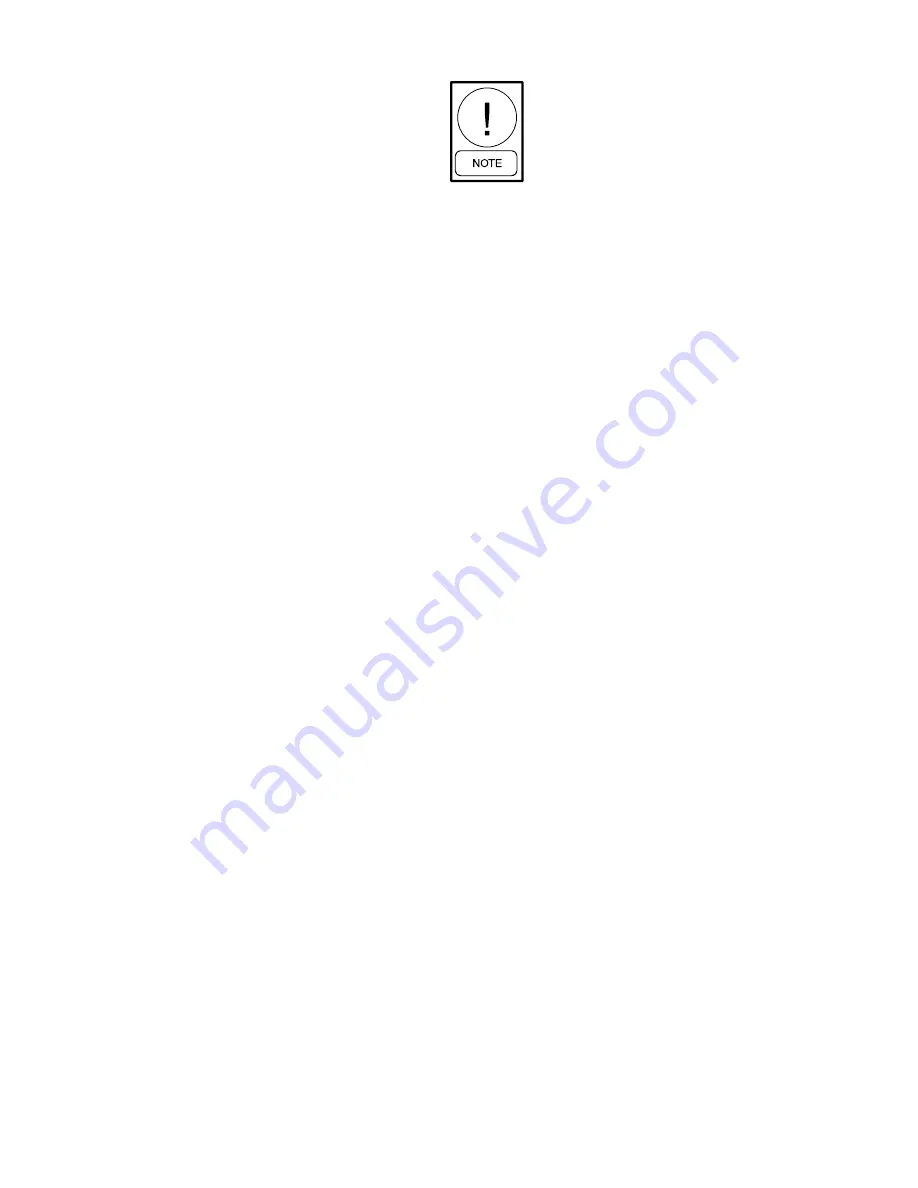
FORM 160.72-O1 (810)
JOHNSON CONTROLS
120
SECTION 4 - GENERAL OPERATING SEQUENCE
If the minimum oil pressures are not established,
startup will be prevented and an alarm signal will
be transmitted to the DISPLAY for indication and
recording. At this point, the operator would manu-
ally turn on the auxiliary oil pumps by pressing
the AUTO MANUAL button on the appropriate
DISPLAY screen. After adequate pressure is es-
tablished, the starting may continue.
If the minimum water flows are not established,
startup will be prevented and an alarm signal will
be transmitted to the DISPLAY for indication and
recording.
At the end of the pre-lube time, with the oil pres-
5.
sures and water flows established, a signal is pro
-
vided to energize the compressor drive motor start
control relay to close its contact and energize the
motor starter control circuit.
If the starter auxiliary (start) contact does not close
6.
within the programmed (1 to 10 seconds) time af-
ter the start relay is energized, an alarm signal will
be transmitted to the DISPLAY for indication and
recording and the start relay will be de-energized.
