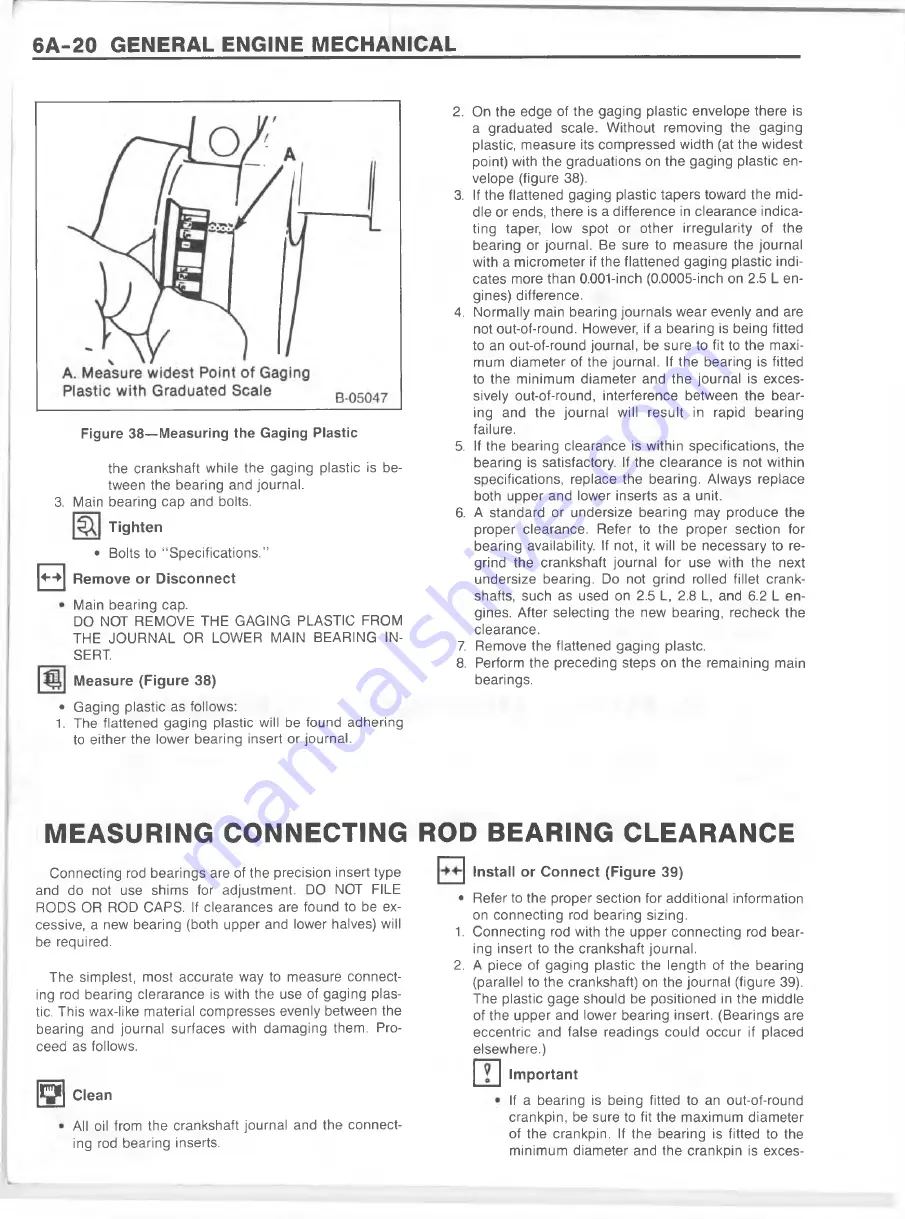
6A-20 GENERAL ENGINE MECHANICAL
Figure 38— Measuring the Gaging Plastic
the crankshaft while the gaging plastic is be
tween the bearing and journal.
3. Main bearing cap and bolts.
T ig h ten
• Bolts to “ Specifications.”
+-► R em ove or D isconnect
Main bearing cap.
DO NOT REMOVE THE GAGING PLASTIC FROM
THE JOURNAL OR LOWER MAIN BEARING IN
SERT
M easure (Figure 38)
• Gaging plastic as follows:
1. The flattened gaging plastic will be found adhering
to either the lower bearing insert or journal.
2. On the edge of the gaging plastic envelope there is
a graduated scale. W ithout removing the gaging
plastic, measure its compressed width (at the widest
point) with the graduations on the gaging plastic en
velope (figure 38).
