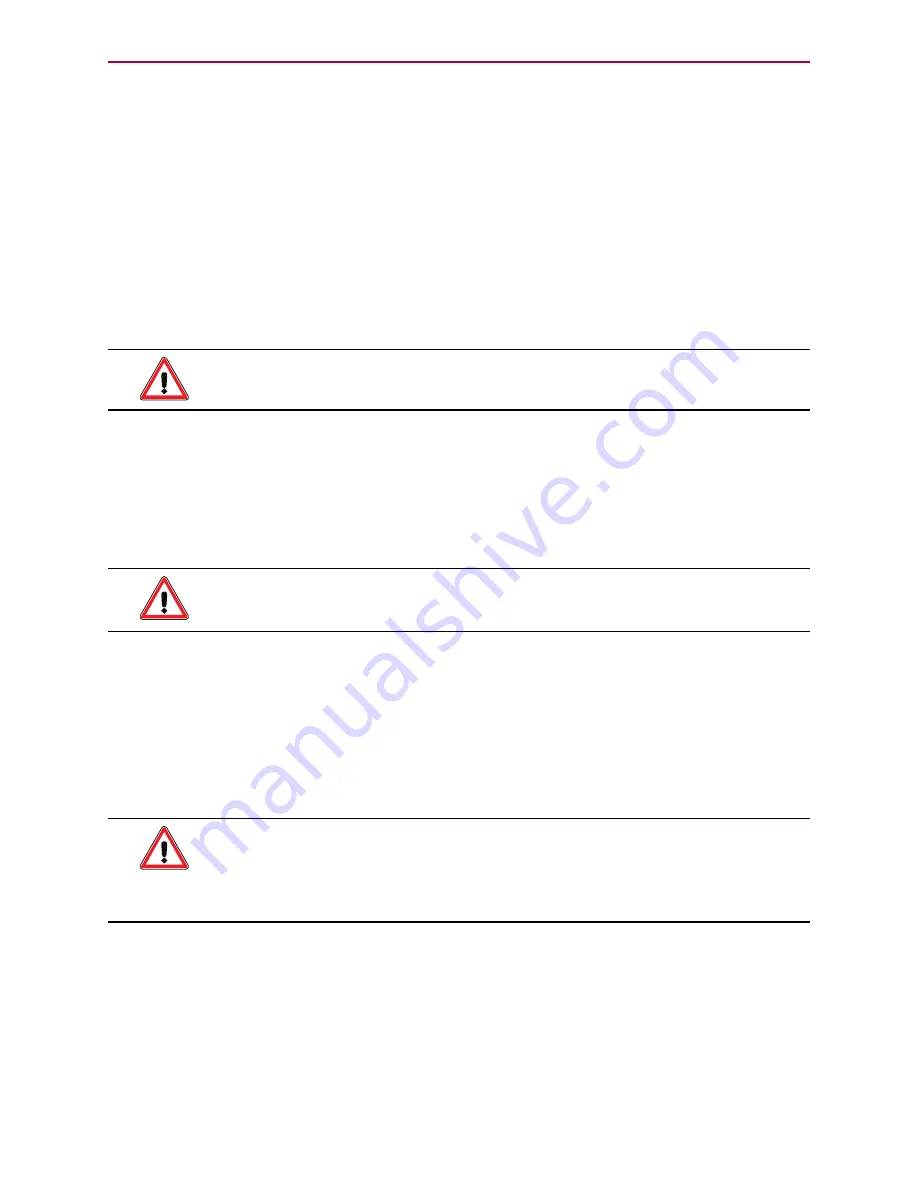
Understanding the Power Requirements
Understanding the Power Requirements
This section describes the power requirements for SmartMotor power, CPU
power, I/O power and
Communications power. For individual pin specifications, refer to Class 5 D-Style Connector Pinouts
on page 67,
and Class 5 M-Style Connector Pinouts on page 70, for D-style and M-style, respectively.
SmartMotor Power Requirements
Requirement:
The power range for D-style SmartMotors is from 24 VDC to 48 VDC; do not exceed 48
VDC. For the D-style AD1 option, do not exceed 24 VDC. Main power must be connected to a source
capable of supplying the rated power of the motor.
For M-style SmartMotors: Control power requires 24 VDC, do not exceed 24 VDC; motor power
requires from 24 VDC to 48 VDC, do not exceed 48 VDC.
CAUTION:
Control power for M-style motors must be 24 volts. They are not rated
for 48 volts.
Details:
Some of the larger SmartMotors can draw high current. Therefore, heavy gauge wire is required
to connect the large motors. As a result, Add-A-Motor cables are only recommended for series 17 and
23 motor frames. Control power consumes much less current. The exact amount depends on I/O,
communication and brake usage, but it is generally under 300 mA. For more information, see the CPU,
I/O and Communications Power section.
Voltages below 18 VDC could cause a brownout shutdown of the CPU, or what would appear as a
power-off reset, under sudden load changes.
CAUTION:
If power is reversed on any standard SmartMotors, immediate damage
WILL occur and the SmartMotor will no longer operate.
When relying on torque/speed curves, pay close attention to the voltage on which they are based.
During hard, fast decelerations, a SmartMotor can pull up supply voltages to the point of damage if a
shunt resistor pack is not used. Protective shunts are available from Moog Animatics.
Special care must be taken when near the upper voltage limit or in vertical applications that can back-
drive the SmartMotor. Gravity-influenced applications can turn the SmartMotor into a generator and
back-drive the power supply voltage above the safe limit for the SmartMotor. Many vertical
applications require a shunt to protect the SmartMotor from damage. Protective shunts are available
from Moog Animatics.
CAUTION:
Many vertical applications and applications with hard, fast
decelerations require shunts to protect the SmartMotor from damage. Note that
shunts should always be placed between the motor input and any disconnect or E-
stop relay to protect the motor when power is off or E-stop relay contacts are
open.
Moog Animatics Class 5 SmartMotor™
Installation and Startup Guide,
Rev. I
Page 33 of 76