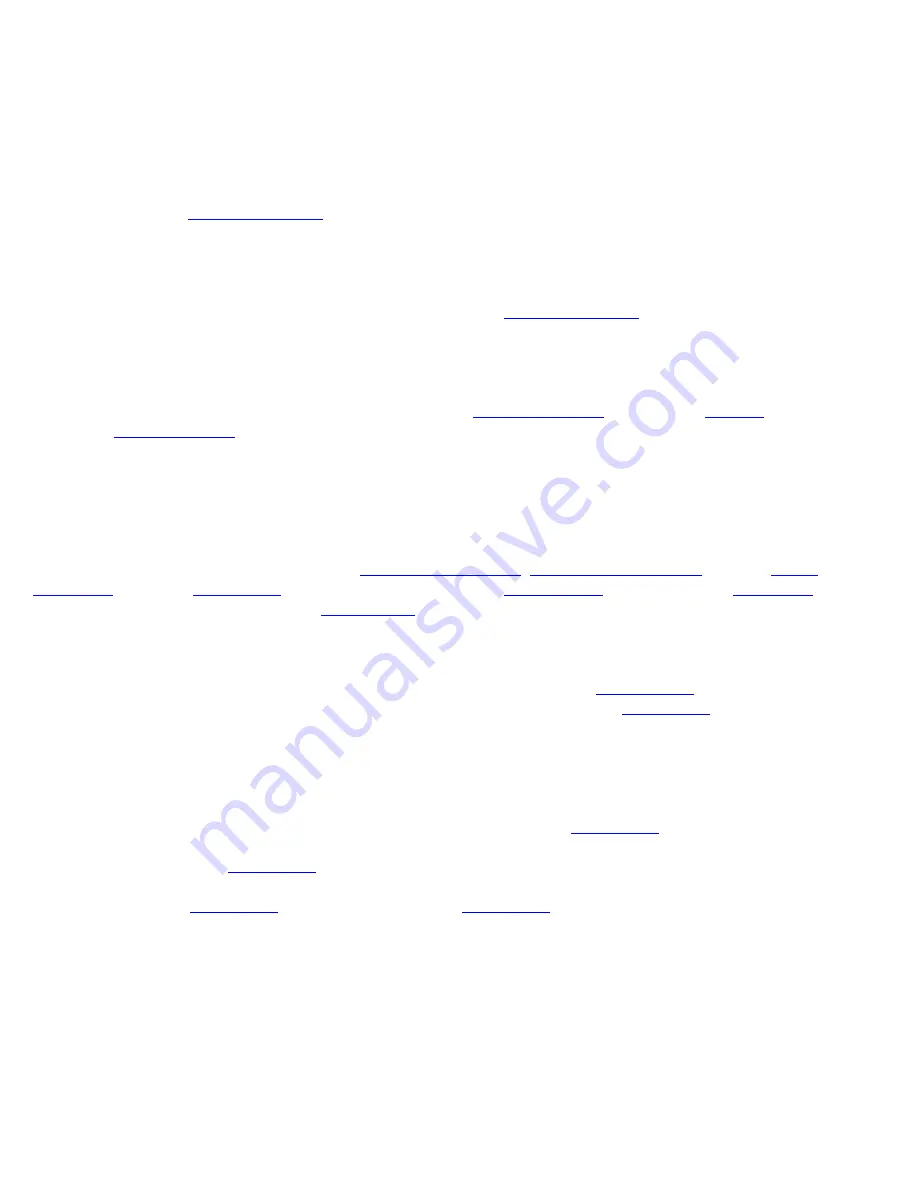
170 | ni.com | NI EDIDS-2400 Series User Manual
All EPT functions have a common internal core that tracks angular position. The supporting internal logic around the
core interprets the incoming crank and cam position pulses according to an expected pattern. Each EPT function
has a Boolean crankshaft and camshaft input. These signals may be connected via any available NI 9411 digital
input source within the DI Driver System. The pattern input signals are named according to the most common
engine applications, such that there is a crankshaft trigger wheel and an optional 4-stroke camshaft trigger wheel.
However, it is also possible to operate with a single trigger wheel mounted to a camshaft of a 4-stroke engine. This
would require routing the physical camshaft trigger wheel sensor signal into the Crank_DigChanAsn of the DI Driver
window description for assigning NI 9411 digital inputs to internal signals.
