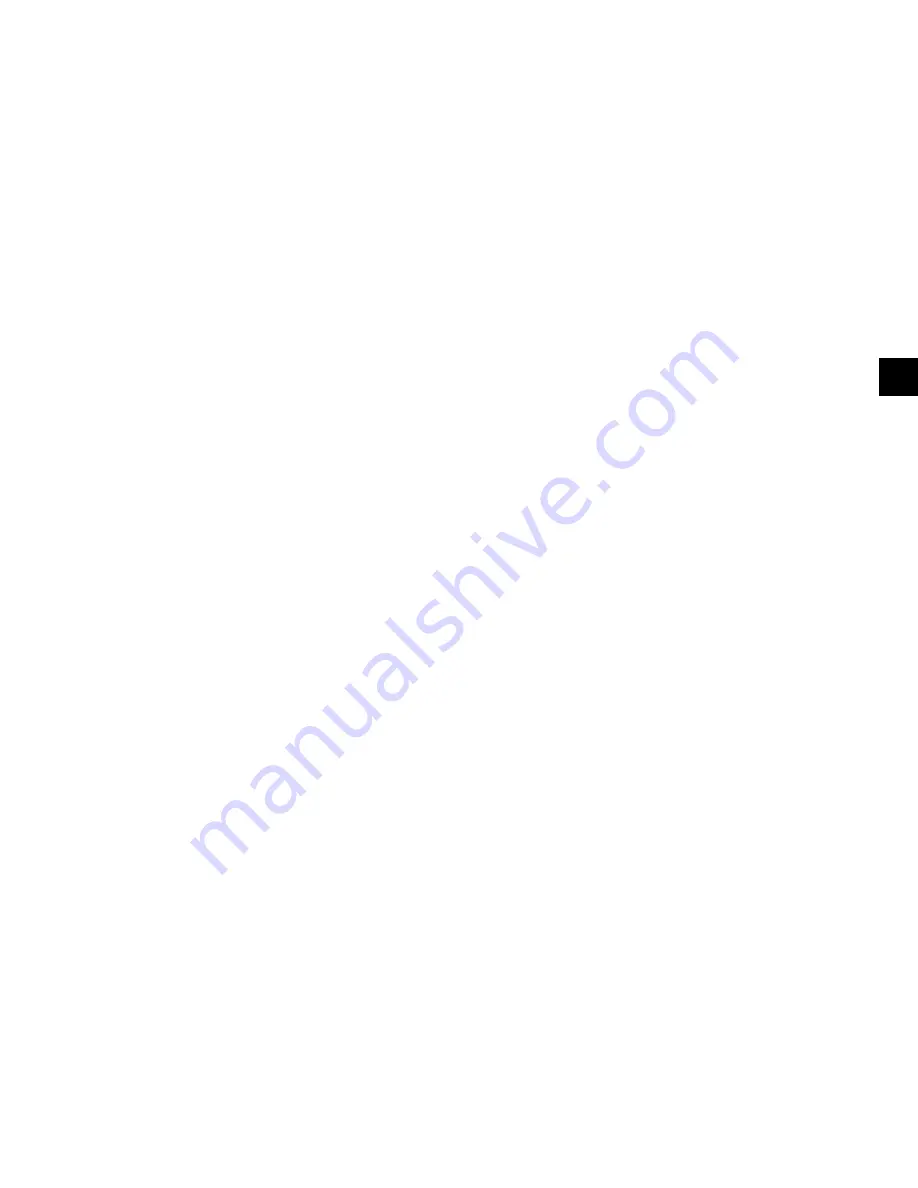
SECTION 4 - GENERAL OPERATING SEQUENCE
JOHNSON CONTROLS
123
FORM 160.72-O1 (810)
HEAD pressure is lowered (due to colder condens-
er water) the compressor is capable of stable opera-
tion at lower loads. The programming in the chiller
panel thus uses the differential HEAD pressure to
establish when the hot gas may be needed.
This valve is opened at shutdown to allow the con-
denser pressure to equalize with the evaporator
quickly, thus reducing backflow of high pressure
gas through the compressor to the evaporator.
The hot gas valve is a pneumatic control valve
with pneumatic positioner. The control signal
from the control panel is 4-20 mA DC, which is
converted to a 3-15 psig / 0.2-1.0 bar pneumatic
signal by an I/P transducer. The valve will be fully
open at 4 mA DC, fully closed at 20 mA DC.
Subcooler Liquid Level Valve
3.
The subcooler liquid level valve controls the re-
frigerant liquid level in the subcooler (located in
the bottom of the condenser) to maintain the prop-
er amount of subcooling and provide the most ef-
ficient operation at all loads.
