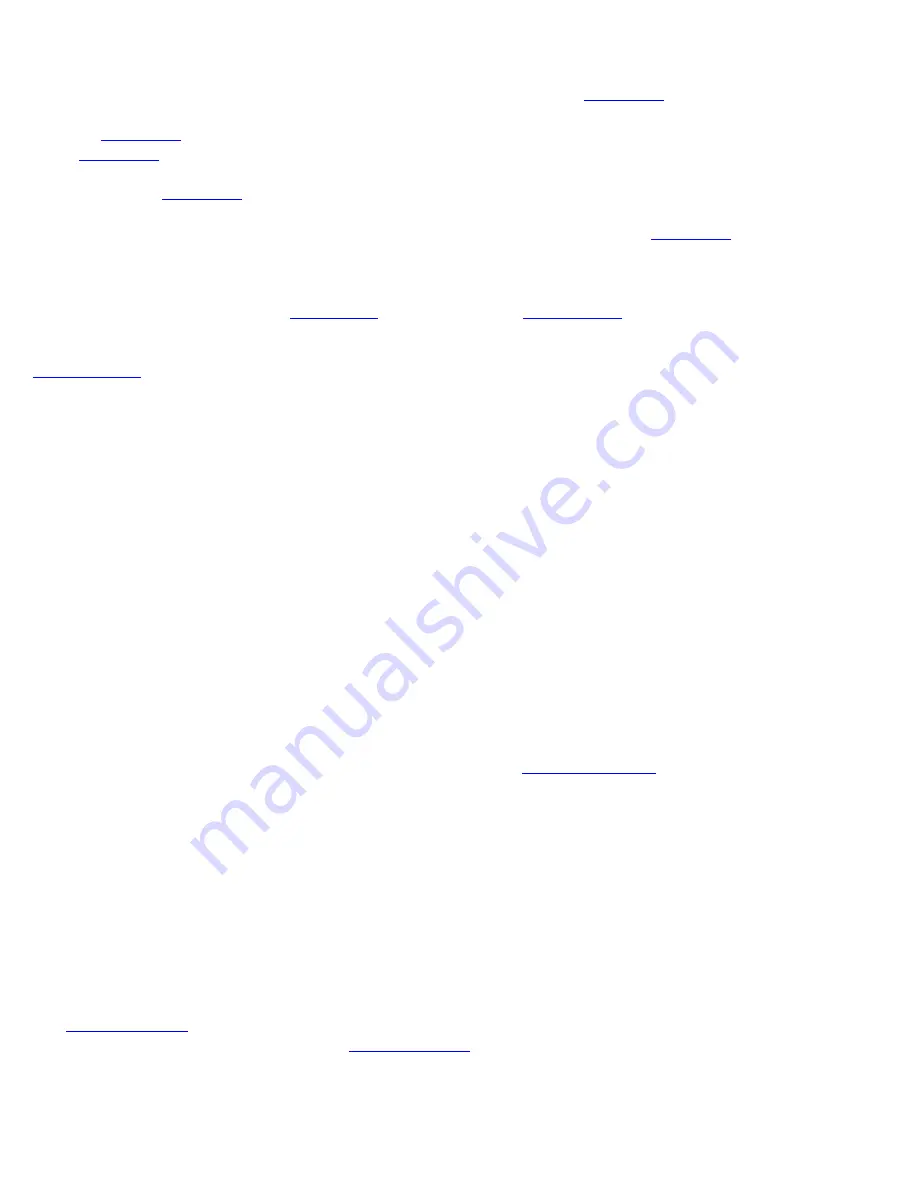
172 | ni.com | NI EDIDS-2400 Series User Manual
will not exceed 24-bit representation. This is a straight-forward calculation for encoder patterns. For example, if a
180-count encoder were used on the crankshaft, and it is desired to have a
tooth period timer for that speed (266666) must be checked so that it does not exceed a 24-bit value (2^24). It does
not, so a
of 50 RPM is acceptable. When EPT N-M 7 function is selected, extra attention must be given
to the
parameter. For example, if a 60-2 crank pattern is used, then there is a two-tooth gap, which
means that the timer period during the gap will be three times the period between the other evenly spaced teeth.
of 50 RPM correlates to an evenly spaced tooth period of 20 milliseconds. Therefore,
the period during the gap would be 60 milliseconds at 50 RPM. Sixty milliseconds correspond to a 40 MHz timer
value of 2400000, which can be represented by a 24-bit value. Therefore, a 50 RPM
this example.
