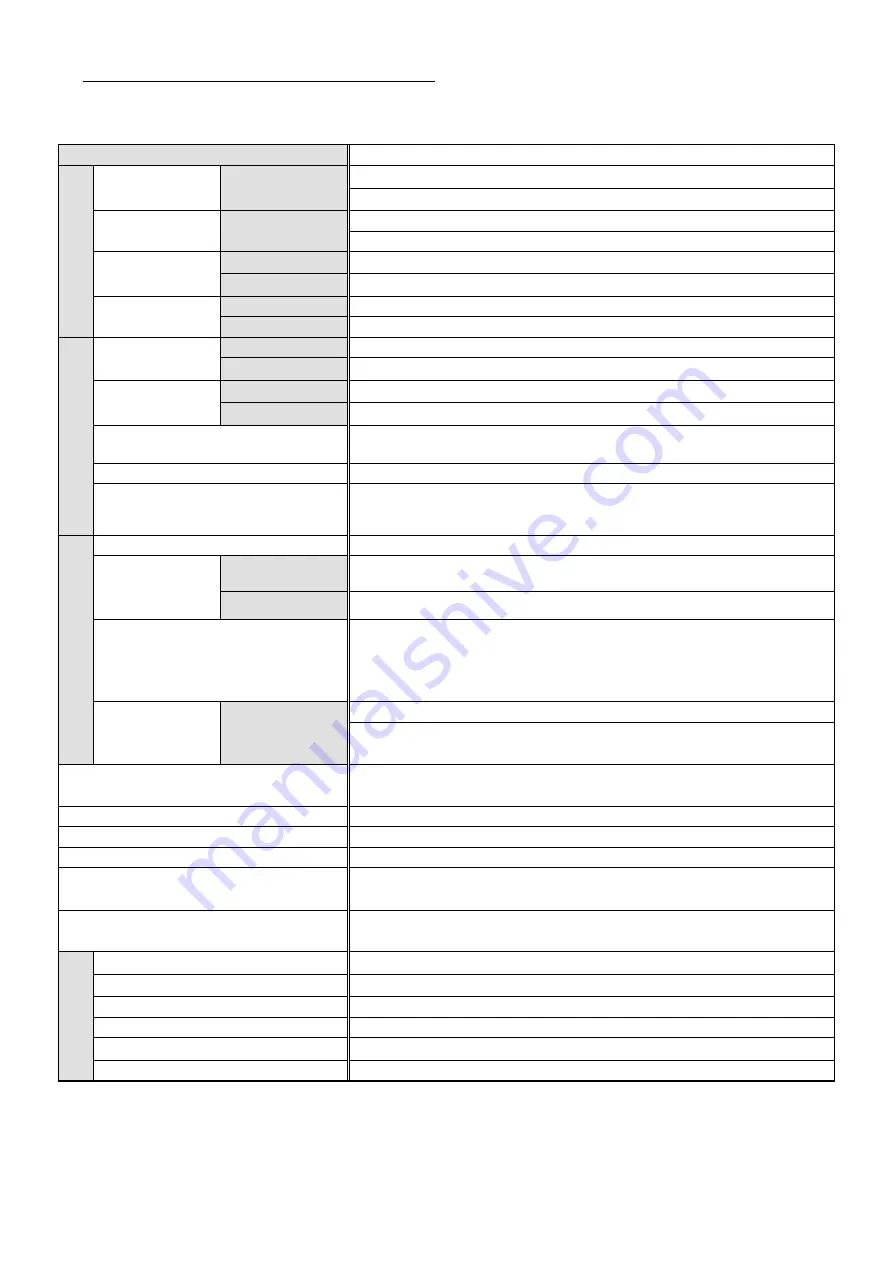
- 312 -
11-2 Inverter General Specification
11-2 Inverter General Specification
Control mode
Vector control ∕ sensorless vector control ∕ V/f control
Dr
iv
in
g
p
er
fo
rm
a
n
ce
*
1
Speed
control range
With PG sensor
0.05Hz-240Hz(1
:
1000/50Hz reference) *5
Without PG sensor
0.25Hz-240Hz(1
:
200/50Hz reference) *5
Speed
Response/precision
With PG sensor
Response characteristic: 250rad/sec Precision: ±0.01%
Without PG sensor
Response characteristic: 100rad/sec Precision: ±0.5%
Torque
control range
With PG sensor
1
:
50(rated torque ratio)
Without PG sensor
1
:
20(rated torque ratio)
Torque precision
With PG sensor
±10%(of rated torque)
Without PG sensor
±20%(of rated torque)
Co
n
tr
o
l
spec
ifi
ca
tio
n
Frequency
setting resolution
Digital setting
0.01Hz
Analog setting
0.05%(12bit0-10V
,
4-20mA), 0.1%(11bit0-5V)
of the maximum output frequency
Frequency precision
Digital setting
±0.01% of output frequency(at -10-40
℃
)
Analog setting
±0.2% of the maximum output frequency(at 25
℃
±10
℃
)
*
2
PG input
Open collector, push-pull mode (power supply voltage 24V) Max. number of pulses:
491.52kHz
*
3
DC braking
Starting frequency (0.05-20Hz), operation time (0.1-10s), braking force (1-10 grades)
Additional functions
Restart after momentary power failure, flying start, multi-speed operation,
frequency jump, auto alarm recovery, PID control operation,
simple scheduled operation, energy-saving operation and others
O
p
er
a
tio
n
spec
ifi
ca
ti
o
n
Start/stop setting
Operation panel, serial communication (RS485, Modbus), control circuit terminals
Frequency
command setting
Digital setting
Operation panel, serial communication (RS485, Modbus),
step setting from terminal board
Analog setting
3 channels, 0-5V, 0-10V, 4-20mA, potentiometer (5kΩ, 0.3W and above)
Input signal
Frequency command, forward run command, reverse run command,
acceleration/deceleration time setting, free run stop, alarm reset, emergency stop,
jogging selection, step frequency setting, operation signal hold and others
