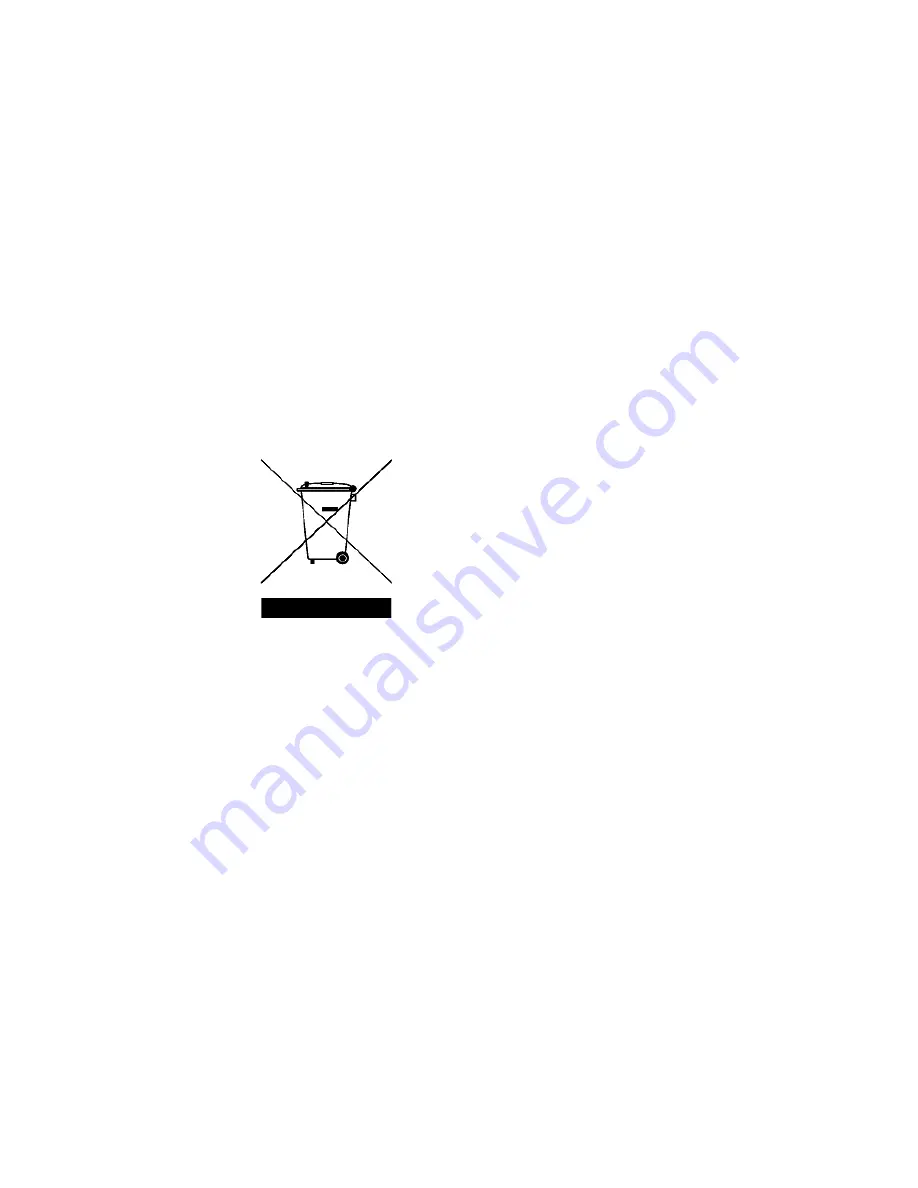
8
U3606A User’s and Service Guide
Waste Electrical and Electronic Equipment (WEEE) Directive 2002/96/EC
This instrument complies with the WEEE Directive (2002/96/EC) marking requirement.
This affixed product label indicates that you must not discard this electrical or electronic
product in domestic household waste.
Product Category:
With reference to the equipment types in the WEEE directive Annex 1, this instrument is
classified as a “Monitoring and Control Instrument” product.
The affixed product label is as shown below.
Do not dispose in domestic household waste
To return this unwanted instrument, contact your nearest Keysight Technologies, or visit:
www.keysight.com/environment/product
for more information.
Summary of Contents for U3606A
Page 1: ...Keysight U3606A Multimeter DC Power Supply User s and Service Guide ...
Page 2: ......
Page 12: ...12 U3606A User s and Service Guide ...
Page 128: ...3 DC Power Supply Operation Remote Sensing 106 U3606A User s and Service Guide ...
Page 160: ...4 System Related Operation Remote Operation 138 U3606A User s and Service Guide ...
Page 242: ...6 Calibration Procedures Adjustments procedures 220 U3606A User s and Service Guide ...
Page 291: ...List of Error Messages 9 Error Messages U3606A User s and Service Guide 269 ...