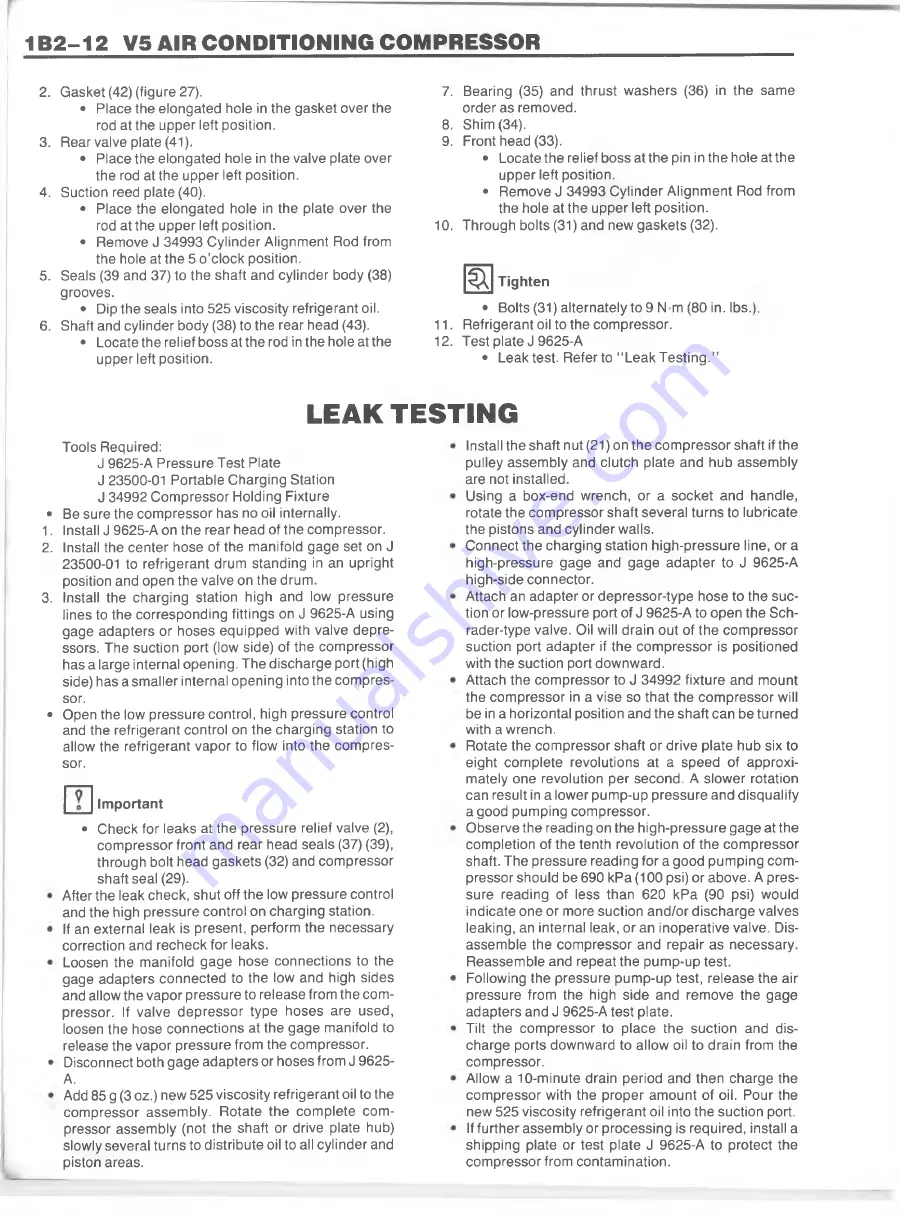
1B2-12 V5 AIR CONDITIONING COMPRESSOR
2. Gasket (42) (figure 27).
• Place the elongated hole in the gasket over the
rod at the upper left position.
3. Rear valve plate (41).
• Place the elongated hole in the valve plate over
the rod at the upper left position.
4. Suction reed plate (40).
• Place the elongated hole in the plate over the
rod at the upper left position.
• Remove J 34993 C ylinder Alignm ent Rod from
the hole at the 5 o ’clock position.
5. Seals (39 and 37) to the shaft and cylinder body (38)
grooves.
• Dip the seals into 525 viscosity refrigerant oil.
6. Shaft and cylinder body (38) to the rear head (43).
• Locate the relief boss at the rod in the hole at the
upper left position.
7. Bearing (35) and thrust washers (36) in the same
order as removed.
8. Shim (34).
9. Front head (33).
• Locate the relief boss at the pin in the hole at the
upper left position.
• Remove J 34993 C ylinder Alignm ent Rod from
the hole at the upper left position.
10. Through bolts (31) and new gaskets (32).
$
Tighten
• Bolts (31) alternately to 9 N m (80 in. lbs.
11. Refrigerant oil to the compressor.
12. Test plate J 9625-A
• Leak test. Refer to “ Leak T estin g.”
LEAK TESTING
Tools Required:
J 9625-A Pressure Test Plate
J 23500-01 Portable C harging Station
J 34992 Com pressor Holding Fixture
• Be sure the com pressor has no oil internally.