3. If the flattened gaging plastic tapers toward the m id
dle or ends, there is a difference in clearance indica
ting taper, low spot or other irregularity of the
bearing or journal. Be sure to measure the journal
with a micrometer if the flattened gaging plastic indi
cates more than 0.001-inch (0.0005-inch on 2.5 L en
gines) difference.
4. Normally main bearing journals wear evenly and are
not out-of-round. However, if a bearing is being fitted
to an out-of-round journal, be sure to fit to the m axi
mum diameter of the journal. If the bearing is fitted
to the minimum diameter and the journal is exces
sively out-of-round, interference between the bear
ing and the journal will result in rapid bearing
failure.
5. If the bearing clearance is within specifications, the
bearing is satisfactory. If the clearance is not within
specifications, replace the bearing. Always replace
both upper and lower inserts as a unit.
6. A standard or undersize bearing may produce the
proper clearance. Refer to the proper section for
bearing availability. If not, it will be necessary to re
grind the crankshaft journal for use with the next
undersize bearing. Do not grind rolled fillet crank
shafts, such as used on 2.5 L, 2.8 L, and 6.2 L en
gines. After selecting the new bearing, recheck the
clearance.
7. Remove the flattened gaging plastc.
8. Perform the preceding steps on the remaining main
bearings.
MEASURING CONNECTING ROD BEARING CLEARANCE
Connecting rod bearings are of the precision insert type
and do not use shims for adjustment. DO NOT FILE
RODS OR ROD CAPS. If clearances are found to be ex
cessive, a new bearing (both upper and lower halves) will
be required.
The simplest, most accurate way to measure connect
ing rod bearing clerarance is with the use of gaging plas
tic. This wax-like material compresses evenly between the
bearing and journal surfaces with dam aging them. Pro
ceed as follows.
jn y
Clean
All oil from the crankshaft journal and the connect
ing rod bearing inserts.
Install or C onnect (Figure 39)
• Refer to the proper section for additional information
on connecting rod bearing sizing.
1. Connecting rod with the upper connecting rod bear
ing insert to the crankshaft journal.
2. A piece of gaging plastic the length of the bearing
(parallel to the crankshaft) on the journal (figure 39).
The plastic gage should be positioned in the middle
of the upper and lower bearing insert. (Bearings are
eccentric and false readings could occur if placed
elsewhere.)
Im portant
If a bearing is being fitted to an out-of-round
crankpin, be sure to fit the maximum diameter
of the crankpin. If the bearing is fitted to the
minimum diameter and the crankpin is exces-
Summary of Contents for 1989 Light Duty Truck
Page 1: ...vr V Light Duty Truck Unit Repair Manual...
Page 2: ......
Page 11: ...GENERAL INFORMATION OA 5 Figure 8 RV Models...
Page 13: ...GENERAL INFORMATION OA 7 Figure 11 ST Models...
Page 18: ......
Page 44: ......
Page 76: ...1B3 18 R 4 AIR CONDITIONING COMPRESSOR N...
Page 114: ......
Page 162: ......
Page 176: ...4B3 14 91 2 INCH RING GEAR...
Page 192: ...4B5 4 DANA REAR AXLES Figure 4 Spreading the Differential Case Figure 7 Removing the Ring Gear...
Page 218: ......
Page 220: ...4B6 2 12 INCH RING GEAR ROCKWELL F 04734 Figure 1 Rear Axle Components...
Page 229: ...12 INCH RING GEAR ROCKWELL 4B6 11 SPECIAL TOOLS Special Tools...
Page 230: ...4B6 12 12 INCH RING...
Page 240: ...4B7 10 LOCKING DIFFERENTIALS SPECIAL TOOLS Special Tools...
Page 260: ...4C2 6 93 4 INCH RING GEAR FRONT AXLE Figure 16 Removing the Pinion Inner Bearing...
Page 273: ...T TRUCK FRONT AXLE 4C3 3 F 05785 Figure 1 Axle Components...
Page 291: ...K TRUCK FRONT AXLE 4C4 3 Figure 1 Front Axle Com ponents K 15 25 Models...
Page 293: ...K TRUCK FRONT AXLE 4C4 5 Figure 3 Front Axle Com ponents K35 Models...
Page 318: ...C4 30 K TRUCK FBOHT AXLE...
Page 334: ......
Page 361: ...2 5 LITER L4 ENGINE 6A1 5 Figure 3 Cylinder Head Manifolds and Components...
Page 363: ...2 5 LITER L4 ENGINE 6A1 7 F 05715 Figure 5 Block and Components...
Page 395: ...2 8 LITER V 6 6A2 3 Figure 1 Engine Lubrication Diagram...
