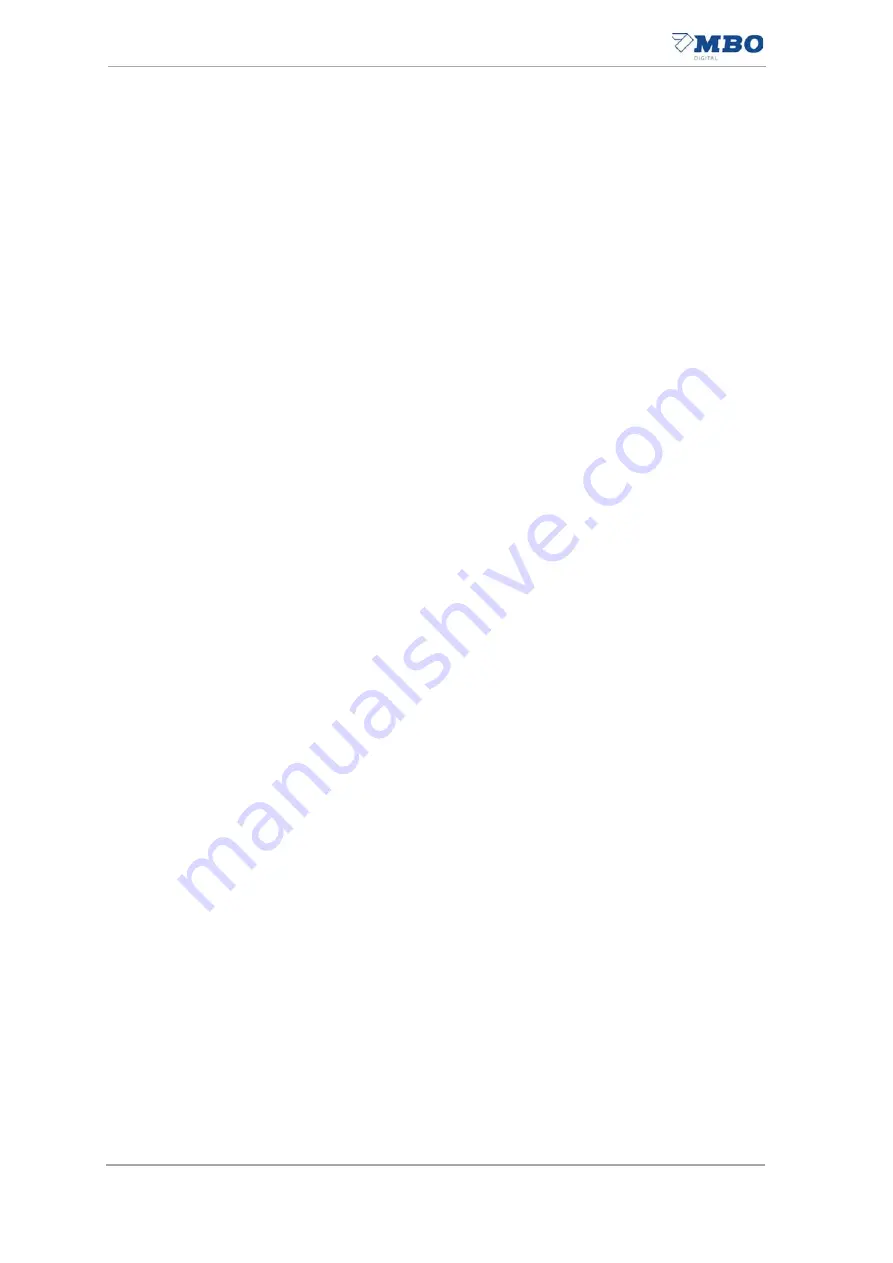
118
Sheeter SVC 525C
Adjustment and operation
Adjusting the machine
Here's how to set the longitudinal cut:
1) Adjust counter knife (5) to the desired position.
2) Tear paper at the position.
3) Plunge the knife (4) in.
Reverse the lever of the knife.
4) Adjust the knife (4) with slight pressure on the counter knife (5).
5) Lift the knife (3) again.
6) Adjust the other side precisely to the format width.
7) Attach the suction devices (2) below the cutting position and feed the
strips into the suction device.
8) Let the web run for a few meters and use the adjusting wheel (1) to slide
the cut to the desired position.
Longitudinal cut is adjusted.
Summary of Contents for SVC 525C
Page 1: ...Sheeter Translation of the original operating manual Keep for future reference SVC525C ...
Page 48: ...44 Sheeter SVC 525C Product description Technical data ...
Page 66: ...62 Sheeter SVC 525C Structure and function Protective devices ...
Page 90: ...86 Sheeter SVC 525C Transport interim storage Interim storage of the machine ...