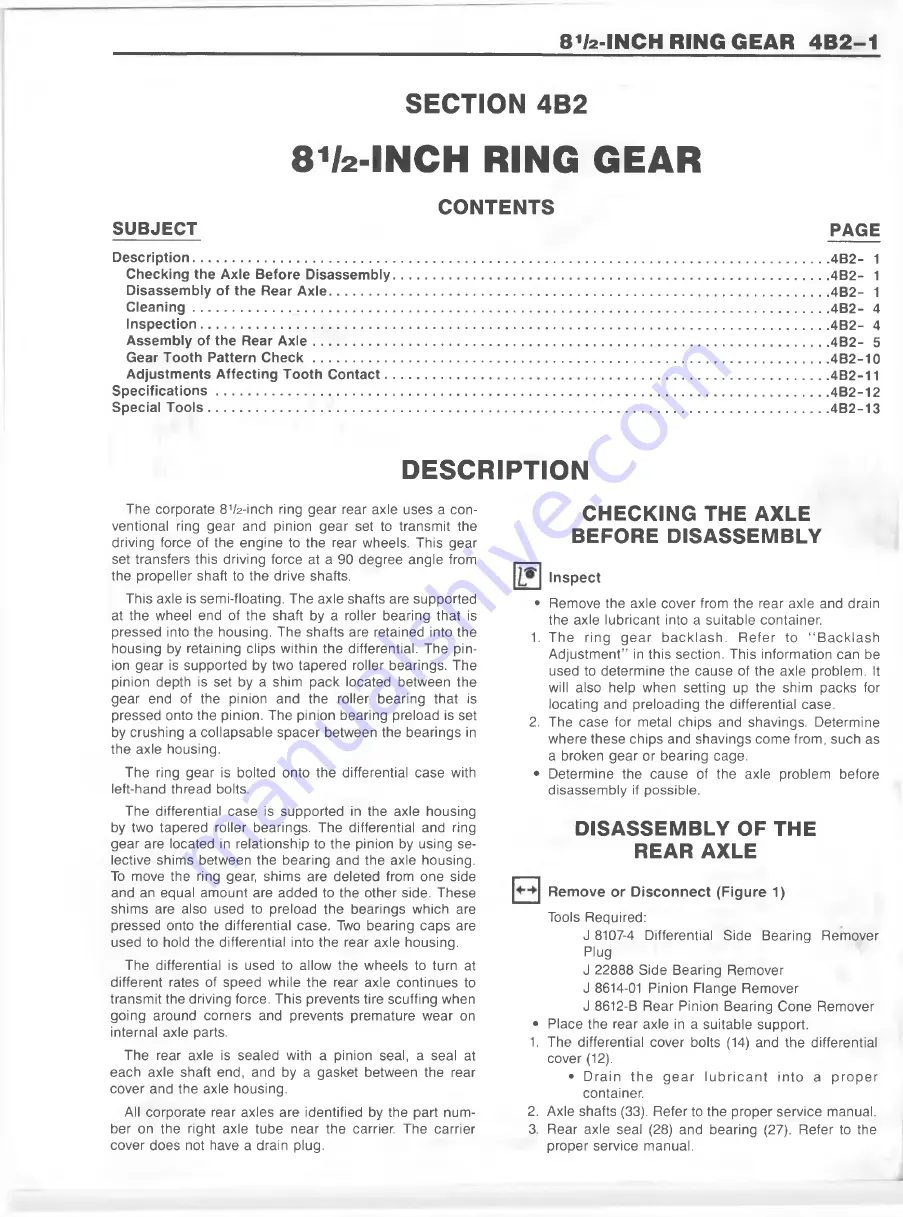
8
V
2
-INCH RING GEAR 4B2-1
SECTION 4B2
8
V
2
-INCH RING GEAR
CONTENTS
S U B J E C T
P A G E
D escription....................................................................................................................................................................................4 B 2 - 1
Checking the Axle Before Disassem bly........................................................................................................................... 4 B 2 - 1
Disassembly of the Rear A x le ............................................................................................................................................. 4 B 2 - 1
C le a n in g .................................................................................................................................................................................... 4 B 2 - 4
Inspectio n ..................................................................................................................................................................................4 B 2 - 4
Assembly of the Rear A x le ..................................................................................................................................................4 B 2 - 5
Gear Tooth Pattern C h e c k ..................................................................................................................................................4 B 2 -1 0
Adjustments Affecting Tooth C o n ta c t............................................................................................................................. 4B2-11
S p e c ific a tio n s ............................................................................................................................................................................. 4 B 2-12
Special T o o ls ............................................................................................................................................................................... 4 B 2-13
DESCRIPTION
The corporate
81
/
2
-inch ring gear rear axle uses a con
ventional ring gear and pinion gear set to transm it the
driving force of the engine to the rear wheels. This gear
set transfers this driving force at a 90 degree angle from
the propeller shaft to the drive shafts.
