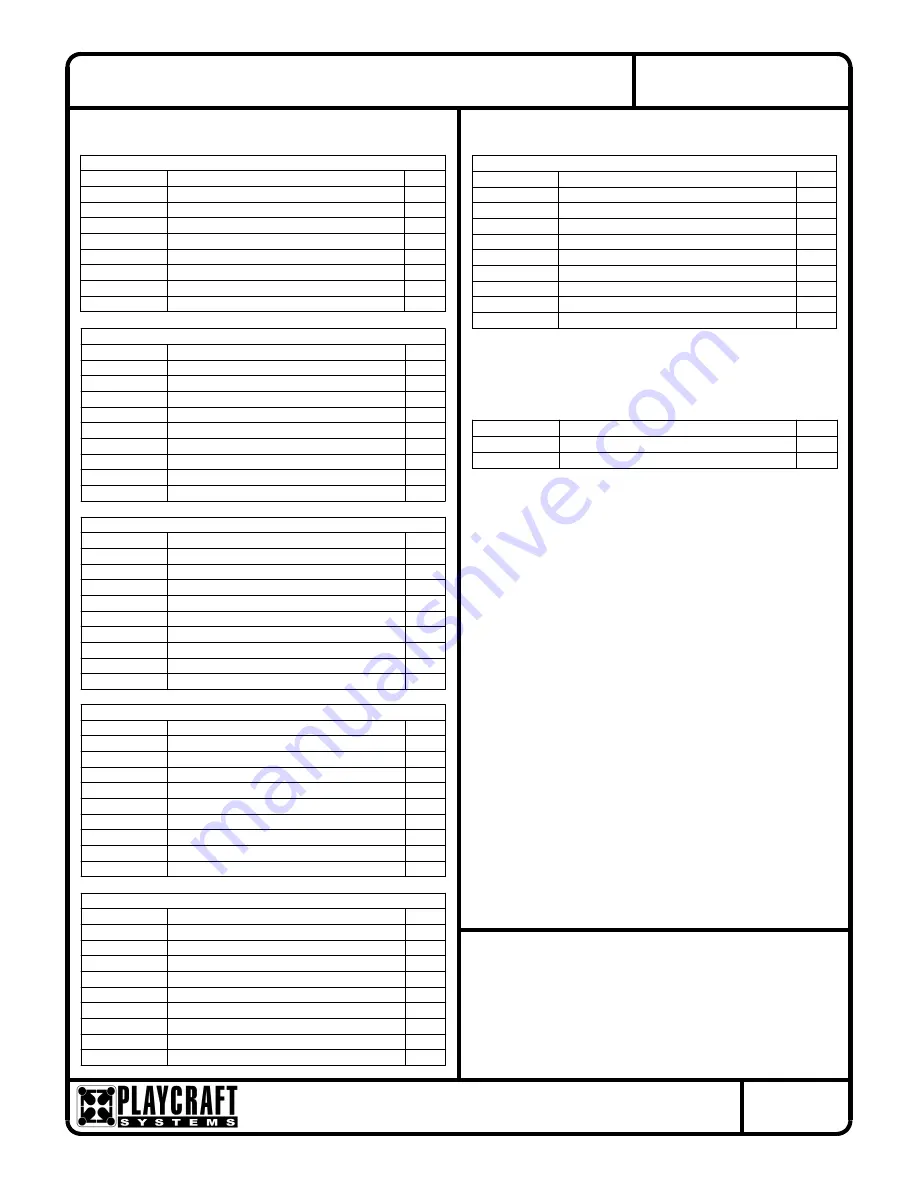
Manufactured by Krauss Craft, Inc.
www.playcraftsystems.com
For Customer Service Call
800.333.8519 (U.S.A.) or
541.955.9199 (International)
DISC CLIMBER
INSTALLATION INSTRUCTIONS
Rev B
11/13/2014
1233
Page 5 of 5
Part #
DESCRIPTION
QTY
9123231
Bolt Hex 3/8" x 5-1/2"
1
9483602
Nut Hex 3/8"
1
DISC CLIMBER CAP:
Shall be made from high density 3/4" sheet plastic
specially formulated for optimum UV protection and
color retention.
DISC CLIMBER DISC:
Shall be constructed of UV-stabilized, rotationally
molded, linear, low density polyethylene with an
average wall thickness of .250".
DISC CLIMBER POST:
Shall be fabricated using 3.5" O.D. 8 gauge steel
tubing with welded 1.315" O.D. 12 gauge steel
handles. The Disc Climber Post shall have a multi-
stage baked-on powder coat finish.
POST CAP R3.5 DOME:
Shall be precision die cast from a high-strength
aluminum alloy. The Post Cap R3.5 Dome shall
have a multi-stage baked-on powder coat finish.
HARDWARE:
Shall be stainless steel, zinc/nickel plated or
galvanized as required to resist rust and corrosion.