Page 396: ...6A2 4 2 8 LITER V 6 Figure 2 Engine Lubrication Diagram...
Page 424: ...6A2 32 2 8 LITER V 6...
Page 427: ...I 4 3 LITER V 6 6A3 3 Figure 1 Engine Lubrication Diagram B 07857...
Page 451: ...4 3 LITER V 6 6A3 27 SPECIFICATIONS ENGINE SPECIFICATIONS F 6344...
Page 457: ...4 8 LITER L6 6A4 3 Figure 2 Lubrication Diagram Front View...
Page 460: ...6A4 6 4 8 LITER L6 C 1 107 112 fK 108 3 109 165 129 B 05056 Figure 5 Block and Components...
Page 490: ...Ml...
Page 493: ...V8 ENGINE 6A5 3 Figure 1 Lubrication Diagram 5 0L and 5 7L Engines...
Page 494: ...6A5 4 V8 ENGINE Figure 2 Lubrication Diagram 5 0L and 5 7L Engines...
Page 530: ...6A5 40 V8 ENGINE Figure 81 Exhaust Manifold 7 4L Engines Figure 82 Water Pumps and Components...
Page 571: ...6 2 LITER DIESEL 6A7 35 Figure 58 Vacuum Pump Installed...
Page 576: ......
Page 582: ...6C1 6 MODEL 1MEF CARBURETOR Figure 9 Monojet Model 1MEF...
Page 604: ...6C2 6 MODEL M4MEF CARBURETOR Figure 9 Model M4MEF...
Page 640: ...6C4 8 MODEL 700 THROTTLE BODY...
Page 652: ...nmm...
Page 672: ......
Page 693: ...DISTRIBUTORS 6D5 13 Figure 27 Testing the Pickup Coil Figure 28 Testing the Ignition Coil...
Page 696: ......
Page 698: ...7A1 2 700 R4 AUTOMATIC TRANSMISSION Figure 1 Case and External Parts J H 0 0 5 3 7 0 0 R 4 R 2...
Page 745: ...700 R4 AUTOMATIC TRANSMISSION 7A1 49...
Page 762: ...7A2 2 400 475 AUTOMATIC TRANSMISSION Figure 1 Case and External Parts H H 0021 400 R 3...
Page 773: ...400 475 AUTOMATIC TRANSMISSION 7A2 13 Figure 29 Internal Parts H H 0 0 4 3 4 0 0 R 2...
Page 797: ...400 475 AUTOMATIC TRANSMISSION 7A2 37 Figure 93 Control Valve Assem bly...
Page 803: ...400 475 AUTOMATIC TRANSMISSION 7A2 43 Figure 104 Bushing Replacement Procedure...
Page 808: ...J c I i sal...
Page 838: ......
Page 840: ......
Page 842: ......
Page 850: ...7B1 12 HM 290 MANUAL TRANSMISSION J i t i a x V L...
Page 856: ...7B1 18 HM 290 MANUAL TRANSMISSION...
Page 892: ...7B1 54 HM 290 MANUAL TRANSMISSION Figure 93 Special Tools...
Page 897: ...HM 117 TRANSMISSION 7B2 5...
Page 901: ...HM 117 TRANSMISSION 7B2 9 B 05180 Figure 17 Installing the 1st and 2nd Synchronizer...
Page 912: ...20 HM...
Page 924: ...7B3 12 NEW PROCESS TRANSMISSION SPECIAL TOOLS...
Page 927: ...BORG WARNER TRANSMISSIONS 7B4 3 Figure 2 77 mm Transmission and Components...
Page 940: ...i ii iii m i in m i...
Page 944: ...7D1 4 TRANSFER CASE FO 5688 Figure 3 NP205 Transfer Case...
Page 952: ...7D1 12 TRANSFER CASE...
Page 963: ...NEW PROCESS 241 TRANSFER CASE 7D2 11 Figure 17 Oil Pump Pickup Screen Doweled Case Holes...
Page 964: ...7D2 12 NEW PROCESS 241 TRANSFER CASE Figure 18 NP 241 Transfer Case Cut Away...
Page 978: ......
Page 981: ...BORG WARNER 1370 TRANSFER CASE 7D4 3 J...
Page 992: ...7D4 14 BORG WARNER 1370 TRANSFER CASE Figure 26 Installing the Rear Output Yoke...
Page 993: ...BORG WARNER 1370 TRANSFER CASE 7D4 15 Figure 27 BW 1370 Transfer Case...
Page 997: ......
Page 998: ...X 8937...