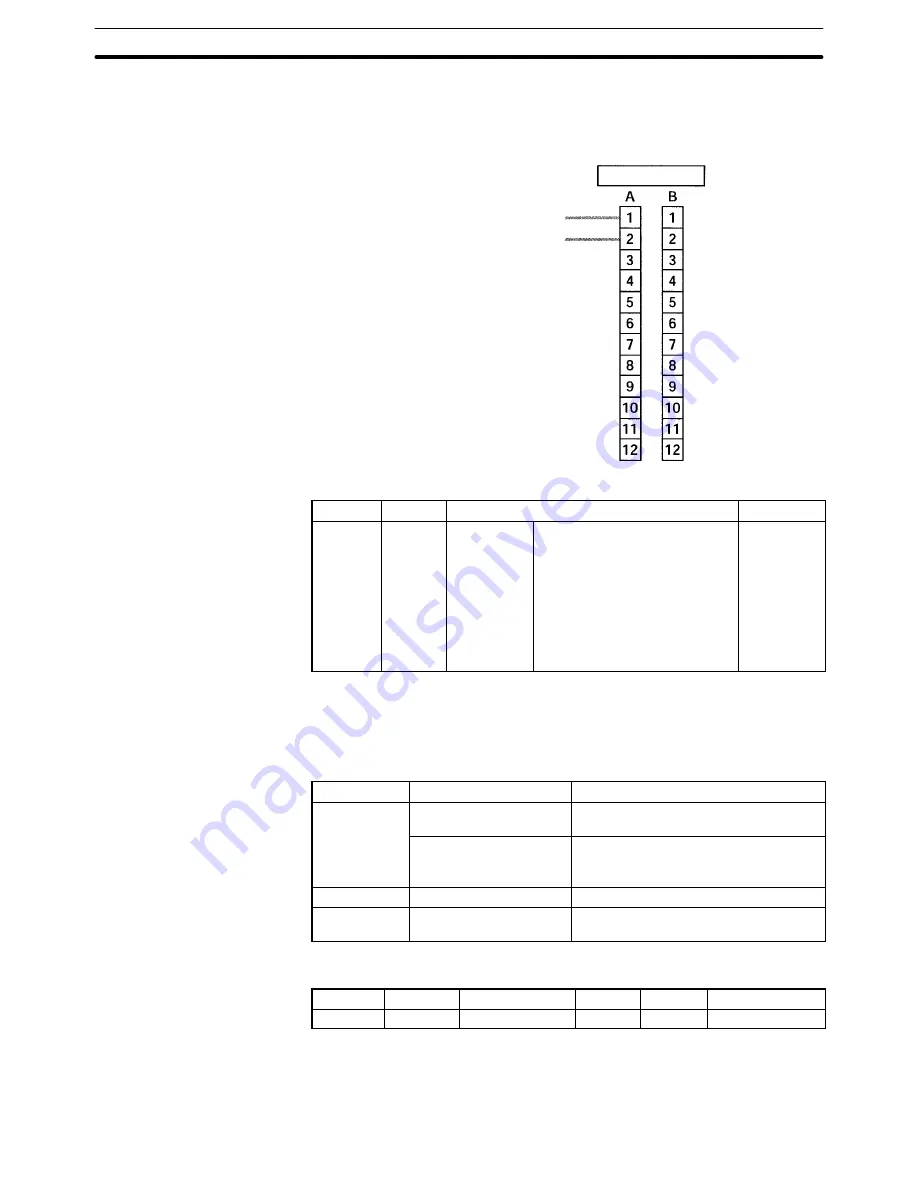
2-5
Section
CPM2A/CPM2C Pulse Output Functions
112
Note
The following examples are for Fujitsu-compatible connectors. Output bit ad-
dresses and connector pin numbers depend on the models. Refer to the
CPM2C
Operation Manual
(W356) or the
CPM2C-S Operation Manual
(W377) for de-
tails.
01000: Pulse output 0 (single-phase output)
01001: Pulse output 1 (single-phase output)
Output connector
(See above note.)
Make the following settings in the PC Setup.
Word
Bits
Function
Setting
DM 6642
08 to 15
High-speed
counter
setting
00: Do not use.
01: Use as high-speed counter
02: Use as synchronized pulse
control (10 to 500 Hz).
03: Use as synchronized pulse
control (20 Hz to 1 kHz).
04: Use as synchronized pulse
control (300 Hz to 20 kHz).
Either 00 or
01
Synchronized pulse control cannot be used simultaneously.
The settings will go into effect when the mode is changed (from PROGRAM to
MONITOR/RUN) or when the power supply is turned ON to the PC.
The following table shows the instruction operations related to pulse outputs
with variable duty ratio.
Instruction
Control
Operation
(@)PWM(––)
Pulse output with
variable duty ratio
Sets the frequency and duty ratio and
starts the pulse outputs.
Change duty ratio
Changes the duty ratio during pulse
while pulse outputs with variable duty
ratio are already in progress.
(@)INI(61)
Stop pulse outputs
Stops the pulse outputs.
(@)PRV(62)
Read pulse output status
Reads the pulse output status (during
pulse outputs).
The following table shows which instructions can be executed during pulse out-
puts without acceleration and deceleration.
PULS(65)
SPED(64)
INI(61)
PRV(62)
ACC(––)
PWM(––)
No
No
Yes (See note 1.) Yes
No
Yes (See note 2.)
Note
1. This instruction can be used only for stopping pulse outputs.
2. This instruction can be used only for changing the duty ratio. The frequency
cannot be changed while pulses are being output. If the frequency needs to
be changed, be sure to stop the pulse output first.
PC Setup
Ladder Diagram
Programming