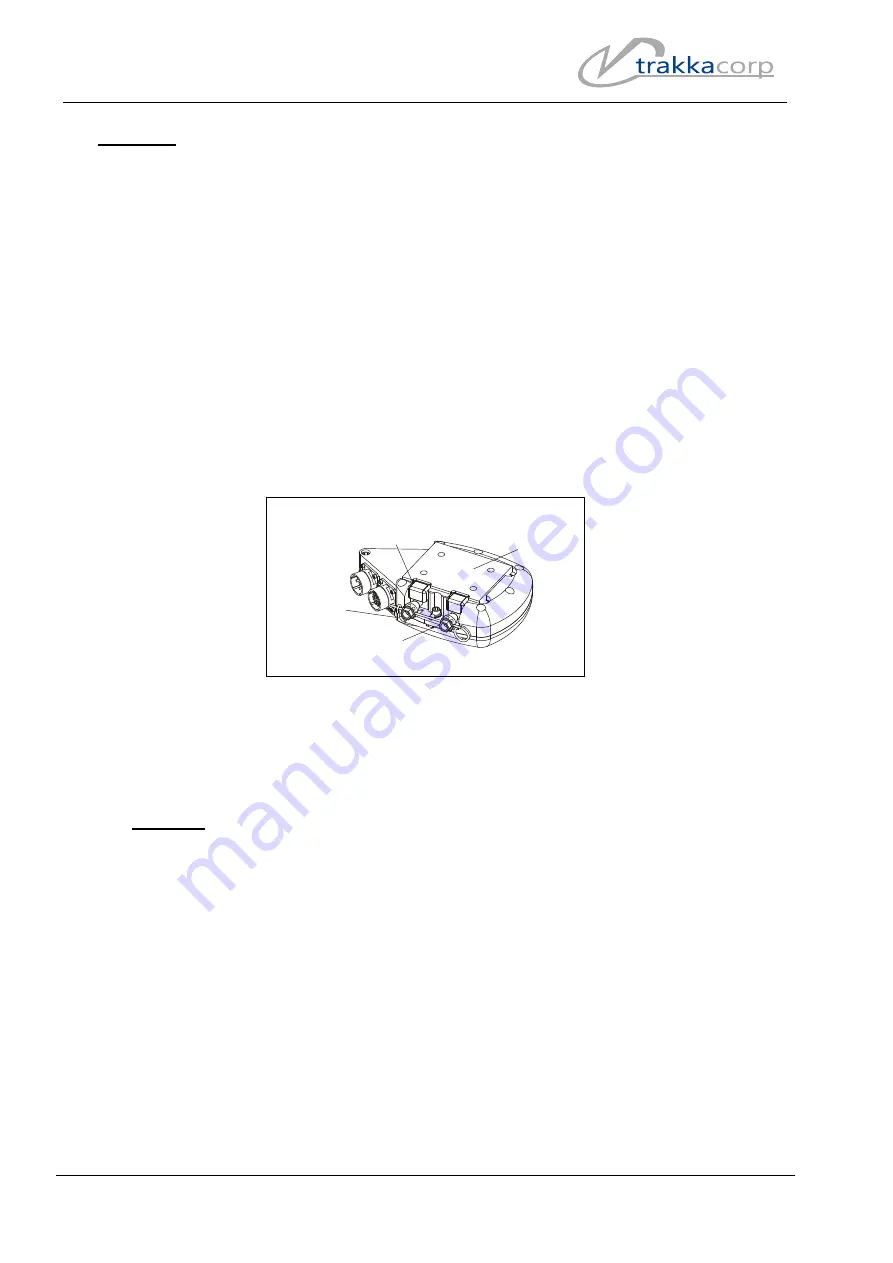
COMPONENT MAINTENANCE MANUAL
Publication No. 051019-1 Rev H
Page 66
33-46-00
AS9100 Certified
Rev G
26-Mar-2014
WARNING: ENSURE ALL PERSONNEL ARE CLEAR OF THE FRONT OF THE SEARCHLIGHT
AND THAT THEY ARE WEARING SAFETY GLASSES THAT COMPLY WITH
AUSTRALIAN STANDARDS AS/NZS 1337 AND 1338 OR SIMILAR OVERSEAS
STANDARDS FOR OCULAR AND IMPACT PROTECTION.
(6) There will be a requirement to energise the light beam to check its focus so a clear area will be
required for aiming at a vertical, and flat, surface. The surface should be:
•
Flat and dark colour to reduce glare.
•
2.4 m x 2.4 m square.
•
10 metres distant.
•
No special markings are required for this check.
(7) A part of checking the focus will involve movement of the searchlight.
B. Removal of the Searchlight Assembly
(1) Disconnect power to the searchlight.
(2) Disconnect the electrical cables from the side of the dovetail assembly (Figure 46).
(3) Disconnect the aircraft bonding strap.
Figure 46 - Dovetail Assembly
(4) Remove the retaining safety pin (Figure 46) (037310) from the two dovetail retaining bolts
(037309) on the top of the dovetail assembly (Figure 46).
(5) Wind out the dovetail retaining block bolts (037309) until the dovetail retaining block assemblies
(034037) are clear of the recesses in the dovetail mounting block (037305).
CAUTION:
THE GIMBAL AND LAMP ASSEMBLY IS HEAVY. EXERCISE CARE WHEN
REMOVING THE ASSEMBLY FROM THE DOVETAIL MOUNTING BLOCK.
REFER TO Figure 23 FOR THE SAFE LIFTING AREAS.
(6) Remove the searchlight by sliding it in a forward direction until it is clear of the dovetail mounting
block.
Dovetail Retaining
Block Assemblies
Dovetail
Mounting
Block
Dovetail Retaining
Block Bolts
Retaining
Safety Pin
G005a
AIRBUS HELICOPTERS: CMM L334M6304E01 ISSUE: B PAGE 84 OF 165
The document reference is online, please check the correspondence between the online documentation and the printed version.