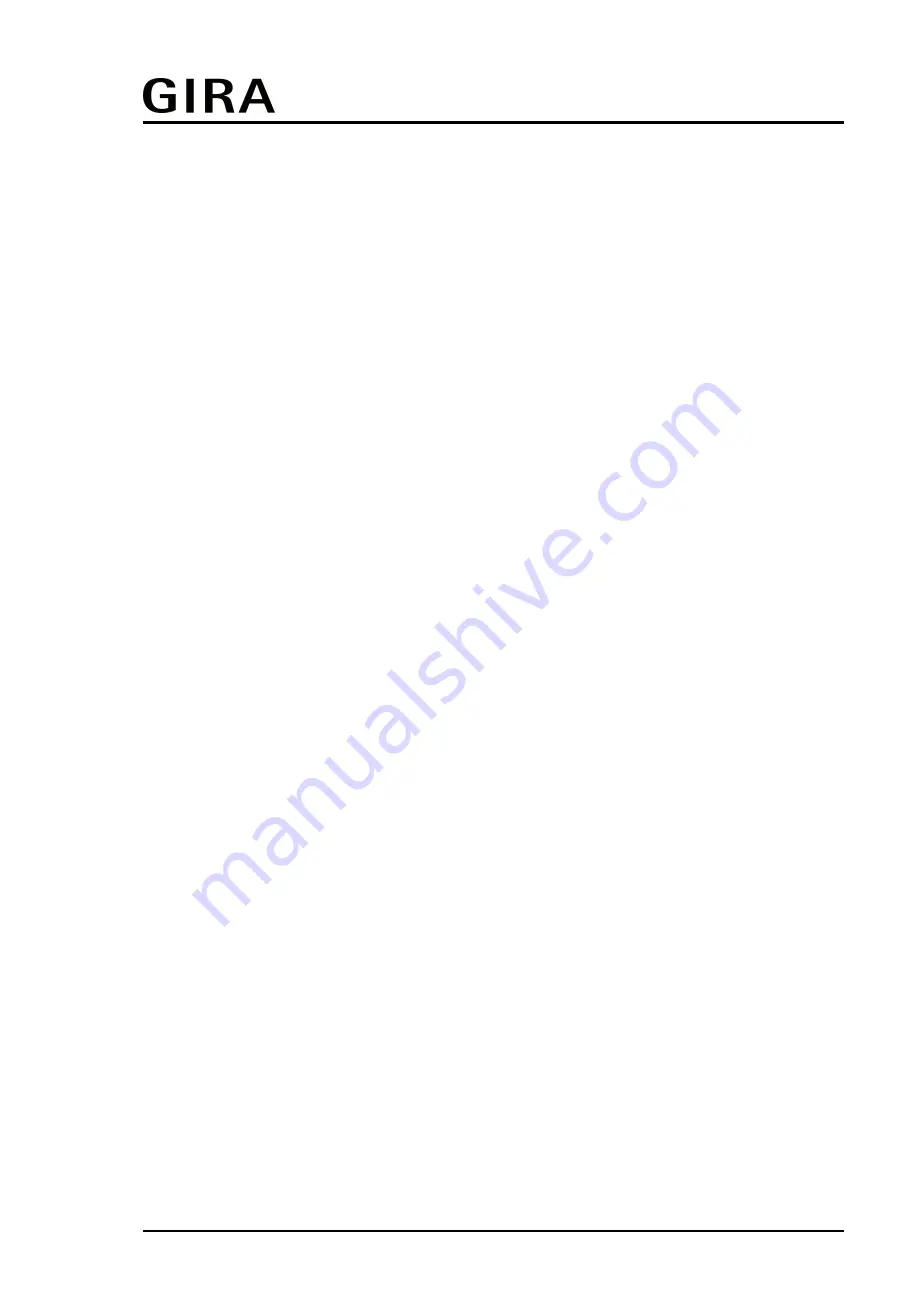
Order No. 2104 ..
4.2.4.4.7 Command value and status output
Command value objects
The format of the command value objects are determined depending on the control algorithm
selected for heating and / or cooling and, if applicable, also for the additional levels. 1 bit or 1
byte command value objects can be created in the ETS. The control algorithm calculates the
command values in intervals of 30 seconds and outputs them via the objects. With the pulse
width modulated PI control (PWM) the command value is updated, if required, solely at the end
of a time cycle.
Possible object data formats for the command values separately for both heating/cooling
operating modes, for the basic and the additional level or for both control circuits are…
-
continuous PI control: 1 byte
-
Switching PI control: 1 bit + additionally 1 byte (for example for the status indication with
visualisations),
-
switching 2-point feedback control: 1 bit.
Depending on the set heating/cooling operating mode, the controller is able to address heating
and / or cooling systems, to determine command values and to output them via separate
objects. One distinguishes between two cases for the "Heating and cooling" mixed operating
mode...
-
Case 1: Heating and cooling system are two separate systems
In this case the "Transmit heating and cooling command value to one common object"
parameter should be set to "No" in the "Room temperature control -> Controller functions"
parameter node. Thus, there are separate objects available for each command value,
which can be separately addressed via the individual systems.
This setting allows to define separate types of control for heating and cooling.
-
Case 2: Heating and cooling system are a combined system
In this case the "Transmit heating and cooling command value to one common object"
parameter may be set, if required, to "Yes". This will transmit the command values for
heating and cooling to the same object. In case of a two-level feedback control, another
shared object will be enabled for the additional levels for heating and cooling.
With this setting it is only possible to define the same type of feedback control for heating
and for cooling as the feedback control and the data format must be identical. The ("Type
of heating / cooling") control parameter for cooling and heating still has to be defined
separately.
A combined command value object may be required, for example, if heating as well as
cooling shall take place via a single-pipe system (combined heating and cooling system).
For this, the temperature of the medium in the single-pipe system must be changed via the
system control. Afterwards the heating/cooling operating mode is set via the object (often
the single-pipe system uses cold water for cooling during the summer, hot water for heating
during the winter).
If required, the command value can be inverted before the transmission to the KNX. With output
via a combined object, the parameters "Output of heating command value", "Output of cooling
command value" or "Output of command values..." output the command value in inverted
fashion according to the object data format. The parameters for inverting the additional level(s)
are additionally available in the two-level control.
The following applies…
For continuous command values:
-> not inverted: Command value 0 % ... 100 %, value 0 ... 255
-> inverted: Command value 0 % ... 100 %, value 255 ... 0
For switching command values:
-> not inverted: Command value off / on, value 0 / 1
-> inverted: Command value off / on, value 1 / 0
Page 102 of 171
Software "KNX CO2 sensor"
Functional description
Содержание CO2-Sensor
Страница 42: ...Order No 2104 Figure 7 CO2 concentration Page 42 of 171 Software KNX CO2 sensor Functional description...
Страница 74: ...Order No 2104 Page 74 of 171 Software KNX CO2 sensor Functional description...
Страница 165: ...Order No 2104 See channel 1 Disable Page 165 of 171 Software KNX CO2 sensor Parameters...