1. Install J 9625-A on the rear head of the compressor.
2. Install the center hose of the m anifold gage set on J
23500-01 to refrigerant drum standing in an upright
position and open the valve on the drum.
3. Install the charging station high and low pressure
lines to the corresponding fittings on J 9625-A using
gage adapters or hoses equipped with valve depre
ssors. The suction port (low side) of the com pressor
has a large internal opening. The discharge port (high
side) has a sm aller internal opening into the com pres
sor.
• Open the low pressure control, high pressure control
and the refrigerant control on the charging station to
allow the refrigerant vapor to flow into the com pres
sor.
Important
• Check for leaks at the pressure relief valve (2),
com pressor front and rear head seals (37) (39),
through bolt head gaskets (32) and compressor
shaft seal (29).
After the leak check, shut off the low pressure control
and the high pressure control on charging station.
If an external leak is present, perform the necessary
correction and recheck for leaks.
Loosen the manifold gage hose connections to the
gage adapters connected to the low and high sides
and allow the vapor pressure to release from the com
pressor. If valve depressor type hoses are used,
loosen the hose connections at the gage manifold to
release the vapor pressure from the compressor.
Disconnect both gage adapters or hoses from J 9625-
A.
Add 85 g (3 oz.) new 525 viscosity refrigerant oil to the
com pressor assem bly. Rotate the com plete com
pressor assem bly (not the shaft or drive plate hub)
slowly several turns to distribute oil to all cylinder and
piston areas.
Install the shaft nut (21) on the com pressor shaft if the
pulley assem bly and clutch plate and hub assem bly
are not installed.
Using a box-end wrench, or a socket and handle,
rotate the com pressor shaft several turns to lubricate
the pistons and cylinder walls.
Connect the charging station high-pressure line, or a
high-pressure gage and gage adapter to J 9625-A
high-side connector.
Attach an adapter or depressor-type hose to the suc
tion or low-pressure port of J 9625-A to open the Sch-
rader-type valve. Oil will drain out of the com pressor
suction port adapter if the com pressor is positioned
with the suction port downward.
Attach the com pressor to J 34992 fixture and mount
the com pressor in a vise so that the com pressor will
be in a horizontal position and the shaft can be turned
with a wrench.
Rotate the com pressor shaft or drive plate hub six to
eight com plete revolutions at a speed of approxi
mately one revolution per second. A slower rotation
can result in a lower pum p-up pressure and disqualify
a good pum ping compressor.
Observe the reading on the high-pressure gage at the
completion of the tenth revolution of the com pressor
shaft. The pressure reading for a good pum ping com
pressor should be 690 kPa (100 psi) or above. A pres
sure reading of less than 620 kPa (90 psi) would
indicate one or more suction and/or discharge valves
leaking, an internal leak, or an inoperative valve. Dis
assemble the com pressor and repair as necessary.
Reassemble and repeat the pum p-up test.
Following the pressure pum p-up test, release the air
pressure from the high side and remove the gage
adapters and J 9625-A test plate.
Tilt the com pressor to place the suction and dis
charge ports downward to allow oil to drain from the
compressor.
Allow a 10-minute drain period and then charge the
com pressor with the proper amount of oil. Pour the
new 525 viscosity refrigerant oil into the suction port.
If further assem bly or processing is required, install a
shipping plate or test plate J 9625-A to protect the
com pressor from contam ination.
Summary of Contents for 1989 Light Duty Truck
Page 1: ...vr V Light Duty Truck Unit Repair Manual...
Page 2: ......
Page 11: ...GENERAL INFORMATION OA 5 Figure 8 RV Models...
Page 13: ...GENERAL INFORMATION OA 7 Figure 11 ST Models...
Page 18: ......
Page 44: ......
Page 76: ...1B3 18 R 4 AIR CONDITIONING COMPRESSOR N...
Page 114: ......
Page 162: ......
Page 176: ...4B3 14 91 2 INCH RING GEAR...
Page 192: ...4B5 4 DANA REAR AXLES Figure 4 Spreading the Differential Case Figure 7 Removing the Ring Gear...
Page 218: ......
Page 220: ...4B6 2 12 INCH RING GEAR ROCKWELL F 04734 Figure 1 Rear Axle Components...
Page 229: ...12 INCH RING GEAR ROCKWELL 4B6 11 SPECIAL TOOLS Special Tools...
Page 230: ...4B6 12 12 INCH RING...
Page 240: ...4B7 10 LOCKING DIFFERENTIALS SPECIAL TOOLS Special Tools...
Page 260: ...4C2 6 93 4 INCH RING GEAR FRONT AXLE Figure 16 Removing the Pinion Inner Bearing...
Page 273: ...T TRUCK FRONT AXLE 4C3 3 F 05785 Figure 1 Axle Components...
Page 291: ...K TRUCK FRONT AXLE 4C4 3 Figure 1 Front Axle Com ponents K 15 25 Models...
