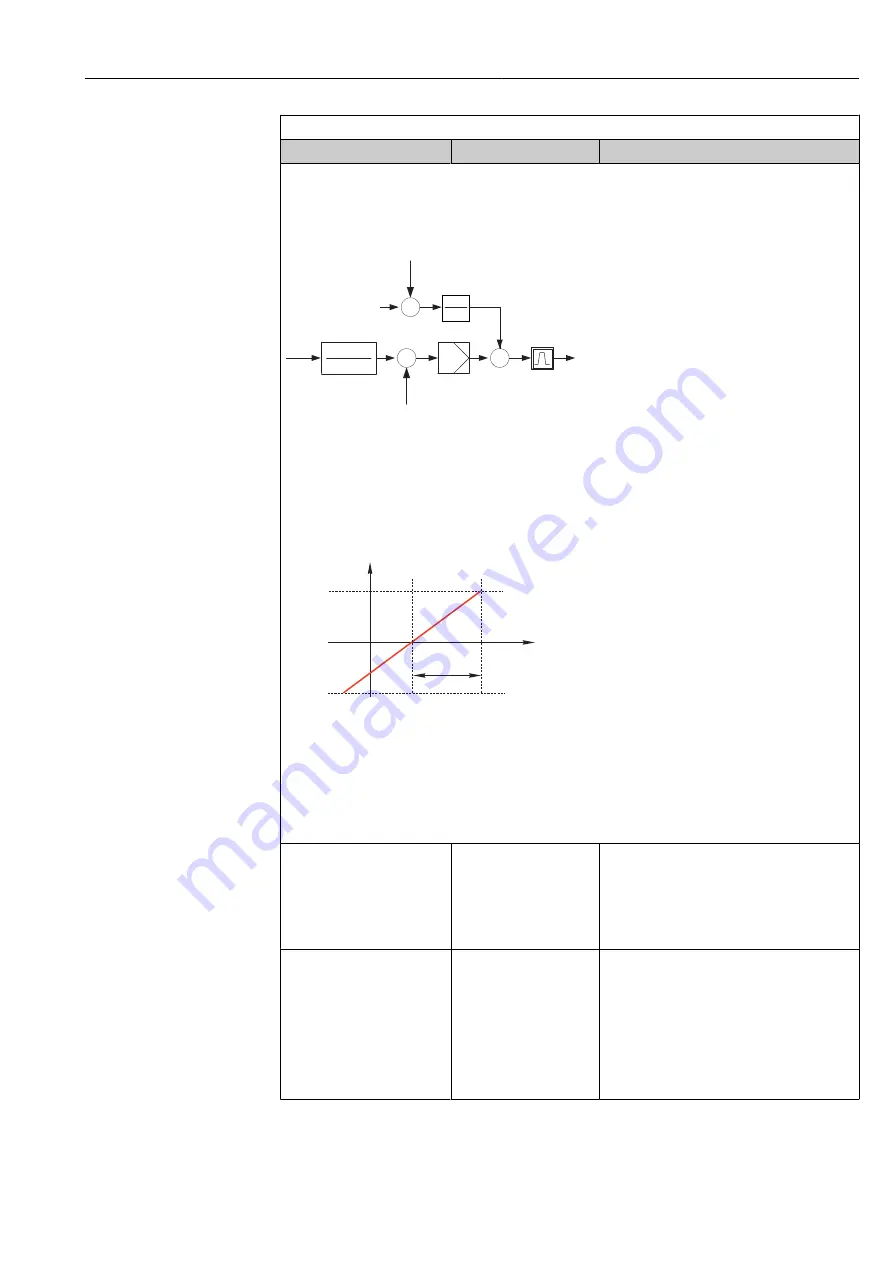
Liquiline System CA80SI
Operation
Hauser
103
Menu/Setup/Additional functions/Controller 1 ... 2
Function
Options
Info
In the case of "flowing medium" (in-line) controls, the flow rate may not be constant. In some circumstances,
strong fluctuations are possible. In the case of a settled control system in which the flow rate is suddenly
halved, it is desirable that the dosed quantity from the controller is also directly halved. In order to achieve this
type of "flow-rate
‐
proportional" dosing, this task is not left to the I
‐
component of the controller, but rather one
enters the (to be measured) flow rate as disturbance variable z multiplicative at the controller output.
z
z
z
0
1
p
y
x
x
1
w
+
+
-
e
r
1+T
w
s
-
Strictly speaking, feedforward control involves an open-loop control system, since its effect is not measured
directly. That means that the feed flow is directed exclusively forward. Hence the designation "feedforward
control".
For the additive feedforward control that is alternatively available in the device, the (standardized) disturbance
variable is added to the controller manipulated variable. This enables you to set up a type of variable base load
dosing.
The standardization of the disturbance variable is required both for multiplicative and for additive feedforward
control and is done using parameters Z
0
(zero point) and Z
p
(proportional band): z
n
= (z
‐
z
0
)/z
p
z
0
z
n
z
z
P
+100 %
0 %
-100 %
Example
Flowmeter with measuring range 0 to 200 m
3
/ h
The controller would currently dose 100% without feedforward control.
The feedforward control should be configured such that at z = 200m
3
/h, the controller still doses at 100% (z
n
=
1).
If the flow rate drops, the dosing rate should be reduced, and at a flow rate of less than 4 m
3
/h, dosing should
stop entirely (z
n
= 0).
→ Select the zero point z
0
= 4 m
3
/h and the proportional band Z
p
= 196 m
3
/h.
Function
Selection
• Off
• Multiply
• Add
Factory setting
Off
Selecting multiplicative or additive feedforward
control
Source of data
Selection
• None
• Sensor inputs
• Current inputs
• Fieldbus signals
• Binary inputs
• Mathematical functions
Factory setting
None
‣
Specify the input which should be the source
of data for the disturbance variable.
Содержание Liquiline CA80SI
Страница 2: ......
Страница 172: ...www addresses endress com 71593680 71593680 ...