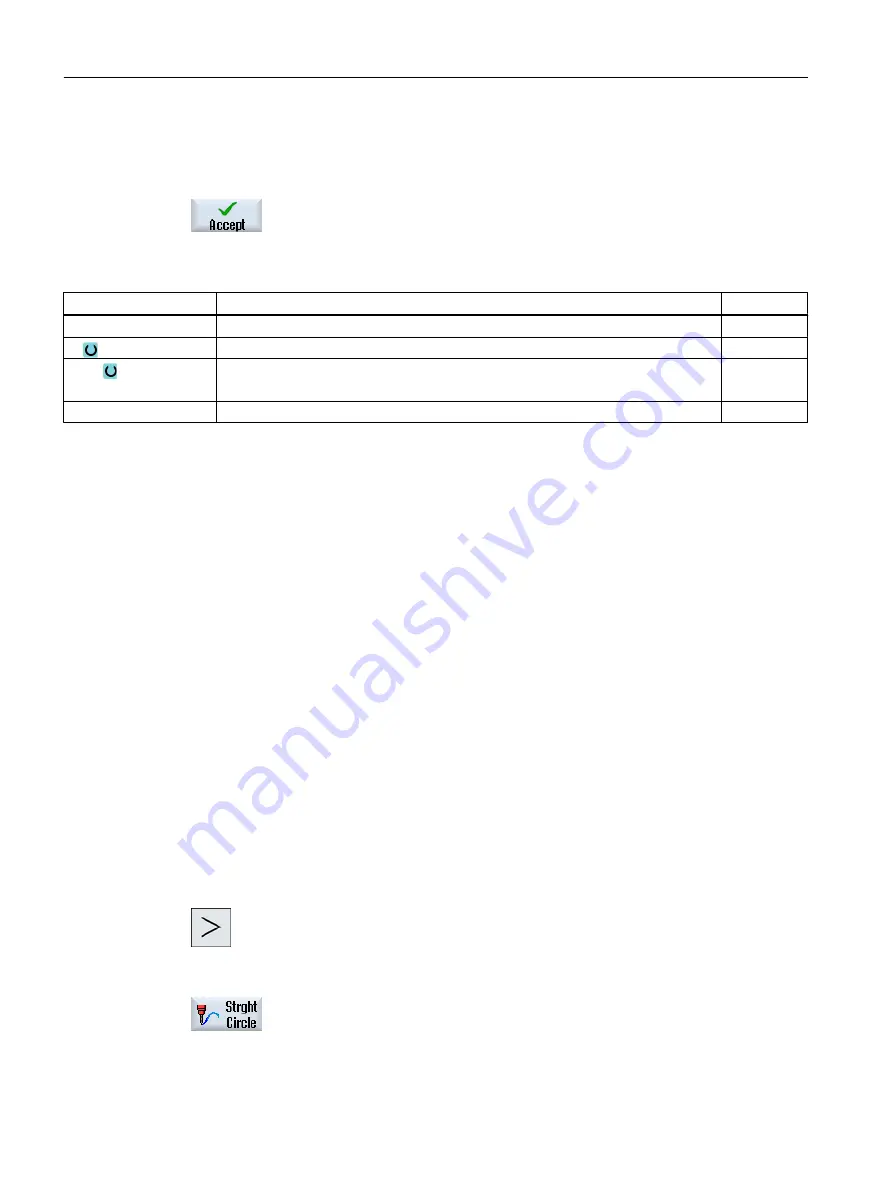
5.
Select the tool cutting edge number D if the tool has several cutting edges.
6.
Enter the spindle speed or cutting rate.
7.
Enter an allowance in the "DR" field.
Press the "Accept" softkey.
The values are saved and the parameterization screen form is closed.
The process plan is displayed and the newly generated program block is
marked.
Parameter
Description
Unit
T
Tool name
D
Cutting edge number
S / V
Spindle speed or
Constant cutting rate
rev/min
m/min
DR
Allowance, tool radius
mm
10.7.8
Programming a straight line
The tool moves at the programmed feedrate or with rapid traverse from its actual position to
the programmed end position.
Radius compensation
Alternatively, you can implement the straight line with radius compensation. The radius
compensation acts modally, therefore you must deactivate the radius compensation again
when you want to traverse without radius compensation. Where several straight line blocks
with radius compensation are programmed sequentially, you may only select radius
compensation in the first program block.
When executing the first path motion with radius compensation, the tool traverses without
compensation at the starting point and with compensation at the end point. This means that if
a vertical path is programmed, the tool traverses an oblique path. The compensation is not
applied over the entire traversing path until the second programmed path motion with radius
compensation is executed. The reverse effect occurs when radius compensation is
deactivated.
Procedure
1.
The ShopMill program to be edited has been created and you are in the
editor.
2.
Press the menu forward key and the "Straight Circle" softkey.
Programming technological functions (cycles)
10.7 Additional cycles and functions in ShopMill
Milling
662
Operating Manual, 08/2018, 6FC5398-7CP41-0BA0
Содержание SINUMERIK 828D Turning
Страница 68: ...Introduction 2 4 User interface Milling 68 Operating Manual 08 2018 6FC5398 7CP41 0BA0 ...
Страница 162: ...Setting up the machine 4 12 MDA Milling 162 Operating Manual 08 2018 6FC5398 7CP41 0BA0 ...
Страница 270: ...Machining the workpiece 6 17 Setting for automatic mode Milling 270 Operating Manual 08 2018 6FC5398 7CP41 0BA0 ...
Страница 278: ...Swivel combination 45 90 Simulating machining 7 1 Overview Milling 278 Operating Manual 08 2018 6FC5398 7CP41 0BA0 ...
Страница 294: ...Simulating machining 7 9 Displaying simulation alarms Milling 294 Operating Manual 08 2018 6FC5398 7CP41 0BA0 ...
Страница 316: ...Generating a G code program 8 10 Measuring cycle support Milling 316 Operating Manual 08 2018 6FC5398 7CP41 0BA0 ...
Страница 684: ...Collision avoidance 12 2 Set collision avoidance Milling 684 Operating Manual 08 2018 6FC5398 7CP41 0BA0 ...
Страница 746: ...Tool management 13 16 Working with Multitool Milling 746 Operating Manual 08 2018 6FC5398 7CP41 0BA0 ...
Страница 830: ...Alarm error and system messages 15 9 Remote diagnostics Milling 830 Operating Manual 08 2018 6FC5398 7CP41 0BA0 ...
Страница 846: ... Working with Manual Machine 16 7 More complex machining Milling 846 Operating Manual 08 2018 6FC5398 7CP41 0BA0 ...
Страница 870: ...HT 8 840D sl only 18 5 Calibrating the touch panel Milling 870 Operating Manual 08 2018 6FC5398 7CP41 0BA0 ...
Страница 890: ...Easy Message 828D only 20 7 Making settings for Easy Message Milling 890 Operating Manual 08 2018 6FC5398 7CP41 0BA0 ...
Страница 924: ...Edit PLC user program 828D only 23 8 Searching for operands Milling 924 Operating Manual 08 2018 6FC5398 7CP41 0BA0 ...
Страница 925: ...Appendix A A 1 840D sl 828D documentation overview Milling Operating Manual 08 2018 6FC5398 7CP41 0BA0 925 ...