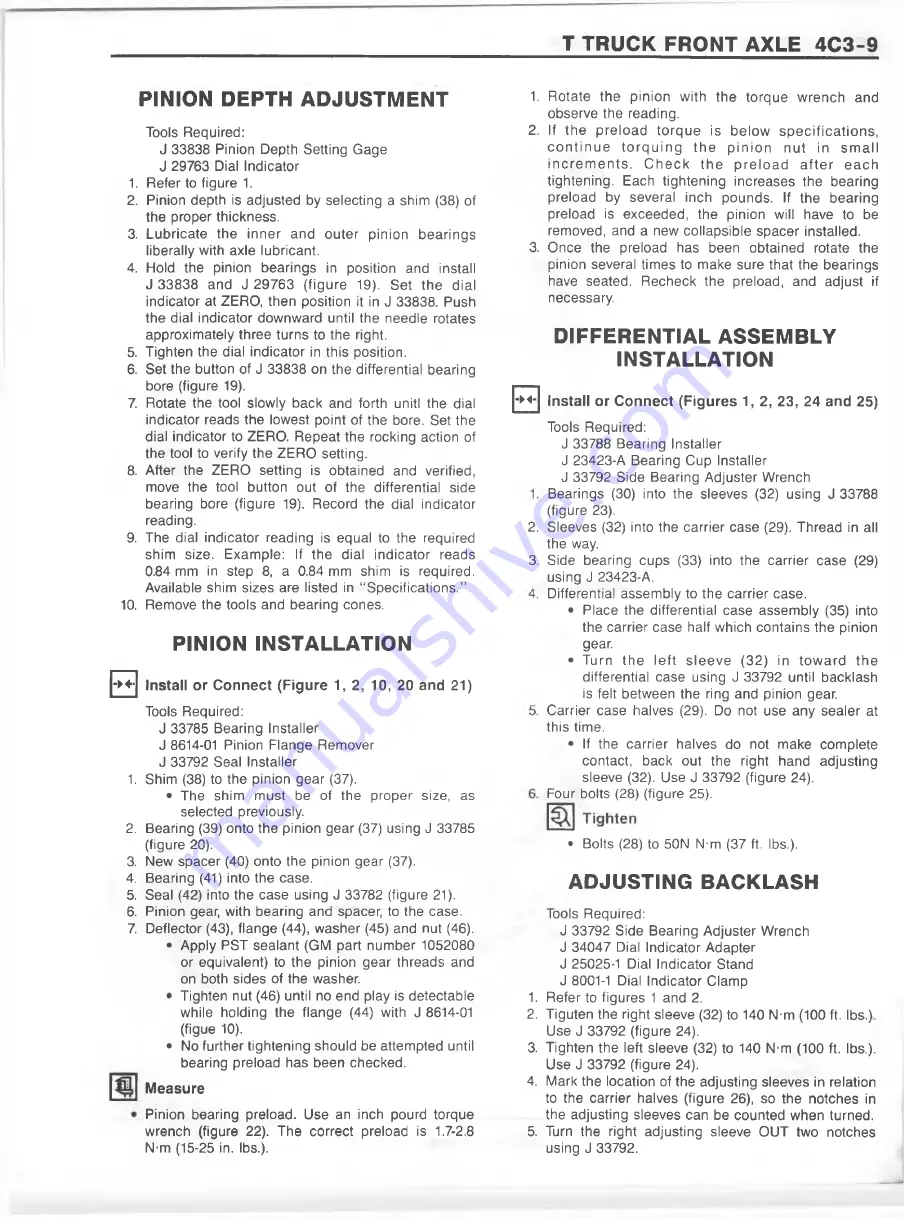
T TRUCK FRONT AXLE 4C3-9
PINION DEPTH ADJUSTMENT
Tools Required:
J 33838 Pinion Depth Setting Gage
J 29763 Dial Indicator
1. Refer to figure 1.
2. Pinion depth is adjusted by selecting a shim (38) of
the proper thickness.
3. Lubricate the inner and outer pinion bearings
liberally with axle lubricant.
4. Hold the pinion bearings in position and install
J 33838 and J 29763 (fig u re 19). Set the dial
indicator at ZERO, then position it in J 33838. Push
the dial indicator downward until the needle rotates
approximately three turns to the right.
5. Tighten the dial indicator in this position.
6. Set the button of J 33838 on the differential bearing
bore (figure 19).
7. Rotate the tool slowly back and forth unitl the dial
indicator reads the lowest point of the bore. Set the
dial indicator to ZERO. Repeat the rocking action of
the tool to verify the ZERO setting.
8. After the ZERO setting is obtained and verified,
move the tool button out of the differential side
bearing bore (figure 19). Record the dial indicator
reading.
9. The dial indicator reading is equal to the required
shim size. Exam ple: If the dial indicator reads
0.84 mm in step 8, a 0.84 mm shim is required.
Available shim sizes are listed in “ Specifications.”
