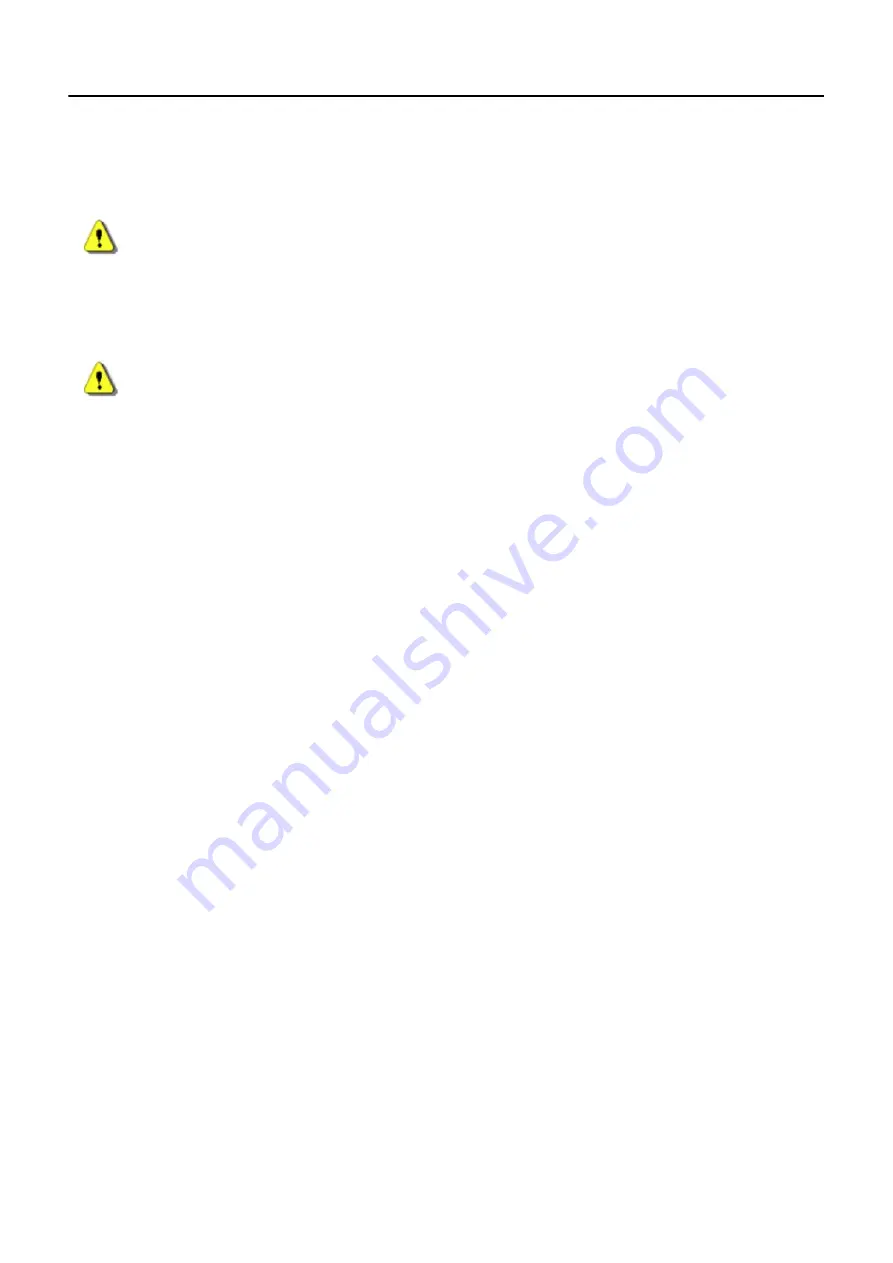
Chapter 14: Quality Assurance and Maintenance
5495975-1EN Rev.9
14-16
© 2013-2017 General Electric Company. All rights reserved.
Aside from routine maintenance, any abnormal noise, vibration or unusual performance should be
reported immediately to a GE representative. Before calling for service, however, be sure the equipment
is being operated in accordance with the foregoing instructions.
WARNING
Failure to perform the periodic inspection and maintenance could allow deterio-
rating conditions to develop without being detected. This deterioration could
result in equipment failures which could cause serious injury or equipment dam-
age.
WARNING
Electric shock hazard! The OTS suspension contains no user serviceable compo-
nents. Do not attempt to disable these components or remove any trim covers.
Refer service to qualified personnel.
Qualified Service
Safe equipment performance also requires the use of service personnel specially trained on the medical
x–ray apparatus. GE and its associates, maintain a world–wide organization of stations from which one
may obtain skilled x–ray service. If desired, arrangements can usually be made to furnish periodic and/
or emergency service on a contract basis. A GE representative will be glad to discuss this plan.
The system should have an expected service life of 10 years. Periodic maintenance of the system is
required to maintain the system lifecycle. The first periodic maintenance shall be implemented after the
first 6 months of use. Then it is suggested to do periodic maintenance by a GE qualified service engineer
according to Planned Maintenance schedule.
General Cleaning and Disinfecting
This equipment should be cleaned frequently, particularly if corroding chemicals are present. Use a cloth
moistened in warm soapy water (use mild soap) to clean the trim and nameplate of the Operator’s Con-
trols. Wipe with a cloth moistened in clean water. Do not use cleaners or solvents of any kind as they may
dull the finish or blur the lettering. Polish with a pure liquid or paste wax. Other surfaces of the equipment
can be cleaned using a clean cloth moistened slightly with a good mild cleaner and polish acceptable for
use on enameled metal surfaces. Before each use, equipment surfaces that contact the patient should
be cleaned with an EPA registered, low-level disinfection or sanitizing agent.
For general cleaning of Table and Wallstand plastic and patient barrier surfaces use a soft non-lint cloth
moistened with Ethanol (ethyl alcohol 95% minimum). For OTS plastic handle the chemical used should
be of a pH between 7 to 9.
Never use cleaners or solvents of any kind if you are uncertain of the nature of the cleaning agent.