The EPT function will lose sync in error when missing or extra crank/cam pulses are encountered where unexpected.
In all conditions, when sync is lost,
will be set to “Stopped”. A loss
of sync due to an error condition will be further signaled by the appropriate pattern-specific error flag on the EPT
tab. An error condition causing loss of sync will prevent any further sync until the error flag is cleared using the
button on the EPT tab. An obvious possible reason for such errors would be that the crank or cam
trigger wheel pattern does not match the configuration of the selected EPT function. If this is the case, the EPT will
either not sync at all or will lose sync almost immediately after initial sync. Assuming that the trigger wheel pattern is
correct, there is another common source of sync errors, which is electrical noise. This problem is discussed below,
along with some diagnostic techniques.
Electrical Noise
Electrical noise can be picked up and manifested in a wide variety of ways. There are a few guidelines that should
be followed for ensuring appropriate immunization against electrical noise. It is unlikely that noise will be introduced
on the crank or cam signals between the NI 9411 module and the cRIO controller. It is most likely that electrical noise
will be picked up along the wires between the sensor and the external connection to the NI 9411 module. If possible,
the wiring for sensors should be twisted shielded pairs and as short as possible. There should be few electrical
connections between the sensor and the module. The signals should be routed away, if possible, from high-current
wires such as injector wires or dynamometer wiring. The NI 9411 module should have a sensor signal ground
connected to its COM pin. Efforts should be made to fully understand all ground connections within the system,
making sure that ground connections are made in a “star” fashion instead of daisy-chain. Daisy-chain grounding can
lead to problematic ground loops where sensors and actuators use signal ground reference wires as a return path
for current back to ground. The wire used for NI 9411 COM ground reference should not be considered as a power
ground return path. If noise spikes are still causing false triggering of the digital input circuit, digital filtering may be
implemented within the DI Driver System using the integrated digital filter function. The digital filter rejects signal
pulses up to a specified width. The filter times are specified via the
window. It is common to use
a filter time of 1 to 5 microseconds. If filter times higher than 10 microseconds are required, then it is likely that noise
problems can be resolved in the external wiring.
Troubleshooting
Achieving reliable, clean crank and cam signals can sometimes be a trial and error process. It is National
Instruments’ experience that reliable sync is often not achieved with the first attempt at running the engine over the
entire speed and load range. Even though sync may occur successfully at low engine speeds, it does not always
mean that sync will be consistent at high speeds or loads due to trigger wheel imperfections, sensor placement
distance from the trigger teeth, ignition or injection radiated noise, or camshaft position lash or stretch with respect to
the crankshaft. The system engineer should take care to check that external signal shielding and routing are optimal
and that there is plenty of signal-edge margin for cam belt or chain stretch.
tab can be used to capture the crank and cam signals for diagnosing post-filter problems with
extraneous pulses or pulse alignment. The
tab can continuously display crank and cam signals and
then be stopped for analysis. The signals can be captured upon a loss of sync trigger to look at the crank and cam
signals captured before the loss of sync.
Summary of Contents for NI EDIDS-2400 Series
Page 2: ...2 ni com NI EDIDS 2400 Series User Manual...
Page 13: ...NI EDIDS 2400 Series User Manual National Instruments 13 3 2 Software...
Page 35: ...NI EDIDS 2400 Series User Manual National Instruments 35...
Page 43: ...NI EDIDS 2400 Series User Manual National Instruments 43 3 3 Hardware...
Page 48: ...48 ni com NI EDIDS 2400 Series User Manual 3 3 3 Connecting Injectors Sensors and Actuators...
Page 60: ...60 ni com NI EDIDS 2400 Series User Manual 3 3 5 b Side View of Optional Enclosure...
Page 86: ...86 ni com NI EDIDS 2400 Series User Manual See descriptions for PFI 1...
Page 241: ...NI EDIDS 2400 Series User Manual National Instruments 241 Aux PWX 2 4 See above descriptions...
Page 254: ...254 ni com NI EDIDS 2400 Series User Manual...
Page 268: ...268 ni com NI EDIDS 2400 Series User Manual...
Page 271: ...NI EDIDS 2400 Series User Manual National Instruments 271...
Page 294: ...294 ni com NI EDIDS 2400 Series User Manual...
Page 306: ...306 ni com NI EDIDS 2400 Series User Manual 22 TDK to cRIO Remote Connection...
Page 308: ...308 ni com NI EDIDS 2400 Series User Manual 8 Important Information...