10. Remove the tools and bearing cones.
PINION INSTALLATION
“►4- Install or C onnect (Figure 1, 2, 10, 20 and 21)
Tools Required:
J 33785 Bearing Installer
J 8614-01 Pinion Flange Remover
J 33792 Seal Installer
1. Shim (38) to the pinion gear (37).
• The shim must be of the proper size, as
selected previously.
2. Bearing (39) onto the pinion gear (37) using J 33785
(figure 20).
3. New spacer (40) onto the pinion gear (37).
4. Bearing (41) into the case.
5. Seal (42) into the case using J 33782 (figure 21).
6. Pinion gear, with bearing and spacer, to the case.
7. Deflector (43), flange (44), washer (45) and nut (46).
• Apply PST sealant (GM part number 1052080
or equivalent) to the pinion gear threads and
on both sides of the washer.
• Tighten nut (46) until no end play is detectable
while holding the flange (44) with J 8614-01
(figue 10).
• No further tightening should be attempted until
bearing preload has been checked.
M easure
Pinion bearing preload. Use an inch pourd torque
wrench (figure 22). The correct preload is 1.7-2.8
N-m (15-25 in. lbs.).
1. Rotate the pinion with the torque w rench and
observe the reading.
2. If th e p re lo a d to rq u e is b elow s p e c ific a tio n s ,
c o n tin u e to rq u in g th e p in io n n u t in s m a ll
in c re m e n ts . C h e c k th e p re lo a d a fte r e a c h
tightening. Each tightening increases the bearing
preload by several inch pounds. If the bearing
preload is exceeded, the pinion will have to be
removed, and a new collapsible spacer installed.
3. Once the preload has been obtained rotate the
pinion several times to make sure that the bearings
have seated. Recheck the preload, and adjust if
necessary.
DIFFERENTIAL ASSEMBLY
INSTALLATION
■H" Install or C o nnect (Figures 1, 2, 23, 24 and 25)
2
.
3.
Tools Required:
J 33788 Bearing Installer
J 23423-A Bearing Cup Installer
J 33792 Side Bearing Adjuster Wrench
Bearings (30) into the sleeves (32) using J 33788
(figure 23).
Sleeves (32) into the carrier case (29). Thread in all
the way.
Side bearing cups (33) into the carrier case (29)
using J 23423-A.
Differential assembly to the carrier case.
• Place the differential case assembly (35) into
the carrier case half which contains the pinion
gear.
• Turn th e le ft s le e v e (32) in to w a rd th e
differential case using J 33792 until backlash
is felt between the ring and pinion gear.
Carrier case halves (29). Do not use any sealer at
this time.
• If the carrier halves do not make complete
contact, back out the right hand adjusting
sleeve (32). Use J 33792 (figure 24).
Four bolts (28) (figure 25).
• Bolts (28) to 50N N-m (37 ft. lbs.).
ADJUSTING BACKLASH
Tools Required:
J 33792 Side Bearing Adjuster Wrench
J 34047 Dial Indicator Adapter
J 25025-1 Dial Indicator Stand
J 8001-1 Dial Indicator Clamp
1. Refer to figures 1 and 2.
2. Tiguten the right sleeve (32) to 140 N-m (100 ft. lbs.).
Use J 33792 (figure 24).
3. Tighten the left sleeve (32) to 140 N-m (100 ft. lbs.).
Use J 33792 (figure 24).
4. Mark the location of the adjusting sleeves in relation
to the carrier halves (figure 26), so the notches in
the adjusting sleeves can be counted when turned.
5. Turn the right adjusting sleeve OUT two notches
using J 33792.
Summary of Contents for 1989 Light Duty Truck
Page 1: ...vr V Light Duty Truck Unit Repair Manual...
Page 2: ......
Page 11: ...GENERAL INFORMATION OA 5 Figure 8 RV Models...
Page 13: ...GENERAL INFORMATION OA 7 Figure 11 ST Models...
Page 18: ......
Page 44: ......
Page 76: ...1B3 18 R 4 AIR CONDITIONING COMPRESSOR N...
Page 114: ......
Page 162: ......
Page 176: ...4B3 14 91 2 INCH RING GEAR...
Page 192: ...4B5 4 DANA REAR AXLES Figure 4 Spreading the Differential Case Figure 7 Removing the Ring Gear...
Page 218: ......
Page 220: ...4B6 2 12 INCH RING GEAR ROCKWELL F 04734 Figure 1 Rear Axle Components...
Page 229: ...12 INCH RING GEAR ROCKWELL 4B6 11 SPECIAL TOOLS Special Tools...
Page 230: ...4B6 12 12 INCH RING...
Page 240: ...4B7 10 LOCKING DIFFERENTIALS SPECIAL TOOLS Special Tools...
Page 260: ...4C2 6 93 4 INCH RING GEAR FRONT AXLE Figure 16 Removing the Pinion Inner Bearing...
Page 273: ...T TRUCK FRONT AXLE 4C3 3 F 05785 Figure 1 Axle Components...
Page 291: ...K TRUCK FRONT AXLE 4C4 3 Figure 1 Front Axle Com ponents K 15 25 Models...
