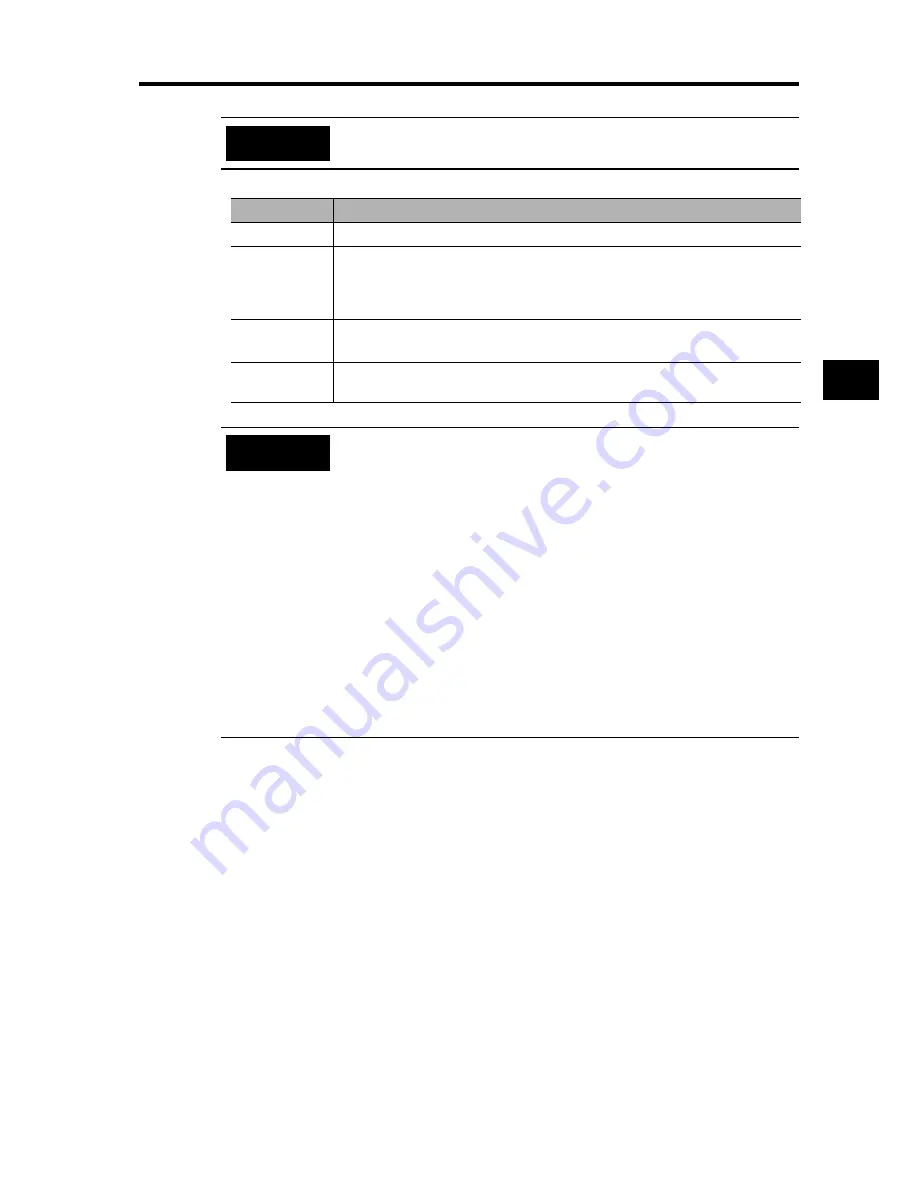
5-46
5-23 Adaptive Filter
Ope
rati
n
g Func
tions
5
The adaptive filter may not function properly under the following
conditions.
Conditions under which the adaptive filter does not function properly
Control Mode
In Torque Control Mode. (Operates in position and speed control modes)
Resonating load
status
If the resonance frequency is 300 Hz or lower.
If there are multiple points of resonance.
If the resonance peak or control gain is low, and the Servomotor speed is not
affected by it.
Load status
If the Servomotor speed with high-frequency components changes due to
backlash or other non-linear elements (play).
Command
pattern
If the acceleration/deceleration suddenly changes, i.e. 3,000 r/min or more in
0.1 s.
Unusual noise or vibration may occur until the adaptive filter stabilizes after
startup, immediately after the first servo ON, or when the Realtime
Autotuning Machine Rigidity Selection (Pn022) is increased, but this is not
a problem if it disappears right away. If the unusual noise or vibration,
however, continues for three or more reciprocating operations, take the
following measures in any order you can.
Write the parameters used during normal operation to the EEPROM.
Lower the Realtime Autotuning Machine Rigidity Selection (Pn022).
Disable the adaptive filter by setting the Adaptive Filter Selection (Pn023)
to 0. (Reset the inertia estimate and adaptive operation)
Set the notch filter manually.
Once unusual noise or vibration occurs, the Inertia Ratio (Pn020) may
have changed to an extreme value. In this case, also take the measures
described above.
The Adaptive Filter Table Number Display (Pn02F) is written to the
EEPROM every 30 minutes, and when the power supply is turned OFF
and turned ON again, this data is used as the initial values for the adaptive
operation.
Precautions
for Correct Use
Precautions
for Correct Use