[Digital input: 8 channels (arbitrary allocation)],
[Analog input: 3 channels for current
and voltage]
Output signal
Contact output
Alarm batch and multifunctional contact output (1C contact, 250VAC, 0.3A)
Monitor signal
Operating, frequency matching, overload alarm, undervoltge,
frequency approach and
etc.
[Open-collector output: 3 channels (arbitrary allocation), Analog output: 2 channels]
LED display
Frequency, output current, speed, load factor, no unit: (output voltage, power and etc.),
operating, alarm
LCD display
Various status, code, alarm, message display (English, Japanese, Chinese)
Communication I/F
RS485, Modbus-RTU
External power supply output
DC24V, 150mA(control terminal board)
Protection function
Current limiting, overcurrent shutoff, motor overload, external thermal alarm,
undervoltage, overvoltage, momentary power failure, fin overheat, open phase
Warning function
Overvoltage prevention, current limiting during acceleration/deceleration,
brake resistor overheat, overload, overheating of radiator fins
En
v
ir
o
n
m
en
t
Ambient temperature
-10
℃
-+50
℃
(no frost):heavy overload,
-10
℃
-+40
℃
(no frost):light overload
Storage temperature
-20
℃
-+65
℃
(short-term storage during transportation)
*
4
Relative humidity
95%RH or less(no condensation)
Elevation
2000m or lower(Decrease the current when higher than 1000m)
Vibration
5.9m/s
2
(0.6G
)
or less(JIS C 60068-2-6 standard; IEC60068-2-6)
Gas medium
Indoor (no corrosive or inflammable gases, oil mist, or dust)
*1
Vary with the environment, condition, motor in use or sensor.
*2
The maximum output frequency is at 5V, 10V, and 20mA.
*3
An optional board is required for linear driver input.
*4
Applicable temperature for medium-term and long-term transportation.
*5
When 2-pole motor is set, the maximum value of frequency setting range is 120Hz.
Summary of Contents for SVCO6
Page 1: ...High Performance Vector Control Inverter Instruction Manual SANKEN ELECTRIC CO LTD ...
Page 2: ......
Page 324: ... 322 Memorandum ...
Page 325: ......