This axle is semi-floating. The axle shafts are supported
at the wheel end of the shaft by a roller bearing that is
pressed into the housing. The shafts are retained into the
housing by retaining clips within the differential. The pin
ion gear is supported by two tapered roller bearings. The
pinion depth is set by a shim pack located between the
gear end of the pinion and the roller bearing that is
pressed onto the pinion. The pinion bearing preload is set
by crushing a collapsable spacer between the bearings in
the axle housing.
The ring gear is bolted onto the differential case with
left-hand thread bolts.
The differential case is supported in the axle housing
by two tapered roller bearings. The differential and ring
gear are located in relationship to the pinion by using se
lective shims between the bearing and the axle housing.
To move the ring gear, shims are deleted from one side
and an equal amount are added to the other side. These
shims are also used to preload the bearings which are
pressed onto the differential case. Two bearing caps are
used to hold the differential into the rear axle housing.
The differential is used to allow the wheels to turn at
different rates of speed while the rear axle continues to
transm it the driving force. This prevents tire scuffing when
going around corners and prevents premature wear on
internal axle parts.
The rear axle is sealed with a pinion seal, a seal at
each axle shaft end, and by a gasket between the rear
cover and the axle housing.
All corporate rear axles are identified by the part num
ber on the right axle tube near the carrier. The carrier
cover does not have a drain plug.
CHECKING THE AXLE
BEFORE DISASSEMBLY
Inspect
• Remove the axle cover from the rear axle and drain
the axle lubricant into a suitable container.
1. The ring g e a r b a c k la s h . R efer to “ B a cklash
A djustm ent” in this section. This information can be
used to determine the cause of the axle problem. It
will also help when setting up the shim packs for
locating and preloading the differential case.
2
. The case for metal chips and shavings. Determine
where these chips and shavings come from, such as
a broken gear or bearing cage.
• Determine the cause of the axle problem before
disassem bly if possible.
DISASSEMBLY OF THE
REAR AXLE
R em ove or D isco n n ect (Figure 1)
Tools Required:
J 8107-4 Differential Side Bearing Remover
Plug
J 22888 Side Bearing Remover
J 8614-01 Pinion Flange Remover
J 8612-B Rear Pinion Bearing Cone Remover
• Place the rear axle in a suitable support.
1. The differential cover bolts (14) and the differential
cover (
12
).
• D ra in th e g e a r lu b ric a n t in to a p ro p e r
container.
2. Axle shafts (33). Refer to the proper service manual.
3. Rear axle seal (28) and bearing (27). Refer to the
proper service manual.
Summary of Contents for 1989 Light Duty Truck
Page 1: ...vr V Light Duty Truck Unit Repair Manual...
Page 2: ......
Page 11: ...GENERAL INFORMATION OA 5 Figure 8 RV Models...
Page 13: ...GENERAL INFORMATION OA 7 Figure 11 ST Models...
Page 18: ......
Page 44: ......
Page 76: ...1B3 18 R 4 AIR CONDITIONING COMPRESSOR N...
Page 114: ......
Page 162: ......
Page 176: ...4B3 14 91 2 INCH RING GEAR...
Page 192: ...4B5 4 DANA REAR AXLES Figure 4 Spreading the Differential Case Figure 7 Removing the Ring Gear...
Page 218: ......
Page 220: ...4B6 2 12 INCH RING GEAR ROCKWELL F 04734 Figure 1 Rear Axle Components...
Page 229: ...12 INCH RING GEAR ROCKWELL 4B6 11 SPECIAL TOOLS Special Tools...
Page 230: ...4B6 12 12 INCH RING...
Page 240: ...4B7 10 LOCKING DIFFERENTIALS SPECIAL TOOLS Special Tools...
Page 260: ...4C2 6 93 4 INCH RING GEAR FRONT AXLE Figure 16 Removing the Pinion Inner Bearing...
Page 273: ...T TRUCK FRONT AXLE 4C3 3 F 05785 Figure 1 Axle Components...
Page 291: ...K TRUCK FRONT AXLE 4C4 3 Figure 1 Front Axle Com ponents K 15 25 Models...
Page 293: ...K TRUCK FRONT AXLE 4C4 5 Figure 3 Front Axle Com ponents K35 Models...
Page 318: ...C4 30 K TRUCK FBOHT AXLE...
Page 334: ......
Page 361: ...2 5 LITER L4 ENGINE 6A1 5 Figure 3 Cylinder Head Manifolds and Components...
