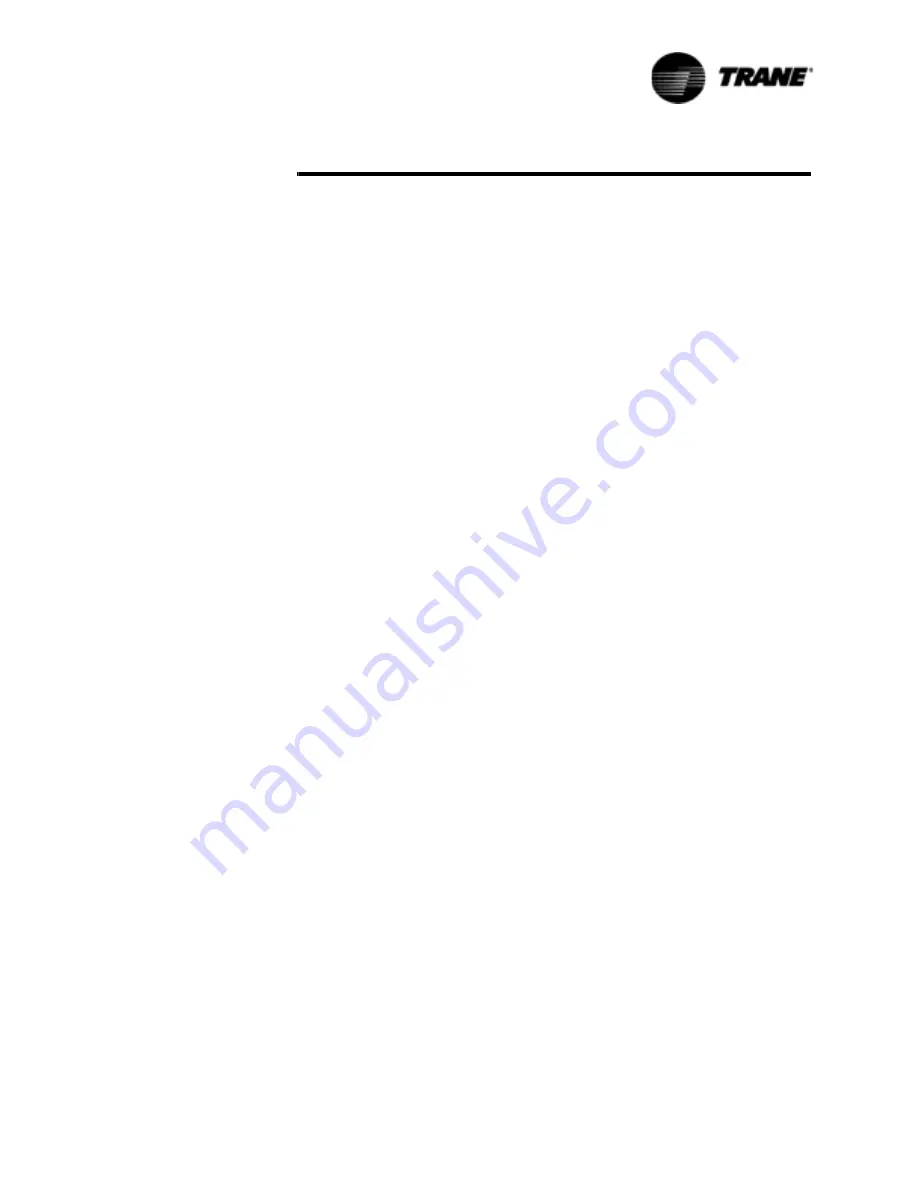
RLC-SVX07A-EN
87
Operating Principles
Compressor Rotors
The compressor is a semi-hermetic, direct-drive helical rotary type
compressor. Each compressor has two rotors - “male” and “female” - which
provide compression. See
Figure
37
. The male rotor is attached to, and driven
by, the motor, and the female rotor is, in turn, driven by the male rotor.
Separately housed bearing sets are provided at each end of both rotors.
The helical rotary compressor is a positive displacement device. The refrig-
erant from the evaporator is drawn into the suction opening at the end of the
motor barrel, through a suction strainer screen, across the motor, and into the
intake of the compressor rotor section. The gas is then compressed and
discharged directly into the discharge line.
