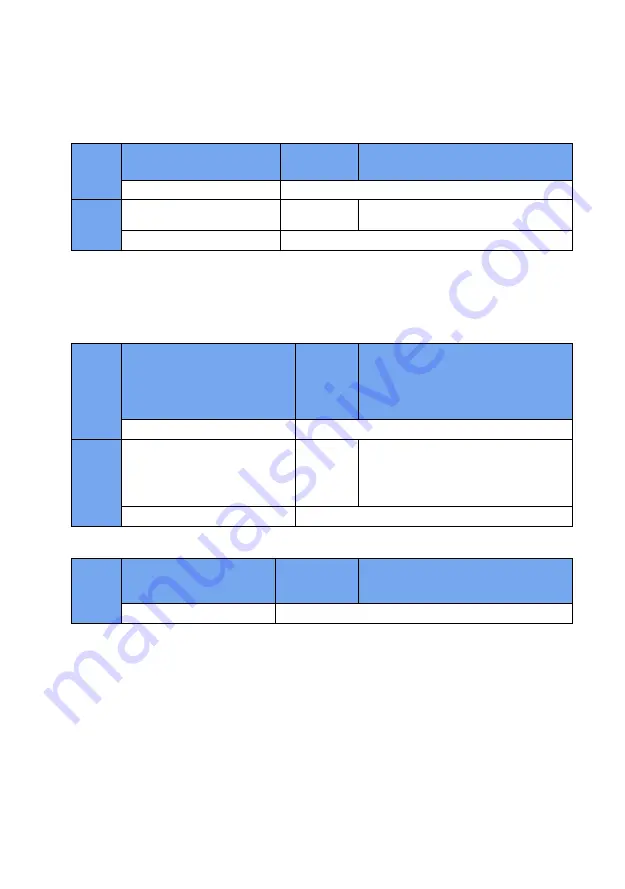
- 114 -
vector control with speed sensor.
When detected motor speed exceeds reference frequency and the excess is larger than the
value of P9-67 for longer than time set in P9-68, the inverter warns FU43 and acts
according to the faulty protection set.
If overspeed detection time is 0.0S, it will cancel over speed detection.
P9-69
Detection level of speed
error
Factory
default
20.0%
Setting Range
0.0%
~
50.0%(max. frequency)
P9-70
Detection time of speed error
Factory
default
5.0s
Setting Range
0.0s
~
60.0s
This function is effective only for vector control with speed sensor.
When detected motor speed is different from frequency reference and the difference is
larger than the value of P9-69 for longer than the time set in P9-70, the inverter warns
FU43 and acts according to the faulty protection set.
If detection time of speed error is 0.0S,it will cancel detection of speed error.
P9-71
Gain Kp during no stop
function with instantaneous
power dip
Factory
default
40
Setting Range
0~100
P9-72
Integral coefficient Ki during no
stop
function
with
instantaneous power dip
Factory
default
30
Setting Range
0~100
This function is effective only for P9-59=1.During no stop function with instantaneous
power dip, if it is under voltage, enlarge Kp and Ki.
P9-73
Deceleration time of power
dip
Factory default
20.0s
Setting Range
0~300.0s
This function is effective only for P9-59=2 .
PA group Process control PID function
PID control is a common method of process control. By comparing the difference between
the controlled feedback signal and the target signal, the output frequency of the inverter is
adjusted to form the closed-loop system, and the controlled quantity is stabilized. Target
value.
It is suitable for process control such as flow control, pressure control and temperature
control. Figure 6-25 shows the control block diagram of process PID.