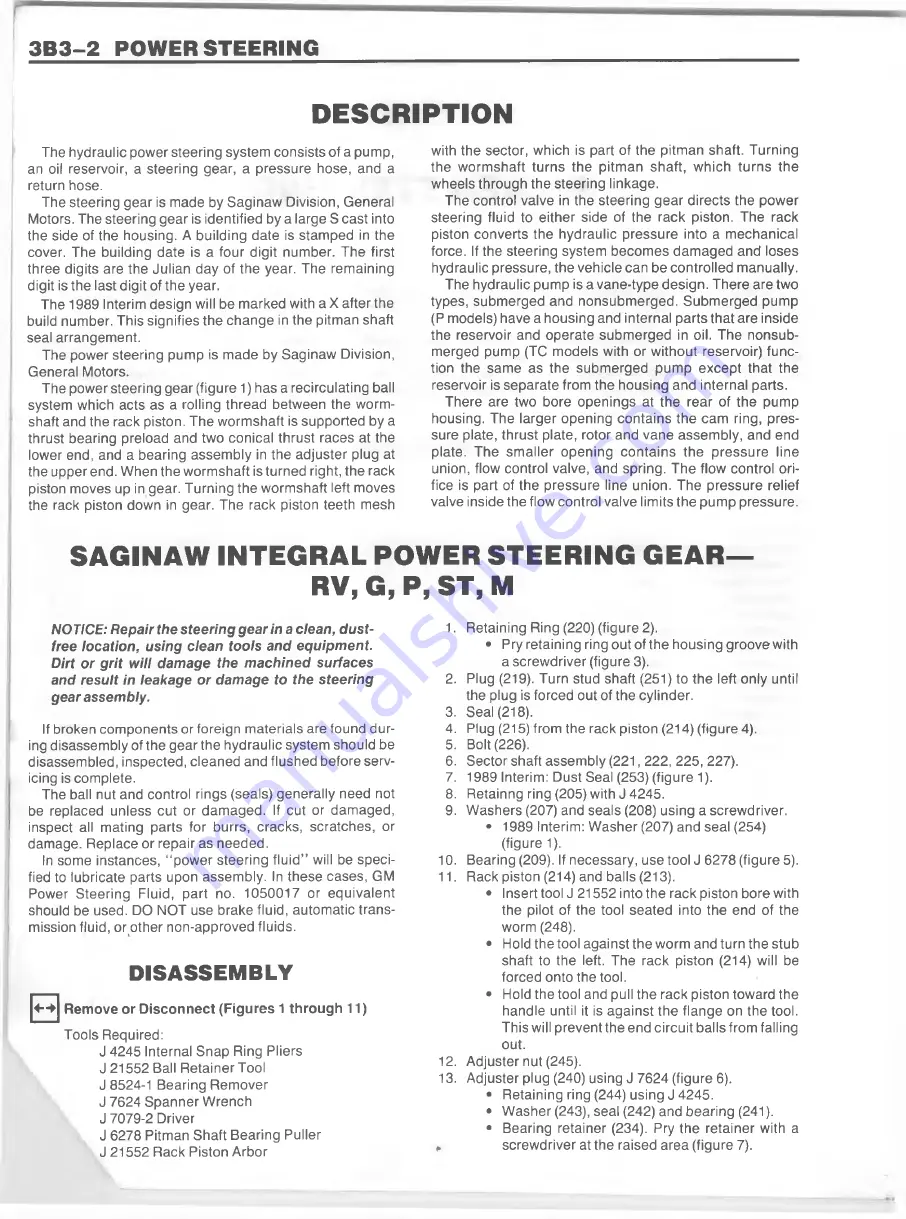
3B3-2 POWER STEERING
DESCRIPTION
The hydraulic power steering system consists of a pump,
an oil reservoir, a steering gear, a pressure hose, and a
return hose.
The steering gear is made by Saginaw Division, General
Motors. The steering gear is identified by a large S cast into
the side of the housing. A building date is stamped in the
cover. The building date is a four digit number. The first
three digits are the Julian day of the year. The remaining
digit is the last digit of the year.
The 1989 Interim design will be marked with a X after the
build number. This signifies the change in the pitman shaft
seal arrangement.
The power steering pump is made by Saginaw Division,
General Motors.
The power steering gear (figure 1) has a recirculating ball
system which acts as a rolling thread between the worm
shaft and the rack piston. The worm shaft is supported by a
thrust bearing preload and two conical thrust races at the
lower end, and a bearing assem bly in the adjuster plug at
the upper end. When the worm shaft is turned right, the rack
piston moves up in gear. Turning the worm shaft left moves
the rack piston down in gear. The rack piston teeth mesh
with the sector, which is part of the pitman shaft. Turning
the w orm shaft turns the pitm an shaft, w hich turns the
wheels through the steering linkage.
The control valve in the steering gear directs the power
steering fluid to either side of the rack piston. The rack
piston converts the hydraulic pressure into a mechanical
force. If the steering system becomes dam aged and loses
hydraulic pressure, the vehicle can be controlled manually.