Page 293: ...K TRUCK FRONT AXLE 4C4 5 Figure 3 Front Axle Com ponents K35 Models...
Page 318: ...C4 30 K TRUCK FBOHT AXLE...
Page 334: ......
Page 361: ...2 5 LITER L4 ENGINE 6A1 5 Figure 3 Cylinder Head Manifolds and Components...
Page 363: ...2 5 LITER L4 ENGINE 6A1 7 F 05715 Figure 5 Block and Components...
Page 395: ...2 8 LITER V 6 6A2 3 Figure 1 Engine Lubrication Diagram...
Page 396: ...6A2 4 2 8 LITER V 6 Figure 2 Engine Lubrication Diagram...
Page 424: ...6A2 32 2 8 LITER V 6...
Page 427: ...I 4 3 LITER V 6 6A3 3 Figure 1 Engine Lubrication Diagram B 07857...
Page 451: ...4 3 LITER V 6 6A3 27 SPECIFICATIONS ENGINE SPECIFICATIONS F 6344...
Page 457: ...4 8 LITER L6 6A4 3 Figure 2 Lubrication Diagram Front View...
Page 460: ...6A4 6 4 8 LITER L6 C 1 107 112 fK 108 3 109 165 129 B 05056 Figure 5 Block and Components...
Page 490: ...Ml...
Page 493: ...V8 ENGINE 6A5 3 Figure 1 Lubrication Diagram 5 0L and 5 7L Engines...
Page 494: ...6A5 4 V8 ENGINE Figure 2 Lubrication Diagram 5 0L and 5 7L Engines...
Page 530: ...6A5 40 V8 ENGINE Figure 81 Exhaust Manifold 7 4L Engines Figure 82 Water Pumps and Components...
Page 571: ...6 2 LITER DIESEL 6A7 35 Figure 58 Vacuum Pump Installed...
Page 576: ......
Page 582: ...6C1 6 MODEL 1MEF CARBURETOR Figure 9 Monojet Model 1MEF...
Page 604: ...6C2 6 MODEL M4MEF CARBURETOR Figure 9 Model M4MEF...
Page 640: ...6C4 8 MODEL 700 THROTTLE BODY...
Page 652: ...nmm...
Page 672: ......
Page 693: ...DISTRIBUTORS 6D5 13 Figure 27 Testing the Pickup Coil Figure 28 Testing the Ignition Coil...
Page 696: ......
Page 698: ...7A1 2 700 R4 AUTOMATIC TRANSMISSION Figure 1 Case and External Parts J H 0 0 5 3 7 0 0 R 4 R 2...
Page 745: ...700 R4 AUTOMATIC TRANSMISSION 7A1 49...
Page 762: ...7A2 2 400 475 AUTOMATIC TRANSMISSION Figure 1 Case and External Parts H H 0021 400 R 3...
Page 773: ...400 475 AUTOMATIC TRANSMISSION 7A2 13 Figure 29 Internal Parts H H 0 0 4 3 4 0 0 R 2...
Page 797: ...400 475 AUTOMATIC TRANSMISSION 7A2 37 Figure 93 Control Valve Assem bly...
Page 803: ...400 475 AUTOMATIC TRANSMISSION 7A2 43 Figure 104 Bushing Replacement Procedure...
Page 808: ...J c I i sal...
Page 838: ......
Page 840: ......
Page 842: ......
Page 850: ...7B1 12 HM 290 MANUAL TRANSMISSION J i t i a x V L...
Page 856: ...7B1 18 HM 290 MANUAL TRANSMISSION...
Page 892: ...7B1 54 HM 290 MANUAL TRANSMISSION Figure 93 Special Tools...
Page 897: ...HM 117 TRANSMISSION 7B2 5...
Page 901: ...HM 117 TRANSMISSION 7B2 9 B 05180 Figure 17 Installing the 1st and 2nd Synchronizer...
Page 912: ...20 HM...
Page 924: ...7B3 12 NEW PROCESS TRANSMISSION SPECIAL TOOLS...
Page 927: ...BORG WARNER TRANSMISSIONS 7B4 3 Figure 2 77 mm Transmission and Components...
Page 940: ...i ii iii m i in m i...
Page 944: ...7D1 4 TRANSFER CASE FO 5688 Figure 3 NP205 Transfer Case...
Page 952: ...7D1 12 TRANSFER CASE...
Page 963: ...NEW PROCESS 241 TRANSFER CASE 7D2 11 Figure 17 Oil Pump Pickup Screen Doweled Case Holes...
Page 964: ...7D2 12 NEW PROCESS 241 TRANSFER CASE Figure 18 NP 241 Transfer Case Cut Away...
Page 978: ......
Page 981: ...BORG WARNER 1370 TRANSFER CASE 7D4 3 J...
Page 992: ...7D4 14 BORG WARNER 1370 TRANSFER CASE Figure 26 Installing the Rear Output Yoke...
Page 993: ...BORG WARNER 1370 TRANSFER CASE 7D4 15 Figure 27 BW 1370 Transfer Case...
Page 997: ......
Page 998: ...X 8937...