Page 363: ...2 5 LITER L4 ENGINE 6A1 7 F 05715 Figure 5 Block and Components...
Page 395: ...2 8 LITER V 6 6A2 3 Figure 1 Engine Lubrication Diagram...
Page 396: ...6A2 4 2 8 LITER V 6 Figure 2 Engine Lubrication Diagram...
Page 424: ...6A2 32 2 8 LITER V 6...
Page 427: ...I 4 3 LITER V 6 6A3 3 Figure 1 Engine Lubrication Diagram B 07857...
Page 451: ...4 3 LITER V 6 6A3 27 SPECIFICATIONS ENGINE SPECIFICATIONS F 6344...
Page 457: ...4 8 LITER L6 6A4 3 Figure 2 Lubrication Diagram Front View...
Page 460: ...6A4 6 4 8 LITER L6 C 1 107 112 fK 108 3 109 165 129 B 05056 Figure 5 Block and Components...
Page 490: ...Ml...
Page 493: ...V8 ENGINE 6A5 3 Figure 1 Lubrication Diagram 5 0L and 5 7L Engines...
Page 494: ...6A5 4 V8 ENGINE Figure 2 Lubrication Diagram 5 0L and 5 7L Engines...
Page 530: ...6A5 40 V8 ENGINE Figure 81 Exhaust Manifold 7 4L Engines Figure 82 Water Pumps and Components...
Page 571: ...6 2 LITER DIESEL 6A7 35 Figure 58 Vacuum Pump Installed...
Page 576: ......
Page 582: ...6C1 6 MODEL 1MEF CARBURETOR Figure 9 Monojet Model 1MEF...
Page 604: ...6C2 6 MODEL M4MEF CARBURETOR Figure 9 Model M4MEF...
Page 640: ...6C4 8 MODEL 700 THROTTLE BODY...
Page 652: ...nmm...
Page 672: ......
Page 693: ...DISTRIBUTORS 6D5 13 Figure 27 Testing the Pickup Coil Figure 28 Testing the Ignition Coil...
Page 696: ......
Page 698: ...7A1 2 700 R4 AUTOMATIC TRANSMISSION Figure 1 Case and External Parts J H 0 0 5 3 7 0 0 R 4 R 2...
Page 745: ...700 R4 AUTOMATIC TRANSMISSION 7A1 49...
Page 762: ...7A2 2 400 475 AUTOMATIC TRANSMISSION Figure 1 Case and External Parts H H 0021 400 R 3...
Page 773: ...400 475 AUTOMATIC TRANSMISSION 7A2 13 Figure 29 Internal Parts H H 0 0 4 3 4 0 0 R 2...
Page 797: ...400 475 AUTOMATIC TRANSMISSION 7A2 37 Figure 93 Control Valve Assem bly...
Page 803: ...400 475 AUTOMATIC TRANSMISSION 7A2 43 Figure 104 Bushing Replacement Procedure...
Page 808: ...J c I i sal...
Page 838: ......
Page 840: ......
Page 842: ......
Page 850: ...7B1 12 HM 290 MANUAL TRANSMISSION J i t i a x V L...
Page 856: ...7B1 18 HM 290 MANUAL TRANSMISSION...
Page 892: ...7B1 54 HM 290 MANUAL TRANSMISSION Figure 93 Special Tools...
Page 897: ...HM 117 TRANSMISSION 7B2 5...
Page 901: ...HM 117 TRANSMISSION 7B2 9 B 05180 Figure 17 Installing the 1st and 2nd Synchronizer...
Page 912: ...20 HM...
Page 924: ...7B3 12 NEW PROCESS TRANSMISSION SPECIAL TOOLS...
Page 927: ...BORG WARNER TRANSMISSIONS 7B4 3 Figure 2 77 mm Transmission and Components...
Page 940: ...i ii iii m i in m i...
Page 944: ...7D1 4 TRANSFER CASE FO 5688 Figure 3 NP205 Transfer Case...
Page 952: ...7D1 12 TRANSFER CASE...
Page 963: ...NEW PROCESS 241 TRANSFER CASE 7D2 11 Figure 17 Oil Pump Pickup Screen Doweled Case Holes...
Page 964: ...7D2 12 NEW PROCESS 241 TRANSFER CASE Figure 18 NP 241 Transfer Case Cut Away...
Page 978: ......
Page 981: ...BORG WARNER 1370 TRANSFER CASE 7D4 3 J...
Page 992: ...7D4 14 BORG WARNER 1370 TRANSFER CASE Figure 26 Installing the Rear Output Yoke...
Page 993: ...BORG WARNER 1370 TRANSFER CASE 7D4 15 Figure 27 BW 1370 Transfer Case...
Page 997: ......
Page 998: ...X 8937...