The hydraulic pump is a vane-type design. There are two
types, submerged and nonsubmerged. Subm erged pump
(P models) have a housing and internal parts that are inside
the reservoir and operate subm erged in oil. The nonsub
merged pump (TC models with or w ithout reservoir) func
tion the same as the subm erged pum p except that the
reservoir is separate from the housing and internal parts.
There are two bore openings at the rear of the pump
housing. The larger opening contains the cam ring, pres
sure plate, thrust plate, rotor and vane assem bly, and end
plate. The sm aller opening contains the pressure line
union, flow control valve, and spring. The flow control ori
fice is part of the pressure line union. The pressure relief
valve inside the flow control valve limits the pum p pressure.
SAGINAW INTEGRAL POWER STEERING GEAR—
RV, G, P, ST, M
NO TIC E: R e p a ir the s te e rin g g e a r in a clean, d ust-
free lo catio n, using c lean tools a n d e q u ip m e n t.
D irt o r g rit w ill d am ag e the m a c h in e d surfaces
an d resu lt in leakag e o r d am ag e to the s teerin g
g e a r assem bly.
If broken com ponents or foreign m aterials are found dur
ing disassembly of the gear the hydraulic system should be
disassembled, inspected, cleaned and flushed before serv
icing is complete.
The ball nut and control rings (seals) generally need not
be replaced unless cut or dam aged. If cut or damaged,
inspect all mating parts for burrs, cracks, scratches, or
damage. Replace or repair as needed.
In some instances, “ power steering flu id ” will be speci
fied to lubricate parts upon assembly. In these cases, GM
Power Steering Fluid, part no. 1050017 or equivalent
should be used. DO NOT use brake fluid, automatic trans
mission fluid, or other non-approved fluids.
DISASSEMBLY
0
Remove or Disconnect (Figures 1 through 11)
Tools Required:
J 4245 Internal Snap Ring Pliers
J 21552 Ball Retainer Tool
J 8524-1 Bearing Remover
J 7624 Spanner W rench
J 7079-2 Driver
J 6278 Pitman Shaft Bearing Puller
J 21552 Rack Piston Arbor
1. Retaining Ring (220) (figure 2).
• Pry retaining ring out of the housing groove with
a screwdriver (figure 3).
2. Plug (219). Turn stud shaft (251) to the left only until
the plug is forced out of the cylinder.
3. Seal (218).
4. Plug (215) from the rack piston (214) (figure 4).
5. Bolt (226).
6. Sector shaft assem bly (221, 222, 225, 227).
7. 1989 Interim: Dust Seal (253) (figure 1).
8. Retainng ring (205) with J 4245.
9. W ashers (207) and seals (208) using a screwdriver.
• 1989 Interim: W asher (207) and seal (254)
(figure 1).
10. Bearing (209). If necessary, use tool J 6278 (figure 5).
11. Rack piston (214) and balls (213).
• Insert tool J 21552 into the rack piston bore with
the pilot of the tool seated into the end of the
worm (248).
• Hold the tool against the worm and turn the stub
shaft to the left. The rack piston (214) will be
forced onto the tool.
• Hold the tool and pull the rack piston toward the
handle until it is against the flange on the tool.
This will prevent the end circuit balls from falling
out.
12. Adjuster nut (245).
13. Adjuster plug (240) using J 7624 (figure 6).
• Retaining ring (244) using J 4245.
• W asher (243), seal (242) and bearing (241).
• Bearing retainer (234). Pry the retainer with a
t
screw driver at the raised area (figure 7).
Summary of Contents for 1989 Light Duty Truck
Page 1: ...vr V Light Duty Truck Unit Repair Manual...
Page 2: ......
Page 11: ...GENERAL INFORMATION OA 5 Figure 8 RV Models...
Page 13: ...GENERAL INFORMATION OA 7 Figure 11 ST Models...
Page 18: ......
Page 44: ......
Page 76: ...1B3 18 R 4 AIR CONDITIONING COMPRESSOR N...
Page 114: ......
Page 162: ......
Page 176: ...4B3 14 91 2 INCH RING GEAR...
Page 192: ...4B5 4 DANA REAR AXLES Figure 4 Spreading the Differential Case Figure 7 Removing the Ring Gear...
Page 218: ......
Page 220: ...4B6 2 12 INCH RING GEAR ROCKWELL F 04734 Figure 1 Rear Axle Components...
Page 229: ...12 INCH RING GEAR ROCKWELL 4B6 11 SPECIAL TOOLS Special Tools...
Page 230: ...4B6 12 12 INCH RING...
Page 240: ...4B7 10 LOCKING DIFFERENTIALS SPECIAL TOOLS Special Tools...
Page 260: ...4C2 6 93 4 INCH RING GEAR FRONT AXLE Figure 16 Removing the Pinion Inner Bearing...
Page 273: ...T TRUCK FRONT AXLE 4C3 3 F 05785 Figure 1 Axle Components...
Page 291: ...K TRUCK FRONT AXLE 4C4 3 Figure 1 Front Axle Com ponents K 15 25 Models...