There is no physical contact between the rotors and compressor housing.
The rotors contact each other at the point where the driving action between
the male and female rotors occurs. Oil is injected along the top of the
compressor rotor section, coating both rotors and the compressor housing
interior. Although this oil does provide rotor lubrication, its primary purpose is
to seal the clearance spaces between the rotors and compressor housing.
A positive seal between these internal parts enhances compressor efficiency
by limiting leakage between the high pressure and low pressure cavities.
Capacity control is accomplished by means of two unloader valve assemblies
in the rotor section of the compressor. The female rotor valve is a two-
position valve and the male valve is an infinitely variable position valve. See
Figure
37
.
Compressor load capacity is dictated by the positions of the unloader valves.
They divert refrigerant gas from the rotors to the compressor suction, thus
unloading the compressor. This varies the compressor capacity to match the
load and reduces the KW draw of the compressor motor.
The two-position female unloader will fully open or fully close a port on the
rotor housing, at the discharge end of the female rotor. This relieves a refrig-
erant gas to suction and unloads the compressor. The female unloader valve
is the first stage of loading after the compressor starts and the last stage of
unloading before the compressor shuts down.
The modulating male unloader valve opens or closes ports in the rotor
housing along the side of the male rotor. It can move to a more loaded
(closed) position after the female unloader valve is in the loaded position or
can relieve refrigerant gas to suction to unload the compressor.
Compressor Loading Sequence (RTWA and RTUA only)
When there is a call for chilled water, the UCM will start the compressor
which has the least number of starts. If the first compressor cannot satisfy
the demand, the UCM will start the other compressor and then balance the
load on both compressors by pulsing the load/unload solenoids.
The load on the compressors will be kept in balance, as load fluctuates, until
the demand for chilled water is reduced to a level that can be handled by one
compressor. At this time, the UCM will drop off the compressor that has the
greatest number of operating hours and will adjust the load on the other
compressor, as required.
Oil System Operation (RTWA and RTUA Only)
Overview
Oil that collects in the bottom of the oil separator is at condensing pressure
during compressor operation; therefore, oil is constantly moving to lower
pressure areas. Refer to
Figure
37
.
Summary of Contents for R Series
Page 17: ...RLC SVX07A EN 17 Installation Mechanical Figure 2 Rigging and Lifting for RTWA Units ...
Page 22: ...22 RLC SVX07A EN Installation Mechanical Figure 7 Rigging and Lifting for RTUA Units ...
Page 25: ...RLC SVX07A EN 25 Installation Mechanical Figure 10 Rigging and Lifting for RTCA Condenser ...
Page 69: ...RLC SVX07A EN 69 Installation Electrical Figure 28 Interconnecting Wiring from RTUA to RTCA ...
Page 129: ...RLC SVX07A EN 129 Start Up Procedures Figure 41 RTWA Unit Sequence of Operation ...
Page 130: ...130 RLC SVX07A EN Start Up Procedures Figure 42 RTUA Unit Sequence of Operation ...
Page 154: ...154 RLC SVX07A EN Diagnostics ...
Page 156: ...156 RLC SVX07A EN 3332 ...
Page 158: ...158 RLC SVX07A EN 3333 ...
Page 160: ...160 RLC SVX07A EN 3334 ...
Page 162: ...162 RLC SVX07A EN 3335 ...
Page 164: ...164 RLC SVX07A EN 3336 ...
Page 166: ...166 RLC SVX07A EN 5119 ...
Page 168: ...168 RLC SVX07A EN 5143 ...
Page 170: ...170 RLC SVX07A EN 5144 ...
Page 172: ...172 RLC SVX07A EN 5145 ...
Page 174: ...174 RLC SVX07A EN 5146 ...
Page 176: ...176 RLC SVX07A EN 6008 ...
Page 178: ...178 RLC SVX07A EN 6009 ...
Page 180: ...180 RLC SVX07A EN 5147 ...
Page 182: ...182 RLC SVX07A EN 6526 ...
Page 184: ...184 RLC SVX07A EN 5150 ...
Page 186: ...186 RLC SVX07A EN 6010 ...