This valve is opened after shutdown to allow all
the refrigerant liquid to drain through the inter-
cooler and into the evaporator. It remains open for
five minutes after start-up and then slowly closes
until it reaches the position dictated by the liquid
level control PID instruction in the control logic.
The liquid level valve is a pneumatic rotary ball
type control valve with pneumatic positioner. The
control signal from the control panel is 4-20 mA
DC, which is converted to a 3-15 psig / 0.2-1.0 bar
pneumatic signal by an I/P Transducer. The valve
will be fully open at 4 mA DC, fully closed at 20
mA DC.
Interstage Gas Valve
4.
The interstage valve controls refrigerant flash gas,
from the intercooler to the second stage compres-
sor impeller wheel when required to maintain a
minimum pressure in the intercooler.
At normal conditions, the interstage valve will
modulate to control to setpoint and close on shut-
down to reduce compressor backspin.
This valve remains closed for ten minutes (ad-
justable) after start-up to allow the subcooler
level controller to establish a liquid level in the
subcooler and then slowly opens until it reaches
the position dictated by the capacity controls.
When the intercooler float differential pressure
(intercooler pressure minus evaporator pressure)
falls below the minimum allowed (due to colder
than normal condenser water temperatures), the
interstage valve is driven closed by the INTER-
COOLER FLOAT MTN. DIFF. PRESS. CON-
TROL in software. This maintains a minimum
pressure in the intercooler and ensures that the
intercooler refrigerant float valve will have suf-
ficient pressure drop to accommodate the design
flow of liquid being expanded to the evaporator.
The interstage valve is a pneumatic rotary butter-
fly type control valve with pneumatic positioner.
The control signal from the control panel is 4-20
mA DC, which is converted to a 3-15 psig / 0.2-
1.0 bar pneumatic signal by an I/P Transducer.
The valve will be fully closed at 4 mA DC, fully
open at 20 mA DC.
programmed capacity control functions
Manual Override (Manual/Automatic) Stations
1.
The Auto/Manual Screen allows the operator to
manually control the pre-rotation vanes, interstage
valve, hot gas bypass valve, and subcooler level
control valve. Normally these should be left in the
AUTO mode.
If during manual operation the unit is started or
stopped, the manual control override logic returns
the manual control outputs to their safe start-up or
shutdown values so that die PRV and valves are in
their proper positions for the transition, however,
any actuator placed in the manual mode will re-
main there until reset by the operator.
The Auto/Manual display will indicate the control
mode of each actuator and prevent transfer of the
mode from manual to auto when the calculated
auto position and the manual position differ by
more than 5%. This will be indicated by illumi-
nation of the TRANSFER INHIBIT LED for that
actuator and the SWITCH TO AUTO button color
changing from green to red.
Leaving Chilled Water Temperature Control
2.
(Main Capacity Control)
Using the input signal from a temperature trans-
mitter in the leaving chilled water line, this con-
trol provides an output signal which decreases as
water temperature drops below set point to reduce
the capacity of the chiller.
4
Содержание YORK OM Titan
Страница 4: ...FORM 160 72 O1 810 JOHNSON CONTROLS 4 This Page Intentionally Left Blank...
Страница 8: ...FORM 160 72 O1 810 JOHNSON CONTROLS 8 SECTION 1 INTRODUCTION This Page Intentionally Left Blank...
Страница 12: ...FORM 160 72 O1 810 JOHNSON CONTROLS 12 SECTION 3 OPTIVIEW CONTROL CENTER This Page Intentionally Left Blank...
Страница 26: ...FORM 160 72 O1 810 JOHNSON CONTROLS 26 Evaporator Screen This Page Intentionally Left Blank...
Страница 52: ...FORM 160 72 O1 810 JOHNSON CONTROLS 52 Setpoints Screen This Page Intentionally Left Blank...
Страница 78: ...FORM 160 72 O1 810 JOHNSON CONTROLS 78 Options Screen This Page Intentionally Left Blank...
Страница 80: ...FORM 160 72 O1 810 JOHNSON CONTROLS 80 Drive Options Screen This Page Intentionally Left Blank...
Страница 96: ...FORM 160 72 O1 810 JOHNSON CONTROLS 96 History Screen This Page Intentionally Left Blank...
Страница 102: ...FORM 160 72 O1 810 JOHNSON CONTROLS 102 Trend Common Slots Screen This Page Intentionally Left Blank...
Страница 104: ...FORM 160 72 O1 810 JOHNSON CONTROLS 104 Custom Screen This Page Intentionally Left Blank...
Страница 118: ...FORM 160 72 O1 810 JOHNSON CONTROLS 118 SECTION 3 OPTIVIEW CONTROL CENTER This Page Intentionally Left Blank...
Страница 136: ...FORM 160 72 O1 810 JOHNSON CONTROLS 136 SECTION 5 SYSTEM COMMISSIONING This Page Intentionally Left Blank...