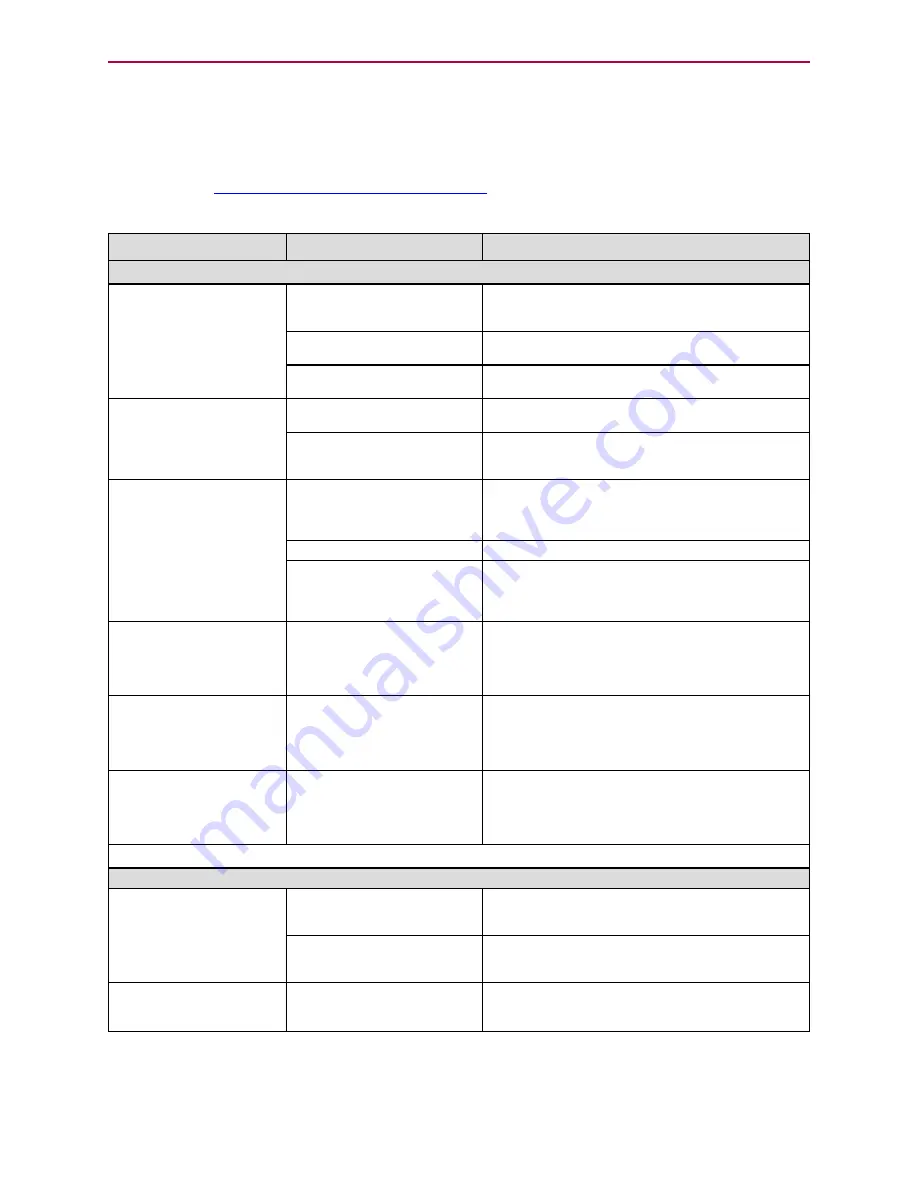
Troubleshooting
Troubleshooting
This section provides troubleshooting information for common problems. For additional support
resources, see:
http://www.animatics.com/support.html
.
Issue
Cause
Solution
Communication and Control Issues
Motor control power light
does not illuminate.
Control power is off,
disconnected or incorrectly
wired.
Check that control power is connected to the proper pins
and turned on. For connection details, see Connecting
the System on page 35.
Motor has routed drive power
through drive-enable pins.
Ensure cabling is correct and drive power is not being
delivered through the 15-pin connector.
Motor is equipped with the DE
option.
To energize control power, apply 24-48 VDC to pin 15
and ground to pin 14.
Motor does not communicate
with SMI.
Transmit, receive or ground pins
are not connected correctly.
Ensure that transmit, receive and ground are all
connected properly to the host PC.
Motor program is stuck in a
continuous loop or is disabling
communications.
To prevent the program from running on power up, use
the Communications Lockup Wizard located on the
SMI
software Communications menu.
Motor disconnects from SMI
sporadically.
COM port buffer settings are too
high.
Adjust the COM port buffer settings to their lowest
values. This is done In the Windows Device Manager>
Advanced Settings dialog box for the associated COM
port driver.
Poor connection on serial cable.
Check the serial cable connections and/or replace it.
Power supply unit (PSU)
brownout.
PSU may be undersized for the application, which causes
it to brown-out during motion. Make moves less
aggressive, increase PSU size or change to a linear
unregulated power supply.
Motor stops communicating
after power reset, requires
redetection.
Motor does not have its address
set in the user program.
NOTE:
Serial addresses are lost
when motor power is off or
reset.
Use the SADDR or ADDR= command within the program
to set the motor address. If there is more than one motor
in a serial daisy chain, ensure the ECHO command is in
the downloaded program.
Red PWR SERVO light
illuminated.
Red LED indicates the drive
stage is OFF. This may be due to
never having been turned on yet,
or a critical shaft protection
fault.
To discover the source of the fault, use the Motor View
tool located on the SMI software Tools menu.
Motor doesn't turn.
Faults not cleared and/or drive
enable not satisfied.
Clear faults (see Checking and Clearing the Status Bits
on page 59).
Satisfy the drive enable input (see Connecting the Sys-
tem on page 35).
Common Faults
Bus voltage fault.
Bus voltage is too high for
operation.
Check servo bus voltage. Check for excessive
regenerative energy from motor due to no/insufficient
shunt resistor.
Bus voltage is too low for
operation.
If motor uses the DE power option, ensure that both
drive and control power are connected. Ensure the power
supplies are sized correctly for the motor.
Overcurrent occurred.
Motor intermittently drew more
than its rated level of current.
Does not cease motion.
Consider making motion less abrupt with softer tuning
parameters or lower acceleration profiles.
Moog Animatics Class 5 SmartMotor™
Installation and Startup Guide,
Rev. I
Page 74 of 76