At 2 seconds (adjustable timer, if enabled) after
7.
the starter auxiliary (start) contact closes, the Vi-
bration Monitor Trip Bypass contact is opened to
allow vibration trips to occur.
When the starter has completed and the transition
8.
to full voltage operation, an auxiliary contact from
the starter run (full voltage) contactor is input to
the chiller control panel to operate the following:
Enable the capacity control circuit compres-
A.
sor pre-rotation vanes and hot gas bypass
valve will now begin to ramp open / closed
at a predetermined rate. See CAPACITY
CONTROL OPERATION for further details
on the ramp-up of the controls.
De-energize the compressor oil heaters, and
B.
energize the auxiliary cooling water solenoid
valve.
When the shaft pumps maintain the gearbox
C.
and compressor oil pressures for a 100 sec-
ond time period (through the respective aux-
iliary oil pump control logic), the auxiliary
motor driven oil pumps will be stopped.
Whenever the gearbox or compressor
shaft pump oil pressure falls below the
auxiliary oil pump control logic set-
ting, the auxiliary pump motors will be
restarted and an alarm signal will be
transmitted to the DISPLAY for indication
and recording.
If either pump does not produce sufficient
oil pressure to satisfy the auxiliary oil
pump control logic within five minutes
after start, an alarm signal will be trans-
mitted.
The compressor sump vent solenoid valve is ener-
9.
gized 20 seconds (adjustable) after the compres-
sor shaft oil pump maintains sufficient pressure. It
then remains energized until the next shutdown.
This allows the sump vent ball valve to slowly
open at a rate determined by the setting of the nee-
dle valve located in the air supply line upstream of
the solenoid valve.
The needle valve must be adjusted so that the
valve opens slowly enough to prevent foaming in
the compressor sump caused by too rapid a sump
pressure reduction on startup.
100 Seconds after the motor starter auxiliary (run)
10.
contact closes, the oil separator heaters are ener-
gized. When the oil temperature in the separa-
tor reaches approximately 100°F, the temperature
control switch closes to actuate the solenoid valve
in the high pressure gas supply line to the eductor.
The eductor will then pull a fresh oil and refrigerant
mixture from the bottom of the evaporator, into the
separator. The refrigerant is boiled off and returned
to the evaporator. The oil level increases and flows
out of the separator, to return to the compressor.
5 Minutes after the motor starter auxiliary (run)
11.
contact closes, the subcooler level control valve,
if enables, begins to ramp closed to allow liquid
refrigerant to accumulate in the subcooler.
10 minutes (adjustable) after the motor starter aux-
12.
iliary (run) contact closes, the interstage valve, if
enabled, begins to ramp open to reduce the pres-
sure in the intercooler and the interstage liquid in-
jection solenoid valve is energized.
After the ramp-up is completed, the capacity con-
13.
trols operate to control chiller capacity in response
to chilled water outlet temperature.
Содержание YORK OM Titan
Страница 4: ...FORM 160 72 O1 810 JOHNSON CONTROLS 4 This Page Intentionally Left Blank...
Страница 8: ...FORM 160 72 O1 810 JOHNSON CONTROLS 8 SECTION 1 INTRODUCTION This Page Intentionally Left Blank...
Страница 12: ...FORM 160 72 O1 810 JOHNSON CONTROLS 12 SECTION 3 OPTIVIEW CONTROL CENTER This Page Intentionally Left Blank...
Страница 26: ...FORM 160 72 O1 810 JOHNSON CONTROLS 26 Evaporator Screen This Page Intentionally Left Blank...
Страница 52: ...FORM 160 72 O1 810 JOHNSON CONTROLS 52 Setpoints Screen This Page Intentionally Left Blank...
Страница 78: ...FORM 160 72 O1 810 JOHNSON CONTROLS 78 Options Screen This Page Intentionally Left Blank...
Страница 80: ...FORM 160 72 O1 810 JOHNSON CONTROLS 80 Drive Options Screen This Page Intentionally Left Blank...
Страница 96: ...FORM 160 72 O1 810 JOHNSON CONTROLS 96 History Screen This Page Intentionally Left Blank...
Страница 102: ...FORM 160 72 O1 810 JOHNSON CONTROLS 102 Trend Common Slots Screen This Page Intentionally Left Blank...
Страница 104: ...FORM 160 72 O1 810 JOHNSON CONTROLS 104 Custom Screen This Page Intentionally Left Blank...
Страница 118: ...FORM 160 72 O1 810 JOHNSON CONTROLS 118 SECTION 3 OPTIVIEW CONTROL CENTER This Page Intentionally Left Blank...
Страница 136: ...FORM 160 72 O1 810 JOHNSON CONTROLS 136 SECTION 5 SYSTEM COMMISSIONING This Page Intentionally Left Blank...