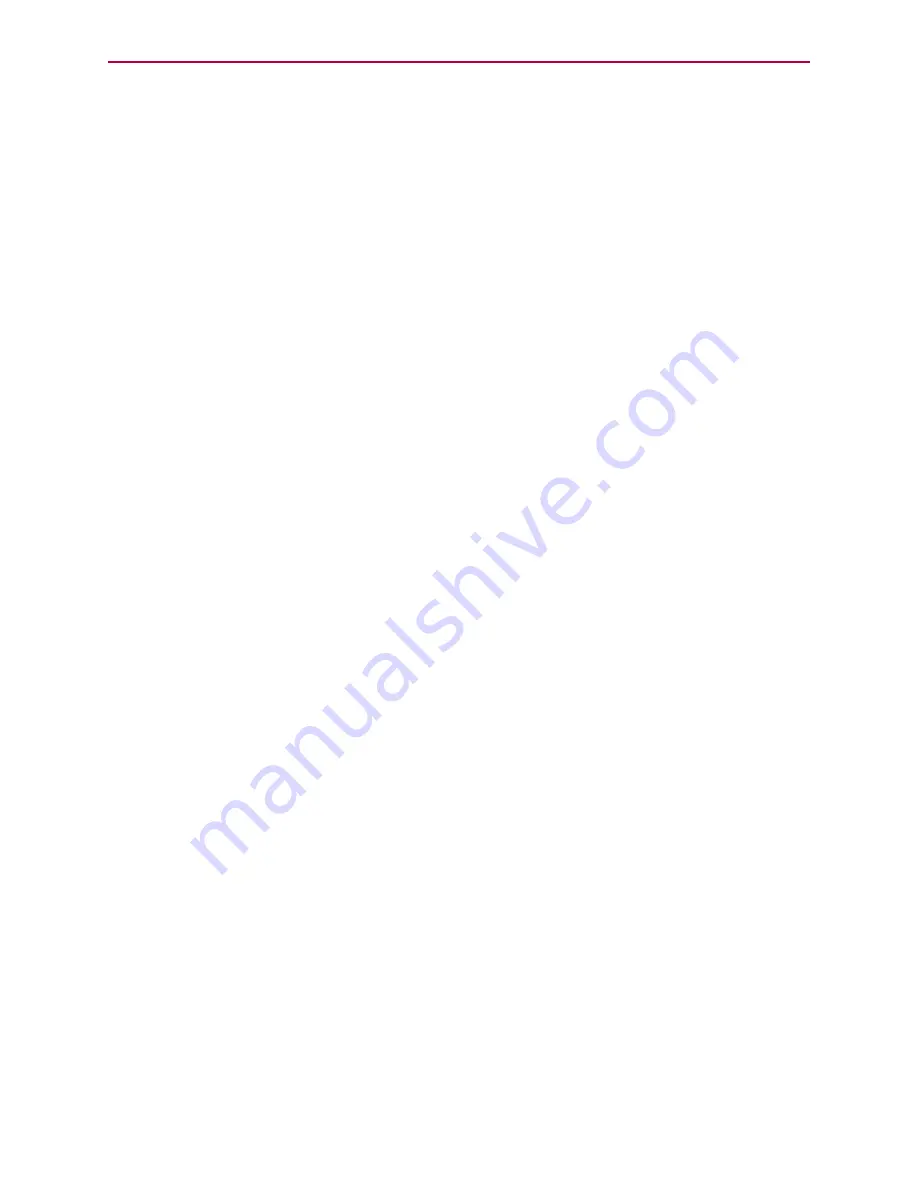
Machine Safety
Machine Safety
In order to protect personnel from any safety hazards in the machine or system, the machine/system
builder must perform a "Risk Assessment", which is often based on the ISO 13849 standard. The
design/implementation of barriers, emergency stop (E-stop) mechanisms and other safeguards will be
driven by the Risk Assessment and the safety standards specified by the governing authority (for
example, ISO, OSHA, UL, etc.) for the locale where the machine is being installed and operated. The
methodology and details of such an assessment are beyond the scope of this manual. However, there
are various sources of Risk Assessment information available in print and on the internet.
NOTE:
The following list is an example of items that would be evaluated when performing the Risk
Assessment. Additional items may be required. The safeguards must ensure the safety of all
personnel who may come in contact with or be in the vicinity of the machine.
In general, the machine/system safeguards must:
l
Provide a barrier to prevent unauthorized entry or access to the machine or system. The barrier
must be designed so that personnel cannot reach into any identified danger zones.
l
Position the control panel so that it is outside the barrier area but located for an unrestricted
view of the moving mechanism. The control panel must include an E-stop mechanism. Buttons
that start the machine must be protected from accidental activation.
l
Provide E-stop mechanisms located at the control panel and at other points around the
perimeter of the barrier that will stop all machine movement when tripped.
l
Provide appropriate sensors and interlocks on gates or other points of entry into the protected
zone that will stop all machine movement when tripped.
l
Ensure that if a portable control/programming device is supplied (for example, a hand-held
operator/programmer pendant), the device is equipped with an E-stop mechanism.
NOTE:
A portable operation/programming device requires
many
additional system design
considerations and safeguards beyond those listed in this section. For details, see the
safety standards specified by the governing authority (for example, ISO, OSHA, UL, etc.) for
the locale where the machine is being installed and operated.
l
Prevent contact with moving mechanisms (for example, arms, gears, belts, pulleys, tooling, etc.).
l
Prevent contact with a part that is thrown from the machine tooling or other part-handling
equipment.
l
Prevent contact with any electrical, hydraulic, pneumatic, thermal, chemical or other hazards
that may be present at the machine.
l
Prevent unauthorized access to wiring and power-supply cabinets, electrical boxes, etc.
l
Provide a proper control system, program logic and error checking to ensure the safety of all
personnel and equipment (for example, to prevent a run-away condition). The control system
must be designed so that it does not automatically restart the machine/system after a power
failure.
l
Prevent unauthorized access or changes to the control system or software.
Documentation and Training
It is the responsibility of the machine/system designer to provide documentation on safety, operation,
maintenance and programming, along with training for all machine operators, maintenance technicians,
programmers, and other personnel who may have access to the machine. This documentation must
include proper lockout/tagout procedures for maintenance and programming operations.
Moog Animatics Class 5 SmartMotor™
Installation and Startup Guide,
Rev. I
Page 9 of 76