Digital Signal Filtering
It is often necessary to implement filtering of the crank and/or cam signals prior to entering the EPT function. The
DI Driver System software provides an integrating filter function which rejects positive and negative digital signal
pulses having a pulse width less than the filter time. Refer to the
window description for further
information about filtering the NI 9411 digital inputs.
EPT Pattern Simulation
All EPT functions contain a built in pattern simulation tool specific to the pattern for which the EPT function was
configured. Pattern simulation is turned on simply by setting
button of the
to
TRUE
and
setting the
to an appropriate value for the simulated speed. When simulation is turned on, the
Crank and Cam inputs to the EPT function are internally disconnected and replaced by the internally simulated
counterparts. The simulation feature allows the designer to bench test the DI Driver System functionality at any stage
of the development without the need for external simulation hardware.
Achieving Sync
In order for position tracking (sync) to start, a few conditions must be met. First, some pattern specific values must
be set correctly to the EPT function, such as
(if N-M),
, and
ON
. When
the stall speed (RPM) is exceeded, the
indicator will be set to
Spinning
and the EPT function begins
counting a complete cycle of crank teeth. After a complete engine cycle of crank teeth is received, the EPT function
begins looking for the first occurrence of a unique feature of the crankshaft and camshaft pattern which identifies an
absolute position. For example, if an N-M pattern is being used, the function searches for the occurrence of the M-
tooth gap. This is the moment of achieving sync. When sync is achieved, the
Sync
and the angular position of the crankshaft will be tracked. As sync is maintained,
will show the latest
crankshaft tooth count with respect to absolute 0 position. Each EPT function will have different rules for achieving
and maintaining sync, as well as location for absolute position 0. This information is contained in the EPT Pattern-
Specific Information section below.
CrankCount
During sync, the EPT function provides the latest crank tooth count at the
indicator, referenced to tooth
0. Tooth 0 is determined according to the pattern that is being tracked and is discussed within the Pattern-Specific
Information section below.
is provided in terms of a complete engine cycle and is reported as if there
were no missing or extra teeth in the pattern. For example, if the pattern type is N-M, NumberOfCrankTeeth = 60 and
will range from 0 to 119.
is for monitoring purposes only.
Crank Position
During sync, the EPT function calculates the latest crankshaft position in terms of absolute Crank Angle Ticks (CAT)
over a complete engine cycle, referenced to position 0. It is internally converted to a crank angle position in terms of
Crank Angle Degrees (CAD), referenced to position 0, so that injection angles may be specified in CAD. Position 0
is determined according to the pattern that is being tracked and is discussed within the Pattern-Specific Information
section below. The CurrentPosition in CAD is calculated according to the following:
CurrentPosition(CAD) = [CurrentPosition(CAT) * Stroke * 360] / MAX_CAT
Where Stroke = 2 if 4-stroke, and Stroke = 1 if 2-stroke.
Summary of Contents for NI EDIDS-2400 Series
Page 2: ...2 ni com NI EDIDS 2400 Series User Manual...
Page 13: ...NI EDIDS 2400 Series User Manual National Instruments 13 3 2 Software...
Page 35: ...NI EDIDS 2400 Series User Manual National Instruments 35...
Page 43: ...NI EDIDS 2400 Series User Manual National Instruments 43 3 3 Hardware...
Page 48: ...48 ni com NI EDIDS 2400 Series User Manual 3 3 3 Connecting Injectors Sensors and Actuators...
Page 60: ...60 ni com NI EDIDS 2400 Series User Manual 3 3 5 b Side View of Optional Enclosure...
Page 86: ...86 ni com NI EDIDS 2400 Series User Manual See descriptions for PFI 1...
Page 241: ...NI EDIDS 2400 Series User Manual National Instruments 241 Aux PWX 2 4 See above descriptions...
Page 254: ...254 ni com NI EDIDS 2400 Series User Manual...
Page 268: ...268 ni com NI EDIDS 2400 Series User Manual...
Page 271: ...NI EDIDS 2400 Series User Manual National Instruments 271...
Page 294: ...294 ni com NI EDIDS 2400 Series User Manual...
Page 306: ...306 ni com NI EDIDS 2400 Series User Manual 22 TDK to cRIO Remote Connection...
Page 308: ...308 ni com NI EDIDS 2400 Series User Manual 8 Important Information...