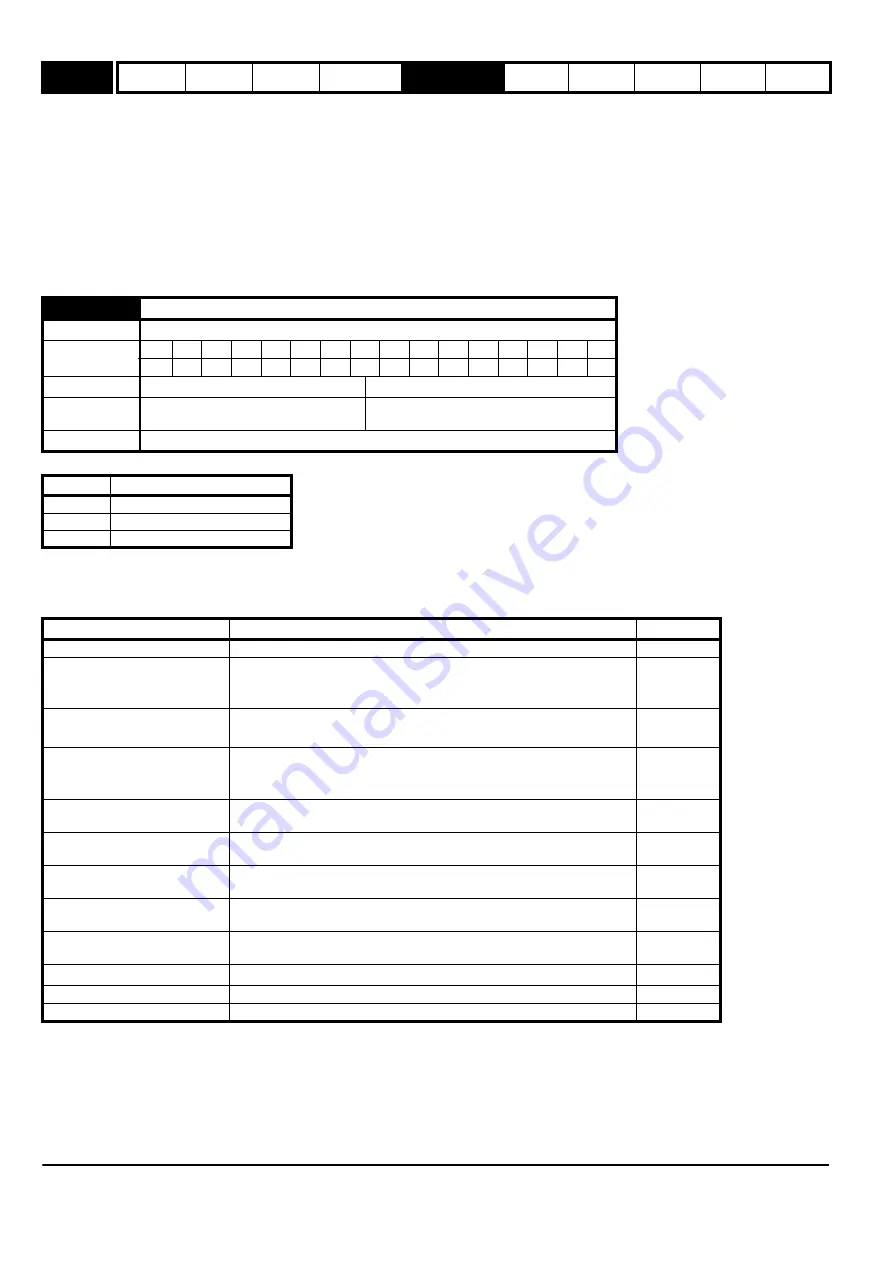
Menu 3
All modes
Parameter
structure
Keypad and
display
Parameter
x.00
Parameter
description format
Advanced parameter
descriptions
Macros
Serial comms
protocol
Electronic
nameplate
Performance RFC mode
74
Unidrive SP Advanced User Guide
www.controltechniques.com Issue Number: 10
This problem should not occur with EnDat encoders because three consecutive corrupted messages at the slowest sample rate (i.e. 25
μ
s) would be
required even at the maximum speed of 40,000rpm before the change of position would be the required 0.5 turns to give possible corruption of the
turns information. If three consecutive messages with CRC errors occur this will cause the drive to produce an Enc5 trip. The drive can only be re-
enabled after the trip is reset which will re-initialize the encoder and correct the absolute turns.
If an SSI encoder is used, but is not powered from the drive, and the encoder is powered up after the drive, it is possible that the first change of
position detected could be large enough to cause the problem described above. This can be avoided if the encoder interface is initialized via Pr
3.47
after the encoder has powered up. If the encoder includes a bit that indicates the status of the power supply the power supply monitor should be
enabled (see Pr
3.40
). This will ensure that the drive remains tripped until the encoder is powered up and the action of resetting the trip will reinitialise
the encoder interface.
If the position feedback device is EnDat it is possible for the drive to set up this parameter automatically from information obtained from the encoder
(see Pr
3.41
).
Trips can be enabled/disabled using Pr
3.40
as follows.
Encoder trips
The following table shows trips that can be initiated that are related to the drive encoder feedback and whether they can be enabled and disabled by
Pr
3.40
.
3.40
Drive encoder error detection level
Drive modes
Open-loop, Closed-loop vector, Servo
Coding
Bit
SP
FI
DE Txt VM DP ND RA NC NV
PT
US RW BU PS
1
1
1
Range
Open-loop, Closed-loop vector, Servo
0 to 7
Default
Open-loop
Closed-loop vector, Servo
0
1
Update rate
Background read
Bit
Function
0
Wire break detect
1
Phase error detect
2
SSI power supply bit monitor
Encoders
Reason for error
Drive trip
All
Power supply short circuit
Enc1
Ab, Fd, Fr, Ab.Servo, Fd.Servo,
Fr.Servo,
SC, SC.Hiper, SC.EnDat, SC.SSI
+Hardware wire-break detect on A, B and Z inputs
(1)
Software wire break detection on sine wave signals
There is no wire break detection on the U, V and W commutation inputs
Enc2
Ab.Servo, Fd.Servo, Fr.Servo
SC.Hiper, SC.EnDat, SC.SSI
+Phase error
(2)
+Sine/cosine phase error
(3)
Enc3
SC.Hiper, SC.EnDat, SC.SSI
EnDat
SSI
Comms failure (timeout)
(5)
Comms failure (timeout) or transfer time too long
Comms transfer time is too long
Enc4
SC.Hiper, SC.EnDat, EnDat
Checksum/CRC error or SSI not ready at start of position transfer (i.e. data
input not one)
Enc5
SC.Hiper, SC.EnDat, EnDat
SSI, SC.SSI
The encoder has indicated an error
+Power supply failure
Enc6
SC, SC.Hiper, SC.EnDat,
SC.SSI, EnDat, SSI
Initialisation has failed due to a comms error.
Enc7
SC.Hiper, SC.EnDat, EnDat
Auto-configuration has been requested by changing Pr
3.41
, but an
initialisation has not occurred to perform auto-configuration.
Enc8
All
Speed feedback selected from an option slot that does not have a position
feedback category Solutions Module installed
Enc9
All (Servo mode only)
Incorrect encoder phasing
(4)
Enc10
SC, SC.Hiper, SC.EnDat, SC.SSI Failure of analog position alignment during encoder initialisation
Enc11
SC.Hiper
The encoder type could not be identified during auto-configuration
Enc12
Summary of Contents for unidrive sp
Page 419: ......
Page 420: ...0471 0002 10 ...