Page 293: ...K TRUCK FRONT AXLE 4C4 5 Figure 3 Front Axle Com ponents K35 Models...
Page 318: ...C4 30 K TRUCK FBOHT AXLE...
Page 334: ......
Page 361: ...2 5 LITER L4 ENGINE 6A1 5 Figure 3 Cylinder Head Manifolds and Components...
Page 363: ...2 5 LITER L4 ENGINE 6A1 7 F 05715 Figure 5 Block and Components...
Page 395: ...2 8 LITER V 6 6A2 3 Figure 1 Engine Lubrication Diagram...
Page 396: ...6A2 4 2 8 LITER V 6 Figure 2 Engine Lubrication Diagram...
Page 424: ...6A2 32 2 8 LITER V 6...
Page 427: ...I 4 3 LITER V 6 6A3 3 Figure 1 Engine Lubrication Diagram B 07857...
Page 451: ...4 3 LITER V 6 6A3 27 SPECIFICATIONS ENGINE SPECIFICATIONS F 6344...
Page 457: ...4 8 LITER L6 6A4 3 Figure 2 Lubrication Diagram Front View...
Page 460: ...6A4 6 4 8 LITER L6 C 1 107 112 fK 108 3 109 165 129 B 05056 Figure 5 Block and Components...
Page 490: ...Ml...
Page 493: ...V8 ENGINE 6A5 3 Figure 1 Lubrication Diagram 5 0L and 5 7L Engines...
Page 494: ...6A5 4 V8 ENGINE Figure 2 Lubrication Diagram 5 0L and 5 7L Engines...
Page 530: ...6A5 40 V8 ENGINE Figure 81 Exhaust Manifold 7 4L Engines Figure 82 Water Pumps and Components...
Page 571: ...6 2 LITER DIESEL 6A7 35 Figure 58 Vacuum Pump Installed...
Page 576: ......
Page 582: ...6C1 6 MODEL 1MEF CARBURETOR Figure 9 Monojet Model 1MEF...
Page 604: ...6C2 6 MODEL M4MEF CARBURETOR Figure 9 Model M4MEF...
Page 640: ...6C4 8 MODEL 700 THROTTLE BODY...
Page 652: ...nmm...
Page 672: ......
Page 693: ...DISTRIBUTORS 6D5 13 Figure 27 Testing the Pickup Coil Figure 28 Testing the Ignition Coil...
Page 696: ......
Page 698: ...7A1 2 700 R4 AUTOMATIC TRANSMISSION Figure 1 Case and External Parts J H 0 0 5 3 7 0 0 R 4 R 2...
Page 745: ...700 R4 AUTOMATIC TRANSMISSION 7A1 49...
Page 762: ...7A2 2 400 475 AUTOMATIC TRANSMISSION Figure 1 Case and External Parts H H 0021 400 R 3...
Page 773: ...400 475 AUTOMATIC TRANSMISSION 7A2 13 Figure 29 Internal Parts H H 0 0 4 3 4 0 0 R 2...
Page 797: ...400 475 AUTOMATIC TRANSMISSION 7A2 37 Figure 93 Control Valve Assem bly...
Page 803: ...400 475 AUTOMATIC TRANSMISSION 7A2 43 Figure 104 Bushing Replacement Procedure...
Page 808: ...J c I i sal...
Page 838: ......
Page 840: ......
Page 842: ......
Page 850: ...7B1 12 HM 290 MANUAL TRANSMISSION J i t i a x V L...
Page 856: ...7B1 18 HM 290 MANUAL TRANSMISSION...
Page 892: ...7B1 54 HM 290 MANUAL TRANSMISSION Figure 93 Special Tools...
Page 897: ...HM 117 TRANSMISSION 7B2 5...
Page 901: ...HM 117 TRANSMISSION 7B2 9 B 05180 Figure 17 Installing the 1st and 2nd Synchronizer...
Page 912: ...20 HM...
Page 924: ...7B3 12 NEW PROCESS TRANSMISSION SPECIAL TOOLS...
Page 927: ...BORG WARNER TRANSMISSIONS 7B4 3 Figure 2 77 mm Transmission and Components...
Page 940: ...i ii iii m i in m i...
Page 944: ...7D1 4 TRANSFER CASE FO 5688 Figure 3 NP205 Transfer Case...
Page 952: ...7D1 12 TRANSFER CASE...
Page 963: ...NEW PROCESS 241 TRANSFER CASE 7D2 11 Figure 17 Oil Pump Pickup Screen Doweled Case Holes...
Page 964: ...7D2 12 NEW PROCESS 241 TRANSFER CASE Figure 18 NP 241 Transfer Case Cut Away...
Page 978: ......
Page 981: ...BORG WARNER 1370 TRANSFER CASE 7D4 3 J...
Page 992: ...7D4 14 BORG WARNER 1370 TRANSFER CASE Figure 26 Installing the Rear Output Yoke...
Page 993: ...BORG WARNER 1370 TRANSFER CASE 7D4 15 Figure 27 BW 1370 Transfer Case...
Page 997: ......
Page 998: ...X 8937...