Page 293: ...K TRUCK FRONT AXLE 4C4 5 Figure 3 Front Axle Com ponents K35 Models...
Page 318: ...C4 30 K TRUCK FBOHT AXLE...
Page 334: ......
Page 361: ...2 5 LITER L4 ENGINE 6A1 5 Figure 3 Cylinder Head Manifolds and Components...
Page 363: ...2 5 LITER L4 ENGINE 6A1 7 F 05715 Figure 5 Block and Components...
Page 395: ...2 8 LITER V 6 6A2 3 Figure 1 Engine Lubrication Diagram...
Page 396: ...6A2 4 2 8 LITER V 6 Figure 2 Engine Lubrication Diagram...
Page 424: ...6A2 32 2 8 LITER V 6...
Page 427: ...I 4 3 LITER V 6 6A3 3 Figure 1 Engine Lubrication Diagram B 07857...
Page 451: ...4 3 LITER V 6 6A3 27 SPECIFICATIONS ENGINE SPECIFICATIONS F 6344...
Page 457: ...4 8 LITER L6 6A4 3 Figure 2 Lubrication Diagram Front View...
Page 460: ...6A4 6 4 8 LITER L6 C 1 107 112 fK 108 3 109 165 129 B 05056 Figure 5 Block and Components...
Page 490: ...Ml...
Page 493: ...V8 ENGINE 6A5 3 Figure 1 Lubrication Diagram 5 0L and 5 7L Engines...
Page 494: ...6A5 4 V8 ENGINE Figure 2 Lubrication Diagram 5 0L and 5 7L Engines...
Page 530: ...6A5 40 V8 ENGINE Figure 81 Exhaust Manifold 7 4L Engines Figure 82 Water Pumps and Components...
Page 571: ...6 2 LITER DIESEL 6A7 35 Figure 58 Vacuum Pump Installed...
Page 576: ......
Page 582: ...6C1 6 MODEL 1MEF CARBURETOR Figure 9 Monojet Model 1MEF...
Page 604: ...6C2 6 MODEL M4MEF CARBURETOR Figure 9 Model M4MEF...
Page 640: ...6C4 8 MODEL 700 THROTTLE BODY...
Page 652: ...nmm...
Page 672: ......
Page 693: ...DISTRIBUTORS 6D5 13 Figure 27 Testing the Pickup Coil Figure 28 Testing the Ignition Coil...
Page 696: ......
Page 698: ...7A1 2 700 R4 AUTOMATIC TRANSMISSION Figure 1 Case and External Parts J H 0 0 5 3 7 0 0 R 4 R 2...
Page 745: ...700 R4 AUTOMATIC TRANSMISSION 7A1 49...
Page 762: ...7A2 2 400 475 AUTOMATIC TRANSMISSION Figure 1 Case and External Parts H H 0021 400 R 3...
Page 773: ...400 475 AUTOMATIC TRANSMISSION 7A2 13 Figure 29 Internal Parts H H 0 0 4 3 4 0 0 R 2...
Page 797: ...400 475 AUTOMATIC TRANSMISSION 7A2 37 Figure 93 Control Valve Assem bly...
Page 803: ...400 475 AUTOMATIC TRANSMISSION 7A2 43 Figure 104 Bushing Replacement Procedure...
Page 808: ...J c I i sal...
Page 838: ......
Page 840: ......
Page 842: ......
Page 850: ...7B1 12 HM 290 MANUAL TRANSMISSION J i t i a x V L...
Page 856: ...7B1 18 HM 290 MANUAL TRANSMISSION...
Page 892: ...7B1 54 HM 290 MANUAL TRANSMISSION Figure 93 Special Tools...
Page 897: ...HM 117 TRANSMISSION 7B2 5...
Page 901: ...HM 117 TRANSMISSION 7B2 9 B 05180 Figure 17 Installing the 1st and 2nd Synchronizer...
Page 912: ...20 HM...
Page 924: ...7B3 12 NEW PROCESS TRANSMISSION SPECIAL TOOLS...
Page 927: ...BORG WARNER TRANSMISSIONS 7B4 3 Figure 2 77 mm Transmission and Components...
Page 940: ...i ii iii m i in m i...
Page 944: ...7D1 4 TRANSFER CASE FO 5688 Figure 3 NP205 Transfer Case...
Page 952: ...7D1 12 TRANSFER CASE...
Page 963: ...NEW PROCESS 241 TRANSFER CASE 7D2 11 Figure 17 Oil Pump Pickup Screen Doweled Case Holes...
Page 964: ...7D2 12 NEW PROCESS 241 TRANSFER CASE Figure 18 NP 241 Transfer Case Cut Away...
Page 978: ......
Page 981: ...BORG WARNER 1370 TRANSFER CASE 7D4 3 J...
Page 992: ...7D4 14 BORG WARNER 1370 TRANSFER CASE Figure 26 Installing the Rear Output Yoke...
Page 993: ...BORG WARNER 1370 TRANSFER CASE 7D4 15 Figure 27 BW 1370 Transfer Case...
Page 997: ......
Page 998: ...X 8937...