1 DISC ASSEMBLY
Part #
DESCRIPTION
QTY
DE-4373
Disc Climber Disc
1
EG-4442
Disc Climber Cap
1
FS-1233-1
Disc Climber Post 12"
1
GG-8135
Post Cap R3.5 Dome
1
9103032-TR
Bolt Button Head 3/8" x 3/4"
3
9271062-TR
Screw Tek 1/4" x 1-1/4" BH TR
3
9333042
Washer Flat 3/8" x 7/8" O.D.
3
9610012
Rivet 3/16" x 1/2" to 3/4" Pop
2
2 DISC ASSEMBLY
Part #
DESCRIPTION
QTY
DE-4373
Disc Climber Disc
2
EG-4442
Disc Climber Cap
1
FS-1233-2
Disc Climber Post 24"
1
GG-8135
Post Cap R3.5 Dome
1
9103032-TR
Bolt Button Head 3/8" x 3/4"
3
9103062-TR
Bolt Button Head 3/8" x 1-1/4"
3
9271062-TR
Screw Tek 1/4" x 1-1/4" BH TR
6
9333042
Washer Flat 3/8" x 7/8" O.D.
6
9610012
Rivet 3/16" x 1/2" to 3/4" Pop
2
3 DISC ASSEMBLY
Part #
DESCRIPTION
QTY
DE-4373
Disc Climber Disc
3
EG-4442
Disc Climber Cap
1
FS-1233-3
Disc Climber Post 36"
1
GG-8135
Post Cap R3.5 Dome
1
9103032-TR
Bolt Button Head 3/8" x 3/4"
3
9103062-TR
Bolt Button Head 3/8" x 1-1/4"
6
9271062-TR
Screw Tek 1/4" x 1-1/4" BH TR
9
9333042
Washer Flat 3/8" x 7/8" O.D.
9
9610012
Rivet 3/16" x 1/2" to 3/4" Pop
2
4 DISC ASSEMBLY
Part #
DESCRIPTION
QTY
DE-4373
Disc Climber Disc
4
EG-4442
Disc Climber Cap
1
FS-1233-4
Disc Climber Post 48"
1
GG-8135
Post Cap R3.5 Dome
1
9103032-TR
Bolt Button Head 3/8" x 3/4"
3
9103062-TR
Bolt Button Head 3/8" x 1-1/4"
9
9271062-TR
Screw Tek 1/4" x 1-1/4" BH TR
12
9333042
Washer Flat 3/8" x 7/8" O.D.
12
9610012
Rivet 3/16" x 1/2" to 3/4" Pop
2
5 DISC ASSEMBLY
Part #
DESCRIPTION
QTY
DE-4373
Disc Climber Disc
5
EG-4442
Disc Climber Cap
1
FS-1233-5
Disc Climber Post 60"
1
GG-8135
Post Cap R3.5 Dome
1
9103032-TR
Bolt Button Head 3/8" x 3/4"
3
9103062-TR
Bolt Button Head 3/8" x 1-1/4"
12
9271062-TR
Screw Tek 1/4" x 1-1/4" BH TR
15
9333042
Washer Flat 3/8" x 7/8" O.D.
15
9610012
Rivet 3/16" x 1/2" to 3/4" Pop
2
6 DISC ASSEMBLY
Part #
DESCRIPTION
QTY
DE-4373
Disc Climber Disc
6
EG-4442
Disc Climber Cap
1
FS-1233-6
Disc Climber Post 72"
1
GG-8135
Post Cap R3.5 Dome
1
9103032-TR
Bolt Button Head 3/8" x 3/4"
3
9103062-TR
Bolt Button Head 3/8" x 1-1/4"
15
9271062-TR
Screw Tek 1/4" x 1-1/4" BH TR
18
9333042
Washer Flat 3/8" x 7/8" O.D.
18
9610012
Rivet 3/16" x 1/2" to 3/4" Pop
2
Specifications
Parts List
Maintenance Manual.
Assembled Parts List
Periodically tighten all screws, bolts and nuts. A
periodic inspection of all parts is necessary. If a part
is broken or worn, replace immediately. For general
maintenance please refer to our Playground
Maintenance
Summary of Contents for Farm Sound Panel Insert R5
Page 17: ......
Page 31: ......
Page 35: ......
Page 47: ......
Page 48: ......
Page 49: ......
Page 55: ......
Page 59: ......
Page 63: ......
Page 71: ......
Page 75: ......
Page 79: ......
Page 101: ......
Page 113: ......
Page 119: ......
Page 139: ......
Page 143: ......
Page 145: ......
Page 159: ......
Page 171: ......
Page 179: ......
Page 183: ......
Page 184: ......
Page 185: ......
Page 191: ......
Page 197: ......
Page 207: ......
Page 211: ......
Page 217: ......
Page 221: ......
Page 227: ......
Page 235: ......
Page 239: ......
Page 243: ......
Page 263: ......
Page 297: ......
Page 301: ......
Page 314: ...Playground Equipment Maintenance Guidelines Page 13 of 13 NOTES...